Daily Capacity Of A Product Layout Is Determined By
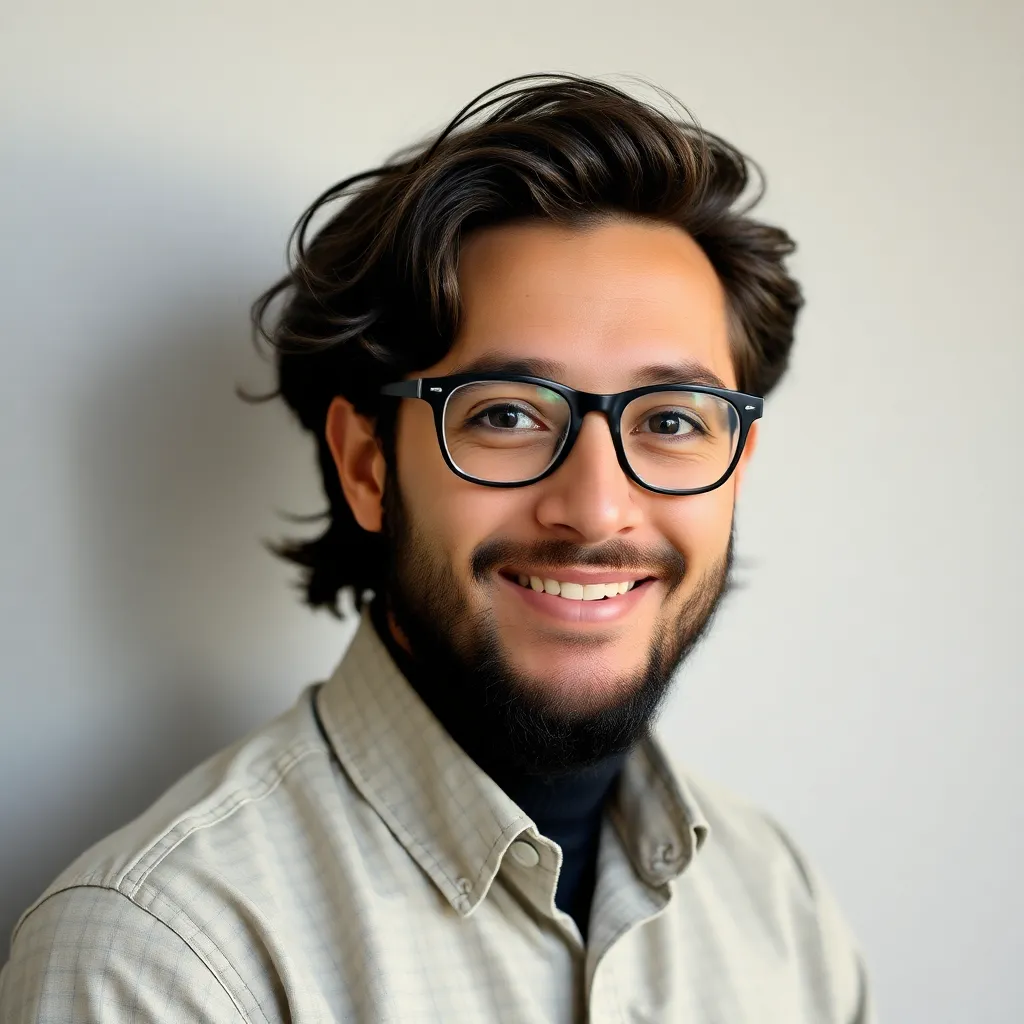
Holbox
Apr 05, 2025 · 7 min read

Table of Contents
- Daily Capacity Of A Product Layout Is Determined By
- Table of Contents
- Daily Capacity of a Product Layout: A Comprehensive Guide
- Understanding Product Layouts and Their Impact on Capacity
- Key Characteristics of Product Layouts Affecting Daily Capacity
- Calculating Daily Capacity: A Step-by-Step Approach
- 1. Bottleneck-Based Calculation: The Most Conservative Approach
- 2. Theoretical Capacity Calculation: The Ideal Scenario
- 3. Adjusted Capacity Calculation: A More Realistic Approach
- Factors Affecting Daily Capacity: A Deeper Dive
- 1. Production Scheduling and Sequencing: Optimizing the Workflow
- 2. Preventive Maintenance: Minimizing Downtime
- 3. Worker Training and Skill Development: Enhancing Productivity
- 4. Quality Control Measures: Reducing Waste and Rework
- 5. Technological Advancements: Automating and Streamlining Processes
- 6. Inventory Management: Optimizing Material Flow
- 7. Workplace Ergonomics: Improving Worker Comfort and Efficiency
- Strategies for Increasing Daily Capacity
- Conclusion: A Continuous Improvement Process
- Latest Posts
- Latest Posts
- Related Post
Daily Capacity of a Product Layout: A Comprehensive Guide
Determining the daily capacity of a product layout is crucial for efficient production planning and scheduling. Understanding the factors that influence capacity allows businesses to optimize their operations, meet customer demand, and maximize profitability. This comprehensive guide delves into the intricacies of calculating daily capacity, exploring various influencing factors and providing practical strategies for improvement.
