Delph Company Uses A Job Order Costing System
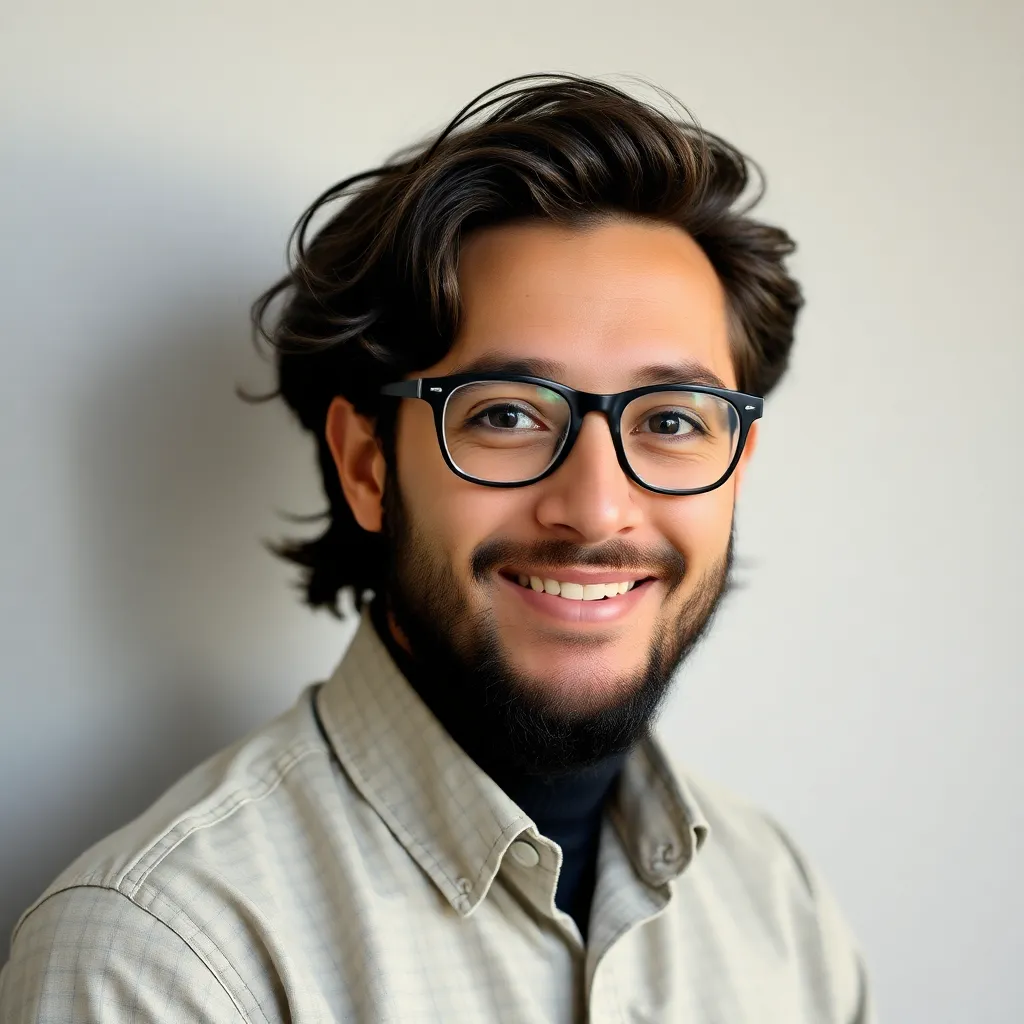
Holbox
Apr 17, 2025 · 7 min read

Table of Contents
- Delph Company Uses A Job Order Costing System
- Table of Contents
- Delph Company Uses a Job Order Costing System: A Deep Dive
- What is Job Order Costing?
