Dehner Corporation Uses A Job Order Costing System
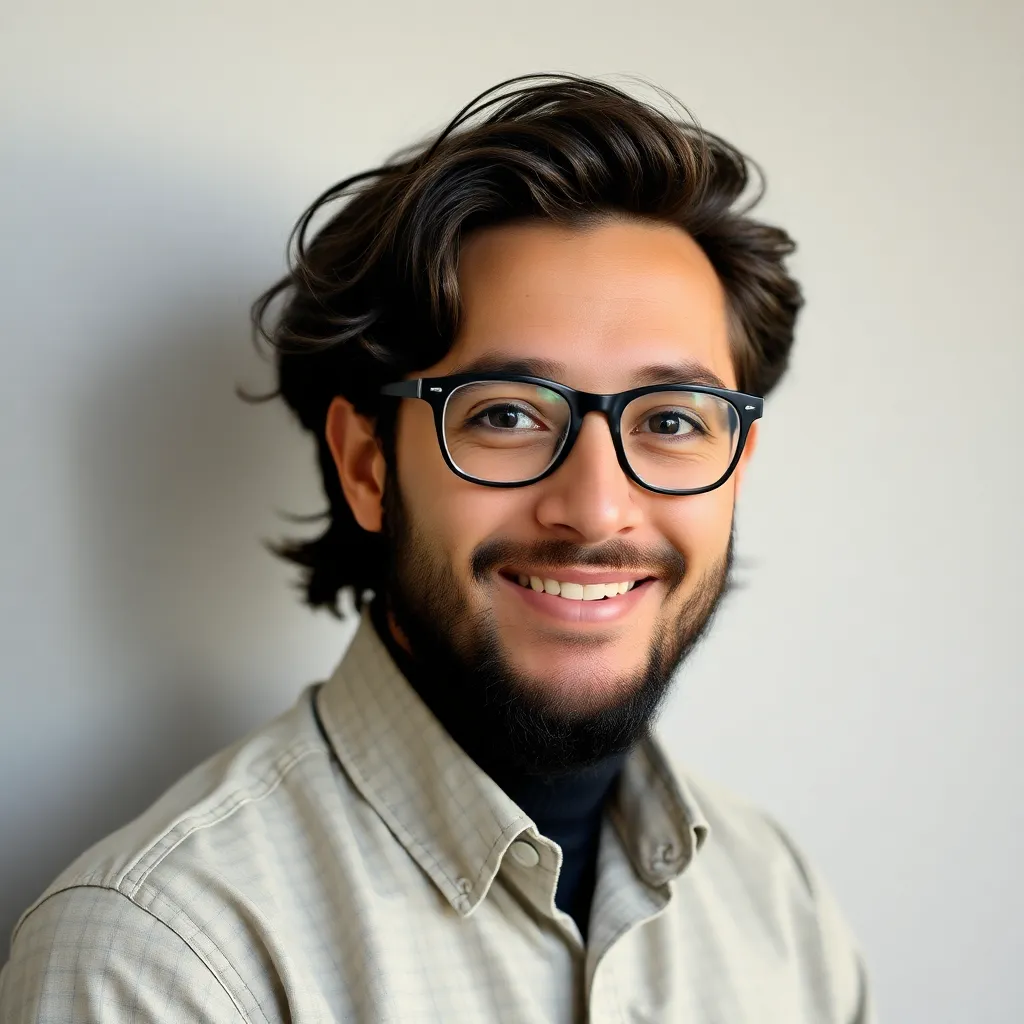
Holbox
Apr 07, 2025 · 7 min read

Table of Contents
- Dehner Corporation Uses A Job Order Costing System
- Table of Contents
- Dehner Corporation Uses a Job Order Costing System: A Deep Dive
- Understanding Job Order Costing at Dehner Corporation
- 1. Direct Materials
- 2. Direct Labor
- 3. Manufacturing Overhead
- The Job Order Cost Sheet: Dehner Corporation's Central Document
- Advantages of Job Order Costing at Dehner Corporation
- Challenges of Job Order Costing at Dehner Corporation
- Integrating Technology for Efficiency at Dehner Corporation
- Beyond Costing: Using Data for Strategic Decision-Making
- Conclusion: Job Order Costing as a Cornerstone for Dehner Corporation's Success
- Latest Posts
- Latest Posts
- Related Post
Dehner Corporation Uses a Job Order Costing System: A Deep Dive
Dehner Corporation, a hypothetical manufacturing company for the purpose of this illustration, uses a job order costing system to track the costs associated with each individual project or job. This system, unlike process costing which averages costs across a large production run, offers granular detail, making it ideal for companies producing unique or customized goods. This article will delve into the intricacies of how Dehner Corporation likely implements this system, highlighting its advantages, challenges, and overall impact on their business operations.
