Determine The Magnitude Of The Pin Force At A
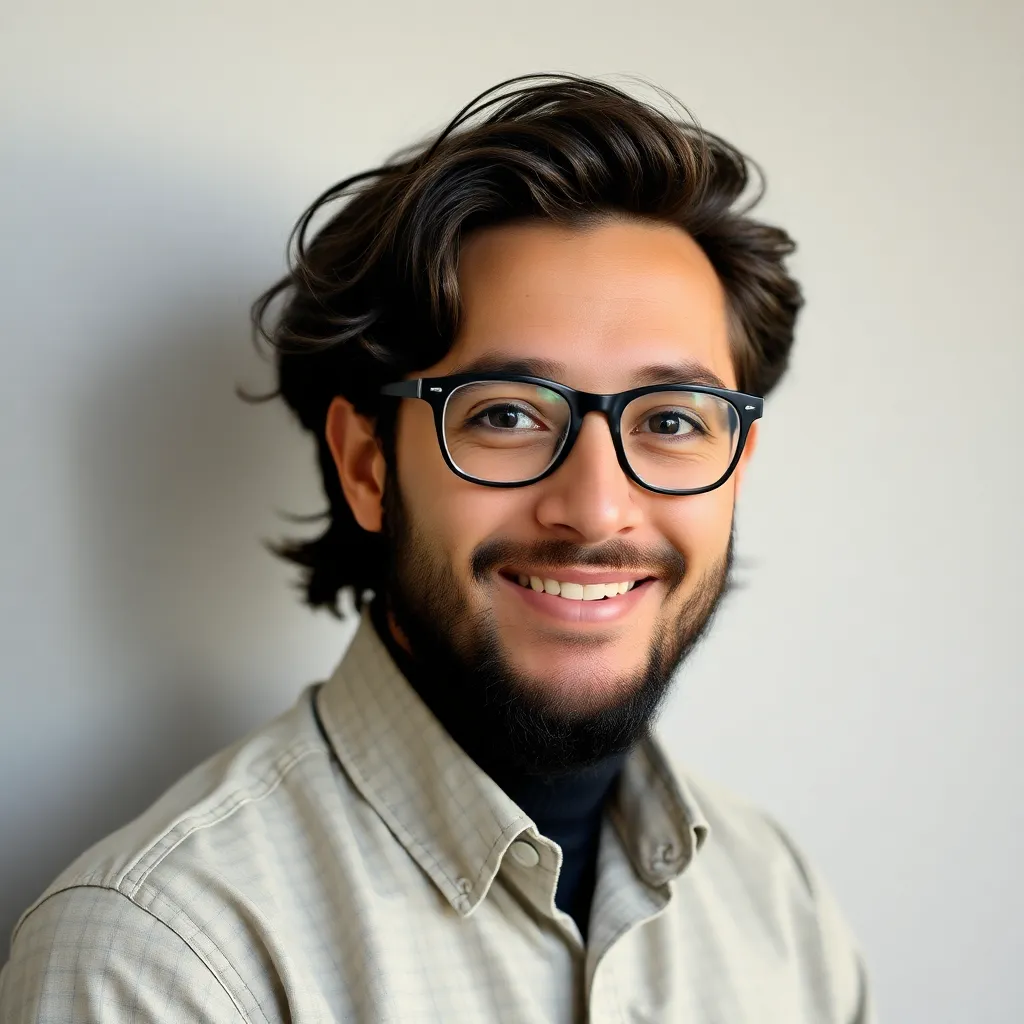
Holbox
Mar 27, 2025 · 6 min read
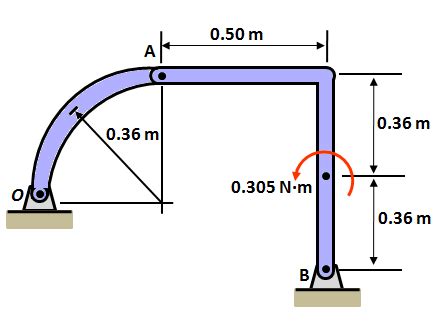
Table of Contents
- Determine The Magnitude Of The Pin Force At A
- Table of Contents
- Determining the Magnitude of Pin Forces: A Comprehensive Guide
- Understanding Pin Connections and Force Transmission
- Types of Pin Connections
- Methods for Determining Pin Force Magnitude
- 1. Method of Joints (Graphical Method)
- 2. Method of Sections (Graphical Method)
- 3. Method of Joints (Analytical Method)
- 4. Method of Sections (Analytical Method)
- 5. Finite Element Analysis (FEA)
- Practical Considerations and Factors Influencing Pin Force Magnitude
- Conclusion
- Latest Posts
- Latest Posts
- Related Post
Determining the Magnitude of Pin Forces: A Comprehensive Guide
Determining the magnitude of pin forces is a crucial aspect of structural analysis, particularly in machine design and construction engineering. Pins are essential connecting elements that transmit forces between components, and understanding the forces acting on them is paramount for ensuring structural integrity and preventing failure. This comprehensive guide will delve into various methods for determining pin forces, covering both theoretical approaches and practical considerations.
Understanding Pin Connections and Force Transmission
Before diving into calculation methods, it's essential to grasp the fundamentals of pin connections and how forces are transmitted. Pin connections, also known as hinge connections, are typically used to allow for relative rotation between connected members while resisting forces in other directions. The pin itself acts as a point of constraint, transferring forces from one member to another.
Types of Pin Connections
Pin connections can be broadly classified into several types, depending on the arrangement and number of pins involved:
- Single Shear Pin: The pin is subjected to shear force on one plane.
- Double Shear Pin: The pin is subjected to shear force on two planes. This configuration generally results in a higher load-carrying capacity.