Understanding Product Layouts and Their Impact on Capacity
Before diving into the calculation, it's vital to understand what a product layout entails. A product layout, also known as a line layout, is a production arrangement where workstations are arranged sequentially based on the steps involved in manufacturing a specific product. This linear flow aims to streamline the process and maximize efficiency. However, the daily capacity of such a layout is not simply a matter of adding up the individual workstation outputs. Several interconnected factors play a significant role.
Key Characteristics of Product Layouts Affecting Daily Capacity
- Bottleneck Analysis: Identifying the bottleneck, the slowest workstation in the line, is paramount. The entire line's capacity is limited by the output of this bottleneck. Optimizing this station is the most impactful way to increase overall capacity.
- Workstation Cycle Time: This is the time it takes to complete one unit at a single workstation. Variations in cycle times across workstations directly influence the overall output.
- Number of Workstations: More workstations generally equate to a higher potential capacity. However, poorly balanced workstations can negate this advantage.
- Machine Uptime and Downtime: Machine failures, maintenance schedules, and unplanned downtime significantly impact daily capacity. Effective preventive maintenance and robust contingency plans are essential.
- Worker Efficiency and Skill: The skill and efficiency of workers directly influence the pace of production. Training, proper ergonomic design, and effective workforce management are crucial.
- Material Handling and Transportation: Efficient material flow between workstations is vital. Inefficient material handling can create delays and reduce overall capacity. This includes minimizing travel time and optimizing material storage locations.
- Quality Control: Implementing rigorous quality checks throughout the production line can detect and address defects early. While this might seem to slow production, early detection minimizes waste and rework, which ultimately enhances efficiency.
- Buffer Stock: Having buffer stock between workstations can mitigate the impact of minor disruptions or variations in workstation cycle times. However, excessive buffer stock can tie up capital and space.
- Demand Fluctuations: Daily capacity needs to be flexible enough to handle variations in customer demand. Forecasting and planning are essential to manage peaks and troughs effectively.
Calculating Daily Capacity: A Step-by-Step Approach
There are several methods to calculate the daily capacity of a product layout, each with its strengths and weaknesses. Let's explore some common approaches.
1. Bottleneck-Based Calculation: The Most Conservative Approach
This method focuses on the bottleneck workstation. The daily capacity is determined by the output of the slowest workstation.
Steps:
- Identify the Bottleneck: Analyze the cycle time of each workstation to find the slowest one.
- Determine the Bottleneck's Hourly Output: Divide 60 minutes (one hour) by the bottleneck's cycle time (in minutes) to get the number of units produced per hour.
- Calculate Daily Output: Multiply the hourly output by the number of operating hours per day. This yields the daily capacity based on the bottleneck.
Example:
If the bottleneck workstation has a cycle time of 5 minutes, and the plant operates for 8 hours a day, the daily capacity is: (60 minutes/hour) / 5 minutes/unit * 8 hours/day = 96 units/day.
This approach offers a conservative estimate, ensuring realistic expectations and avoiding overpromising.
2. Theoretical Capacity Calculation: The Ideal Scenario
This method ignores bottlenecks and assumes perfect efficiency at every workstation.
Steps:
- Determine the Hourly Output of Each Workstation: Divide 60 minutes by the cycle time of each workstation.
- Identify the Lowest Hourly Output: This represents the theoretical bottleneck even if it isn't the actual bottleneck under real-world conditions.
- Calculate Daily Output: Multiply the lowest hourly output by the number of operating hours per day.
Example: Using the same 8-hour workday, if the lowest hourly output across all workstations is 10 units/hour, the theoretical daily capacity is 10 units/hour * 8 hours/day = 80 units/day.
This method provides an optimistic outlook on potential capacity but lacks consideration for real-world inefficiencies.
3. Adjusted Capacity Calculation: A More Realistic Approach
This approach incorporates efficiency factors to account for downtime, worker breaks, and other real-world limitations.