Understanding Job Order Costing at Dehner Corporation
At Dehner Corporation, each job, whether it's a bespoke piece of machinery or a highly customized batch of specialized components, receives a unique identification number. This number acts as a tracking device, allowing the company to meticulously monitor all direct materials, direct labor, and manufacturing overhead costs associated with that specific project. Let's break down each cost element:
1. Direct Materials
Direct materials are the raw materials directly used in the production of a particular job. For Dehner Corporation, this could include steel alloys, specialized plastics, electronic components, or any other materials integral to the finished product. The company uses a meticulous inventory tracking system, likely employing a perpetual inventory method, to ensure accurate record-keeping. Each requisition of materials for a job is documented, linking the cost directly to the job's identification number. This precise tracking minimizes waste and ensures accurate cost allocation.
2. Direct Labor
Direct labor represents the wages and benefits paid to employees directly involved in the production process. For Dehner Corporation, this would include the machinists, welders, electricians, and assembly technicians working hands-on with each job. Time sheets, carefully monitored and reviewed, record the time spent by each employee on each job. These time sheets, coupled with the employees' hourly wage rates and benefits costs, provide a precise calculation of the direct labor costs incurred for each job. The system likely uses a payroll system integrated with the job costing system to ensure accuracy and efficiency.
3. Manufacturing Overhead
Manufacturing overhead encompasses all indirect costs associated with the production process. This is a crucial element often overlooked, but it's essential for accurate costing at Dehner Corporation. These costs are difficult to directly trace to specific jobs. Examples for Dehner Corporation could include:
- Factory rent and utilities: The cost of operating the manufacturing facility.
- Depreciation of factory equipment: The allocation of the cost of machinery over its useful life.
- Factory supervision salaries: The wages of supervisors overseeing the production process.
- Factory insurance: Costs associated with insuring the factory and its contents.
- Maintenance and repairs: Costs incurred in maintaining and repairing factory equipment.
Dehner Corporation likely uses a predetermined overhead rate to allocate manufacturing overhead costs to individual jobs. This rate is calculated at the beginning of an accounting period (often annually) by estimating the total manufacturing overhead costs and dividing them by an allocation base, such as direct labor hours or machine hours. This simplifies the costing process and provides timely cost information, although it does involve an element of estimation. A review and adjustment of this rate may occur periodically to ensure accuracy.
The Job Order Cost Sheet: Dehner Corporation's Central Document
The heart of Dehner Corporation's job order costing system is the job order cost sheet. This document serves as a comprehensive record of all costs associated with a particular job. It meticulously tracks direct materials, direct labor, and manufacturing overhead, providing a clear picture of the total cost of the job at each stage of the production process.
A typical job order cost sheet for Dehner Corporation might include columns for:
- Job Number: The unique identifier for the job.
- Date: The date of each transaction related to the job.
- Description: A description of the materials or labor used.
- Direct Materials: The cost of materials used on the job.
- Direct Labor: The cost of labor used on the job.
- Manufacturing Overhead: The overhead allocated to the job.
- Total Cost: The sum of direct materials, direct labor, and manufacturing overhead.
This sheet is regularly updated as the job progresses, providing real-time cost data. This allows management to monitor the profitability of each job and make necessary adjustments throughout the production process. The final total cost on the job order cost sheet becomes the basis for pricing decisions, inventory valuation, and ultimately, the calculation of the company's profit.
Advantages of Job Order Costing at Dehner Corporation
The use of a job order costing system offers several key advantages for Dehner Corporation:
- Accurate Costing: Provides highly accurate cost information for each individual job, enabling precise pricing decisions and better profitability analysis.
- Improved Cost Control: Offers detailed tracking of costs, allowing management to identify areas for improvement and implement cost-saving measures.
