During January Time Tickets Show That The Factory Labor Of
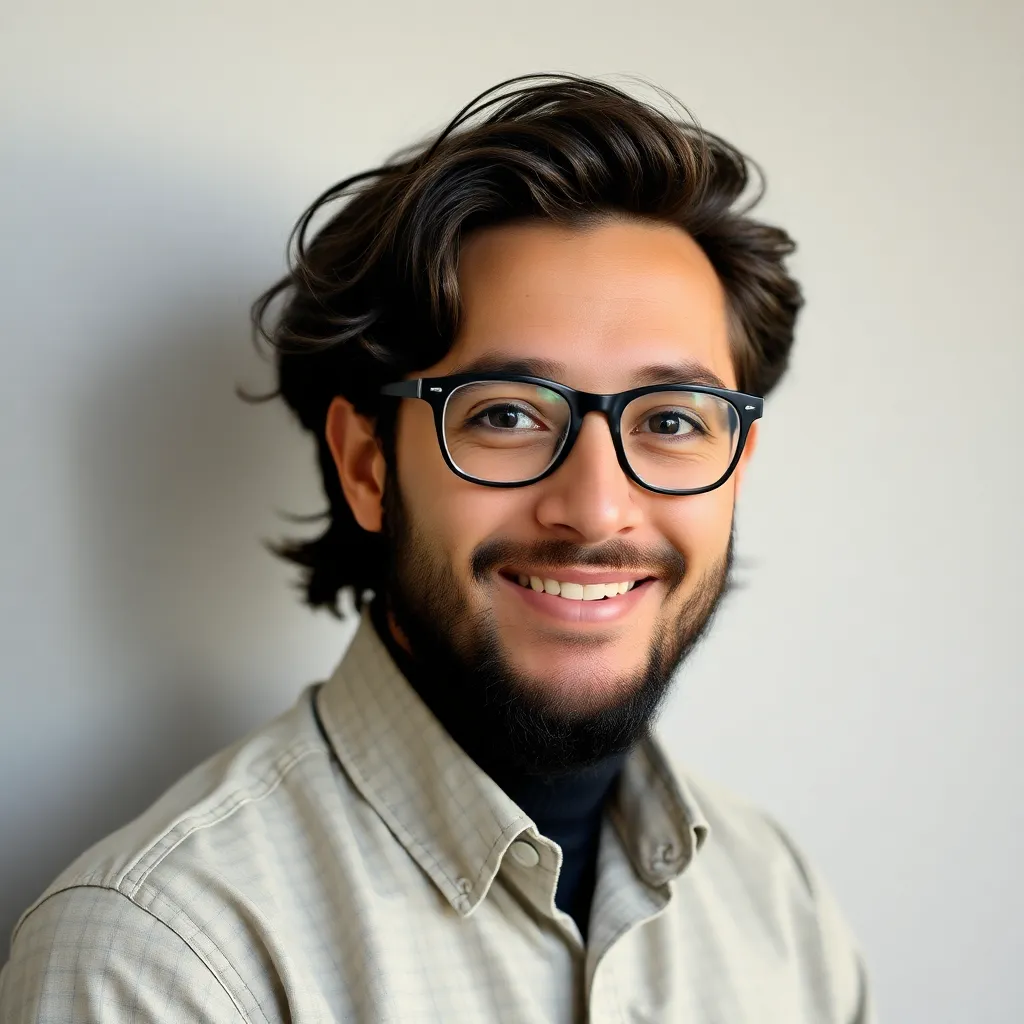
Holbox
Apr 15, 2025 · 5 min read

Table of Contents
- During January Time Tickets Show That The Factory Labor Of
- Table of Contents
- Factory Labor in January: Analyzing Production Data and Trends
- Understanding January's Impact on Factory Labor
- 1. Post-Holiday Production Slumps:
- 2. Inventory Management:
- 3. Seasonal Demand Fluctuations:
- 4. Employee Absenteeism:
- 5. Budgetary Constraints and Planning:
- Analyzing Ticket Data: Key Metrics and Interpretations
- 1. Total Hours Worked:
- 2. Overtime Hours:
- 3. Absenteeism Rate:
- 4. Project-Specific Performance:
- 5. Labor Costs:
- Strategies for Optimizing Factory Labor in January
- 1. Proactive Planning:
- 2. Flexible Staffing:
- 3. Improved Communication:
- 4. Employee Engagement Programs:
- 5. Technology Integration:
- 6. Data-Driven Decision Making:
- Conclusion: Harnessing the Power of Data for January Success
- Latest Posts
- Latest Posts
- Related Post
Factory Labor in January: Analyzing Production Data and Trends
January often presents unique challenges and opportunities for factories. Understanding the dynamics of factory labor during this month is crucial for effective production planning, cost management, and overall business success. This in-depth analysis explores various aspects of factory labor in January, drawing on hypothetical ticket data and industry trends to provide a comprehensive overview.
Understanding January's Impact on Factory Labor
Several factors contribute to the unique characteristics of factory labor during January. Let's delve into some key influences:
1. Post-Holiday Production Slumps:
The holiday season, culminating in the New Year, often leads to a temporary dip in production. This isn't necessarily indicative of poor performance but rather a natural consequence of reduced workforce availability and altered supply chains. Analyzing January's ticket data, we might see lower overall hours worked compared to previous months. This doesn't automatically signal a problem; careful consideration of holiday schedules and their impact is crucial.