- Multiple Pin Connections: Structures can utilize multiple pins to distribute loads and enhance stability.
The type of pin connection significantly influences the calculation of pin forces.
Methods for Determining Pin Force Magnitude
Several methods can be employed to determine the magnitude of pin forces. The choice of method depends on factors such as the complexity of the structure, the type of loading, and the available information.
1. Method of Joints (Graphical Method)
This method is particularly useful for analyzing simple truss structures. It involves analyzing the equilibrium of forces at each pin joint. By considering the equilibrium of forces in the x and y directions, we can solve for the unknown pin forces.
Steps:
- Free Body Diagram: Create a free body diagram of the entire structure.
- Isolate Joints: Isolate each joint and draw a free body diagram showing all forces acting on it.
- Equilibrium Equations: Apply the equilibrium equations (ΣFx = 0 and ΣFy = 0) to each joint.
- Solve for Unknown Forces: Solve the resulting system of equations for the unknown pin forces.
Advantages:
- Relatively simple to understand and apply for simple trusses.
- Provides a clear visual representation of forces.
Disadvantages:
- Can become cumbersome for complex structures with many joints.
- Graphical approach can lead to inaccuracies.
2. Method of Sections (Graphical Method)
This method is applicable to truss structures and involves cutting the truss into sections to analyze the forces in specific members. It is often faster than the method of joints for determining forces in particular members without having to analyze every joint.
Steps:
- Section the Truss: Cut the truss through the members whose forces you want to determine.
- Free Body Diagram: Create a free body diagram of one of the sections.
- Equilibrium Equations: Apply the equilibrium equations to the section.
- Solve for Unknown Forces: Solve the resulting equations to find the forces in the members of interest.
Advantages:
- Efficient for determining forces in specific members without analyzing every joint.
- Can reduce the number of equations to be solved.
Disadvantages:
- Only useful for truss structures.
- Requires careful selection of the section.
3. Method of Joints (Analytical Method)
This is an algebraic approach to the method of joints, offering higher precision compared to its graphical counterpart. This method involves applying the equilibrium equations to each joint, systematically solving for unknown forces. The process typically involves constructing a system of equations and then using matrix methods or substitution to arrive at solutions.
Advantages:
- More precise than the graphical method.
- Suitable for complex structures where manual graphical solutions are impractical.
Disadvantages:
- Can become complex for large structures, requiring substantial computational resources.
4. Method of Sections (Analytical Method)
Similar to the graphical approach, the analytical method of sections applies the principles of static equilibrium to a sectioned part of the structure, but uses algebraic equations rather than graphical representations to solve for the unknown pin forces. This is typically done by isolating a portion of the structure and writing equations for the sum of forces in the x and y directions, and the sum of moments about a point.
Advantages:
- More precise than the graphical method.
- Can be easily implemented using computational tools.
Disadvantages:
- Requires a good understanding of statics principles.
- Can lead to complex algebraic solutions for intricate structures.
5. Finite Element Analysis (FEA)
For complex structures with intricate geometries and loading conditions, Finite Element Analysis (FEA) is an indispensable tool. FEA divides the structure into numerous smaller elements, enabling accurate stress and force distribution analysis. This method excels in handling non-linear behaviors and complex material properties. Software packages dedicated to FEA automate the process, making it efficient and precise.
Advantages:
- Can handle complex geometries and loading conditions.
- Accounts for non-linear behavior and complex material properties.
- Provides detailed stress and strain distributions.
Disadvantages:
- Requires specialized software and expertise.
- Can be computationally intensive for very large models.
Practical Considerations and Factors Influencing Pin Force Magnitude
Several factors beyond the theoretical calculations can influence the actual magnitude of pin forces:
- Material Properties: The material strength and yield stress of the pin significantly impact its load-carrying capacity. A stronger material can withstand higher forces before failure.
- Manufacturing Tolerances: Imperfections in the manufacturing process can lead to variations in pin dimensions and alignment, affecting the force distribution.
- Friction: Friction between the pin and the connected members can influence the force distribution, particularly in situations with significant relative movement.
- Dynamic Loading: Dynamic loads (like vibrations or impacts) can substantially increase the forces acting on pins compared to static loading conditions. This necessitates using dynamic analysis methods.
- Corrosion: Corrosion can weaken the pin material, reducing its load-bearing capacity and increasing the risk of failure.
- Fatigue: Repeated cyclic loading can lead to fatigue failure even at loads significantly below the ultimate tensile strength. Fatigue analysis is necessary for applications with repeated loading.
Conclusion
Determining the magnitude of pin forces is essential for ensuring the safety and reliability of structures. The appropriate method for calculating these forces depends on the complexity of the structure and the desired accuracy. While simpler methods like the method of joints and sections are sufficient for basic structures, FEA offers a powerful tool for analyzing intricate designs. Furthermore, practical factors like material properties, manufacturing tolerances, and loading conditions must be considered to obtain a realistic assessment of pin forces and to design robust and safe structures. Remember, thorough analysis and careful consideration of these factors are crucial in preventing structural failure and ensuring the longevity of engineering projects.
Latest Posts
Latest Posts
-
When Derivatively Classifying Information Where Can You Find A Listing
Mar 31, 2025
-
True Or False Professional And Technical Communication Is Research Oriented
Mar 31, 2025
-
Express The Force As A Cartesian Vector
Mar 31, 2025
-
Selling And Administrative Costs Are Blank Costs
Mar 31, 2025
-
Varcarolis Foundations Of Psychiatric Mental Health Nursing A Clinical Approach
Mar 31, 2025
Related Post
Thank you for visiting our website which covers about Determine The Magnitude Of The Pin Force At A . We hope the information provided has been useful to you. Feel free to contact us if you have any questions or need further assistance. See you next time and don't miss to bookmark.