- Better Inventory Management: Facilitates better tracking of inventory levels and costs, minimizing waste and maximizing efficiency.
- Enhanced Customer Relations: Allows for more accurate and transparent cost reporting to customers, fostering trust and building stronger relationships.
- Pricing Decisions: Precise cost information enables informed pricing decisions, ensuring that Dehner Corporation earns a healthy profit margin on each job while remaining competitive.
- Profitability Analysis: Provides granular data on the profitability of each job, enabling managers to identify profitable and unprofitable jobs, and make data-driven decisions regarding future projects.
- Performance Evaluation: Detailed cost data allows for accurate evaluation of the performance of different departments and employees.
Challenges of Job Order Costing at Dehner Corporation
While job order costing provides many benefits, it also presents some challenges:
- Complexity: The system is relatively complex to implement and maintain, requiring significant administrative effort and resources. This necessitates skilled personnel capable of managing the system efficiently and accurately.
- Time-Consuming: The meticulous tracking and documentation required can be time-consuming, especially for companies with a large number of jobs. Streamlining processes is crucial to minimize this overhead.
- Overhead Allocation: Accurately allocating manufacturing overhead can be challenging, as it involves estimating indirect costs and selecting an appropriate allocation base. Careful planning and regular review are necessary to mitigate potential inaccuracies.
- Cost of Implementation: Implementing a robust job order costing system can require significant upfront investment in software and training. This cost must be weighed against the benefits derived from the improved accuracy and control.
Integrating Technology for Efficiency at Dehner Corporation
To overcome some of the challenges associated with job order costing, Dehner Corporation can leverage technology. Enterprise Resource Planning (ERP) systems, specifically those designed for manufacturing, can significantly streamline the process. These systems can automate data entry, track materials and labor accurately, and calculate manufacturing overhead automatically. Integration with other systems, such as inventory management and payroll, further enhances accuracy and reduces manual effort. The use of barcode scanners or RFID tags can further automate the tracking of materials and labor, reducing errors and freeing up personnel for other tasks.
Beyond Costing: Using Data for Strategic Decision-Making
The data generated by the job order costing system at Dehner Corporation extends far beyond simple cost tracking. The detailed information can be used for strategic decision-making across various aspects of the business:
- Pricing Strategy: Analyzing the cost of previous jobs allows Dehner Corporation to develop a more sophisticated pricing strategy, considering factors like material costs, labor complexity, and desired profit margins.
- Process Improvement: Identifying areas where costs are consistently higher than expected can highlight inefficiencies in the production process, leading to improvements and cost reductions.
- Product Development: Understanding the cost breakdown of different products can inform decisions regarding product development and diversification.
- Resource Allocation: The data allows for better allocation of resources, ensuring that materials, labor, and equipment are utilized effectively.
- Capacity Planning: Analyzing the time taken to complete different jobs allows for better capacity planning, improving scheduling and optimizing production flow.
Conclusion: Job Order Costing as a Cornerstone for Dehner Corporation's Success
The implementation of a well-structured job order costing system is a crucial element for Dehner Corporation’s success. While it presents certain challenges, the benefits of accurate cost tracking, improved efficiency, and enhanced strategic decision-making significantly outweigh the drawbacks. By embracing technological advancements and employing skilled personnel, Dehner Corporation can harness the power of job order costing to optimize its operations, improve profitability, and achieve sustainable growth in a competitive market. Regular reviews and adjustments of the system will ensure it remains a valuable asset for years to come. The investment in this system is an investment in the long-term health and success of the company.
Latest Posts
Latest Posts
-
Block Diagram Analysis And Interpretation Activity 10 6
Apr 14, 2025
-
Ways Of The World 5th Edition
Apr 14, 2025
-
Provide The Correct Iupac Systematic Name For The Following Compound
Apr 14, 2025
-
Select All Of The Following That Are True About Protists
Apr 14, 2025
-
Which Of The Following Is Not A Function Of Lipids
Apr 14, 2025
Related Post
Thank you for visiting our website which covers about Dehner Corporation Uses A Job Order Costing System . We hope the information provided has been useful to you. Feel free to contact us if you have any questions or need further assistance. See you next time and don't miss to bookmark.