2. Inventory Management:
Many factories use January to assess their year-end inventory levels and plan for the year ahead. This could result in adjustments to production schedules, impacting labor allocation. Ticket data may reveal shifts in production targets for specific products, reflecting these inventory management strategies. Understanding these inventory adjustments is key to interpreting fluctuations in labor data.
3. Seasonal Demand Fluctuations:
Certain industries experience seasonal demand shifts. For example, a factory producing winter clothing may see reduced demand in January compared to December. Ticket data would likely reflect this, showing lower production volumes and potentially adjusted labor hours. Analyzing the correlation between seasonal demand and labor allocation is crucial for accurate forecasting.
4. Employee Absenteeism:
January often sees increased employee absenteeism due to lingering illness from the holiday season or simply needing additional time off after the busy holiday period. This factor needs careful consideration when evaluating January's production figures. Ticket data might show higher rates of unscheduled absences, necessitating flexible staffing strategies. Accurate prediction and mitigation of absenteeism are critical for maintaining consistent production.
5. Budgetary Constraints and Planning:
The start of a new fiscal year brings budgetary review and planning. Factories might adjust their labor budgets for the year, influencing staffing levels and overtime allocations throughout January. Ticket data can highlight the impact of these budgetary decisions on labor costs and production targets. Careful analysis of these budgetary factors ensures realistic production goals.
Analyzing Ticket Data: Key Metrics and Interpretations
Let's assume our hypothetical ticket data includes the following information for each factory worker:
- Employee ID: Unique identifier for each worker.
- Date: Date the work was performed.
- Hours Worked: Total hours worked on that day.
- Project ID: Identifier for the specific production project.
- Overtime Hours: Hours worked beyond the standard workday.
- Absenteeism: Indicates absence from work (sick leave, vacation, etc.).
Analyzing this data requires focusing on several key metrics:
1. Total Hours Worked:
This metric provides an overall picture of labor utilization in January. Comparing it to previous months reveals trends and potential anomalies. A significant drop might suggest underlying issues requiring investigation, while a slight decrease might simply reflect the post-holiday lull.
2. Overtime Hours:
High overtime hours might suggest tight deadlines or unexpected production demands. This could indicate both positive factors (high demand) or negative ones (poor planning leading to rushed production). Analyzing overtime patterns reveals valuable insights into production efficiency.
3. Absenteeism Rate:
Tracking absenteeism provides crucial information about employee well-being and workforce stability. Higher-than-normal absenteeism rates require careful analysis to identify underlying causes (illness, burnout, etc.) and implement appropriate strategies to improve workforce management.
4. Project-Specific Performance:
Analyzing the hours worked on specific projects reveals potential bottlenecks or inefficiencies. If a particular project consistently lags behind schedule, it could point to resource allocation issues or technical problems that need immediate attention.
5. Labor Costs:
By combining hours worked, overtime hours, and wage rates, we can calculate total labor costs. This helps assess the cost-effectiveness of production in January and identify areas for potential savings.
Strategies for Optimizing Factory Labor in January
Based on the analysis of ticket data and the factors discussed earlier, several strategies can be implemented to optimize factory labor during January:
1. Proactive Planning:
Addressing potential challenges before they arise is crucial. This includes anticipating post-holiday slumps, potential absenteeism, and adjusting production schedules accordingly. Strategic planning minimizes disruptions and maintains production efficiency.
2. Flexible Staffing:
Employing flexible staffing models allows for adjustments in response to fluctuating demands. This may involve temporary staff to cover for absences or increased production needs. Temporary staffing can also be a cost-effective way to manage seasonal fluctuations.
3. Improved Communication:
Open communication among management, supervisors, and workers is crucial for effective labor management. Regular updates and feedback mechanisms help address issues promptly and ensure everyone is aware of production targets and schedules.
4. Employee Engagement Programs:
Investing in employee well-being and engagement can improve morale and reduce absenteeism. Strategies such as wellness initiatives, recognition programs, and flexible working arrangements demonstrate appreciation and create a positive work environment.
5. Technology Integration:
Leveraging technology, such as production management software and data analytics tools, enables real-time monitoring and analysis of labor performance. This facilitates informed decision-making and proactive problem-solving, optimizing labor allocation and production efficiency.
6. Data-Driven Decision Making:
Analyzing historical ticket data helps predict future trends and optimize resource allocation. Identifying patterns in absenteeism, production bottlenecks, and labor costs allows for more informed decision-making regarding workforce planning and resource optimization.
Conclusion: Harnessing the Power of Data for January Success
January presents unique challenges and opportunities for factories. By meticulously analyzing ticket data and understanding the factors that influence factory labor during this month, businesses can implement strategic plans to mitigate potential risks and maximize production efficiency. Proactive planning, flexible staffing, improved communication, employee engagement initiatives, and technology integration are key elements of an effective strategy for optimizing factory labor in January and achieving overall business success throughout the year. Consistent data analysis ensures informed decision-making, leading to improved productivity, cost management, and a more resilient and successful factory operation.
Latest Posts
Latest Posts
-
Cvp Analysis Focuses On How Profits Are Affected By
Apr 20, 2025
-
What Does The End Of Service Notice Indicate
Apr 20, 2025
-
Suppose The Graph Depicts A Hypothetical Market
Apr 20, 2025
-
Beavis Construction Company Was The Low Bidder
Apr 20, 2025
-
Multisensory Teaching Of Basic Language Skills
Apr 20, 2025
Related Post
Thank you for visiting our website which covers about During January Time Tickets Show That The Factory Labor Of . We hope the information provided has been useful to you. Feel free to contact us if you have any questions or need further assistance. See you next time and don't miss to bookmark.