- The Delph Company's Job Order Costing System: A Step-by-Step Guide
- 1. Job Authorization and Cost Sheet Creation:
- 2. Direct Materials Tracking:
- 3. Direct Labor Costing:
- 4. Manufacturing Overhead Allocation:
- 5. Cost Accumulation and Reconciliation:
- 6. Cost of Goods Sold (COGS) and Inventory Valuation:
- Advantages of Job Order Costing for Delph Company
- Limitations of Job Order Costing for Delph Company
- Addressing the Limitations: Improving Delph's System
- Conclusion
- Latest Posts
- Latest Posts
- Related Post
Delph Company Uses a Job Order Costing System: A Deep Dive
Delph Company, a hypothetical manufacturing business, exemplifies the practical application of a job order costing system. This detailed exploration will analyze how Delph uses this system, highlighting its key components, advantages, and limitations. We'll examine the process from initial job costing to final cost determination, exploring the intricacies involved in accurately tracking costs and profitability. Understanding this system is crucial for any business operating in a similar environment, where unique projects or jobs require precise cost accounting.
What is Job Order Costing?
Job order costing is a cost accounting system used to track the costs associated with individual projects or jobs. Unlike process costing, which averages costs across a large volume of homogenous products, job order costing focuses on assigning costs to specific, identifiable units of output. This is particularly relevant for companies that produce customized products or services, where each job has unique characteristics and therefore unique costs. Delph Company, let’s assume, manufactures bespoke furniture pieces, each with specific designs and materials, making job order costing the most appropriate method for cost tracking.
The Delph Company's Job Order Costing System: A Step-by-Step Guide
Delph Company's job order costing system involves a series of carefully documented steps:
1. Job Authorization and Cost Sheet Creation:
Every job at Delph begins with a customer order. This order details the specifications of the furniture piece, including materials, design, and any special requests. Once approved, a unique job number is assigned, and a job cost sheet is created. This sheet serves as a central repository for all costs associated with that specific job. This ensures traceability and accountability. The job cost sheet typically includes spaces for:
- Job Number: A unique identifier for each project.
- Customer Name: Identifies the client for the order.
- Date of Order: The date the order was received.
- Description of Job: Detailed specifications of the furniture piece.
- Direct Materials: A breakdown of all materials used, including their quantity and cost.
- Direct Labor: The time spent by employees working on the job, along with their hourly rates.
- Manufacturing Overhead: Indirect costs allocated to the job (explained in detail later).
- Total Job Cost: The sum of all direct materials, direct labor, and manufacturing overhead.
2. Direct Materials Tracking:
Delph meticulously tracks the direct materials used in each job. This involves using materials requisitions – forms that authorize the release of materials from the company’s inventory to a specific job. Each requisition lists the job number, materials used, and quantity. The cost of these materials is then entered onto the job cost sheet. Delph's inventory management system plays a crucial role in ensuring accurate material tracking and cost assignment. Regular inventory counts help to verify the accuracy of the system. This reduces the risk of overstocking or shortages, thus controlling costs.
3. Direct Labor Costing:
Delph's employees use time sheets to record the time spent working on each job. These time sheets are crucial in accurately determining direct labor costs. Each time sheet specifies the job number, employee's name, hours worked, and hourly rate. Delph may utilize a payroll system that automatically transfers data from time sheets to job cost sheets, streamlining the process and minimizing human error. This also allows for better control of labor costs by analyzing labor hours per job and identifying potential inefficiencies.
4. Manufacturing Overhead Allocation:
Manufacturing overhead comprises indirect costs that cannot be directly traced to specific jobs. These include factory rent, utilities, depreciation of factory equipment, and the salaries of factory supervisors. Delph uses a predetermined overhead rate to allocate manufacturing overhead to individual jobs. This rate is calculated at the beginning of the accounting period (e.g., annually) by estimating total manufacturing overhead costs and dividing them by an allocation base, such as direct labor hours or machine hours.
Formula for Predetermined Overhead Rate:
Predetermined Overhead Rate = Estimated Total Manufacturing Overhead Costs / Estimated Total Allocation Base
Using this predetermined rate, Delph allocates a portion of the total manufacturing overhead to each job based on the job’s consumption of the allocation base. For example, if a job uses 100 direct labor hours, and the predetermined overhead rate is $20 per direct labor hour, $2000 of manufacturing overhead would be allocated to that job.
5. Cost Accumulation and Reconciliation:
Throughout the production process, Delph regularly updates the job cost sheets with the latest direct materials, direct labor, and manufacturing overhead costs. This ensures that the job cost sheet always reflects the current cost of the job. At the completion of each job, Delph reconciles the actual costs with the budgeted costs, identifying any variances. This variance analysis helps management to understand where costs exceed or fall short of expectations, leading to improved cost control and efficiency.