Steps:
- Calculate Theoretical Capacity (as above).
- Determine the Efficiency Factor: This is usually expressed as a percentage reflecting the actual operational efficiency (e.g., 85% efficiency accounts for 15% downtime). This factor needs to be determined through historical data or estimations.
- Calculate Adjusted Capacity: Multiply the theoretical capacity by the efficiency factor.
Example: Using the theoretical capacity of 80 units/day and an efficiency factor of 85%, the adjusted daily capacity is 80 units/day * 0.85 = 68 units/day.
This method provides a more realistic estimate, bridging the gap between theoretical potential and actual achievable output.
Factors Affecting Daily Capacity: A Deeper Dive
Beyond the basic calculations, several other factors significantly influence daily capacity. Understanding these nuances is crucial for accurate assessment and improvement.
1. Production Scheduling and Sequencing: Optimizing the Workflow
Effective scheduling minimizes idle time and maximizes resource utilization. Techniques like Lean Manufacturing principles (e.g., Kanban, 5S) and Six Sigma methodologies can significantly improve efficiency. Prioritizing orders strategically and optimizing material flow also contributes to enhanced capacity.
2. Preventive Maintenance: Minimizing Downtime
Regular maintenance prevents unexpected breakdowns and reduces downtime. A well-structured maintenance schedule minimizes interruptions and maintains consistent production.
3. Worker Training and Skill Development: Enhancing Productivity
Investing in training and development improves worker skills, leading to faster processing times and reduced errors. Providing employees with the right tools and resources also enhances productivity.
4. Quality Control Measures: Reducing Waste and Rework
Implementing rigorous quality checks at various stages reduces defects and minimizes rework, thus improving the effective output. A proactive approach to quality ensures that fewer units are scrapped or require correction.
5. Technological Advancements: Automating and Streamlining Processes
Automating repetitive tasks and incorporating advanced technologies can dramatically improve efficiency and increase capacity. Investing in newer, faster, and more reliable equipment is a long-term strategy for boosting output.
6. Inventory Management: Optimizing Material Flow
Efficient inventory management ensures that materials are available when needed without excessive storage. Just-in-time (JIT) inventory systems can minimize waste and improve flow.
7. Workplace Ergonomics: Improving Worker Comfort and Efficiency
Ergonomic workstations and work practices reduce fatigue and injuries, leading to improved productivity and reduced absenteeism.
Strategies for Increasing Daily Capacity
Once the daily capacity is determined, the focus shifts to increasing it. Here are several key strategies:
- Bottleneck Improvement: Focus on improving the bottleneck workstation. This might involve adding more equipment, optimizing processes, or retraining workers.
- Process Optimization: Analyze the entire production line to identify inefficiencies and streamline processes. Lean methodologies are highly effective here.
- Technology Upgrade: Invest in newer, faster equipment to improve cycle times and reduce downtime.
- Worker Training: Provide training to improve worker skills and efficiency.
- Preventive Maintenance: Implement a robust preventative maintenance schedule to reduce downtime.
- Improved Scheduling: Optimize the production schedule to minimize idle time and maximize resource utilization.
- Inventory Management: Implement efficient inventory management to ensure that materials are available when needed.
- Ergonomic Improvements: Improve workplace ergonomics to reduce fatigue and improve worker comfort.
- Outsourcing: Consider outsourcing certain tasks to free up internal resources.
Conclusion: A Continuous Improvement Process
Determining the daily capacity of a product layout is an ongoing process. Regularly reviewing and updating calculations based on actual production data, technological advancements, and market demands is vital for maintaining efficiency and meeting production goals. The strategies outlined above, when implemented strategically, can significantly enhance daily capacity and contribute to overall business success. Remember that continuous improvement is key to sustained growth and maintaining a competitive edge.
Latest Posts
Latest Posts
-
2e 4e 1 Chloro 3 Methyl 2 4 Hexadiene
Apr 11, 2025
-
Which Idea Is Inconsistent With Pure Competition
Apr 11, 2025
-
Glucagon Secretion Is Stimulated When Blood Glucose Concentration Decreases
Apr 11, 2025
-
To Safeguard Against Hacking Practicing Situational Awareness Means
Apr 11, 2025
-
Identify The Precautions To Take With Exits In The Lab
Apr 11, 2025
Related Post
Thank you for visiting our website which covers about Daily Capacity Of A Product Layout Is Determined By . We hope the information provided has been useful to you. Feel free to contact us if you have any questions or need further assistance. See you next time and don't miss to bookmark.