6. Cost of Goods Sold (COGS) and Inventory Valuation:
Once a job is completed, the total job cost is transferred from the job cost sheet to the finished goods inventory. When the job is sold, the cost is transferred from finished goods inventory to the cost of goods sold (COGS). This accurate tracking of costs ensures that Delph's financial statements reflect the true cost of goods sold and the value of its inventory. This is essential for accurate financial reporting and effective inventory management.
Advantages of Job Order Costing for Delph Company
Delph Company benefits significantly from using a job order costing system:
- Accurate Cost Tracking: Provides detailed cost information for each job, facilitating accurate pricing and profitability analysis.
- Improved Decision-Making: Provides valuable insights into the cost drivers of each job, allowing management to make informed decisions about pricing, resource allocation, and process improvements.
- Enhanced Customer Communication: Allows Delph to provide customers with detailed cost breakdowns for their orders, promoting transparency and building trust.
- Efficient Inventory Management: Facilitates accurate tracking of materials and finished goods, improving inventory control and reducing waste.
- Better Profitability Analysis: By tracking the costs of individual jobs, Delph can identify profitable and unprofitable jobs, allowing for strategic adjustments.
Limitations of Job Order Costing for Delph Company
While beneficial, job order costing also has limitations:
- Complexity: The system can be complex and time-consuming, particularly for companies with a high volume of jobs. Delph must ensure its employees are adequately trained to manage the system effectively.
- Overhead Allocation: The accuracy of overhead allocation depends on the accuracy of the predetermined overhead rate. If the actual overhead costs differ significantly from the estimated overhead costs, the allocated overhead may not accurately reflect the actual overhead consumed by each job.
- Cost of Implementation: Implementing and maintaining a job order costing system requires investment in software, training, and personnel.
- Potential for Errors: Manual data entry increases the potential for errors, especially in a high-volume environment. Delph should invest in robust software solutions to minimize human error.
Addressing the Limitations: Improving Delph's System
To mitigate the limitations, Delph can consider several improvements:
- Investing in Technology: Implementing accounting software specifically designed for job order costing can automate many of the manual tasks, reducing errors and improving efficiency.
- Refining Overhead Allocation: Using multiple allocation bases, such as direct labor hours and machine hours, can provide a more accurate allocation of overhead costs. Regularly reviewing and updating the predetermined overhead rate can also improve accuracy.
- Implementing Activity-Based Costing (ABC): ABC costing is a more sophisticated approach to overhead allocation that traces overhead costs to specific activities, providing a more precise understanding of cost drivers. This can be particularly beneficial for Delph if the overhead costs are significantly influenced by different activities associated with different jobs.
- Strengthening Internal Controls: Implementing robust internal controls, such as regular reconciliation of job cost sheets and periodic inventory counts, can minimize the risk of errors and fraud.
- Employee Training: Thorough training of employees on the job costing procedures is crucial for accurate data entry and efficient system operation.
Conclusion
Delph Company's utilization of a job order costing system is essential for accurate cost tracking, efficient resource management, and informed decision-making. While the system presents some complexities and limitations, these can be effectively addressed through strategic improvements, including technology implementation, refinement of overhead allocation, and enhanced internal controls. By carefully managing and continuously refining its job order costing system, Delph can enhance its operational efficiency, improve profitability, and strengthen its competitive position in the bespoke furniture market. The detailed tracking of costs allows for better pricing strategies, efficient resource allocation, and improved communication with customers, leading to greater overall success. Through meticulous attention to detail and continuous process improvement, Delph can leverage the benefits of job order costing to achieve its business objectives.
Latest Posts
Latest Posts
-
A Partition Between A Users Computer
Apr 23, 2025
-
A Restraint Order Must Contain Which Of The Following
Apr 23, 2025
-
Draw The Organic Product Of The Given Reaction
Apr 23, 2025
-
Which Term Refers To The Strong Information Correlation Between Qubits
Apr 23, 2025
-
The Term Technological Diffusion Is Defined As
Apr 23, 2025
Related Post
Thank you for visiting our website which covers about Delph Company Uses A Job Order Costing System . We hope the information provided has been useful to you. Feel free to contact us if you have any questions or need further assistance. See you next time and don't miss to bookmark.