Costs Assigned To Units Of Product Under Absorption Costing Include
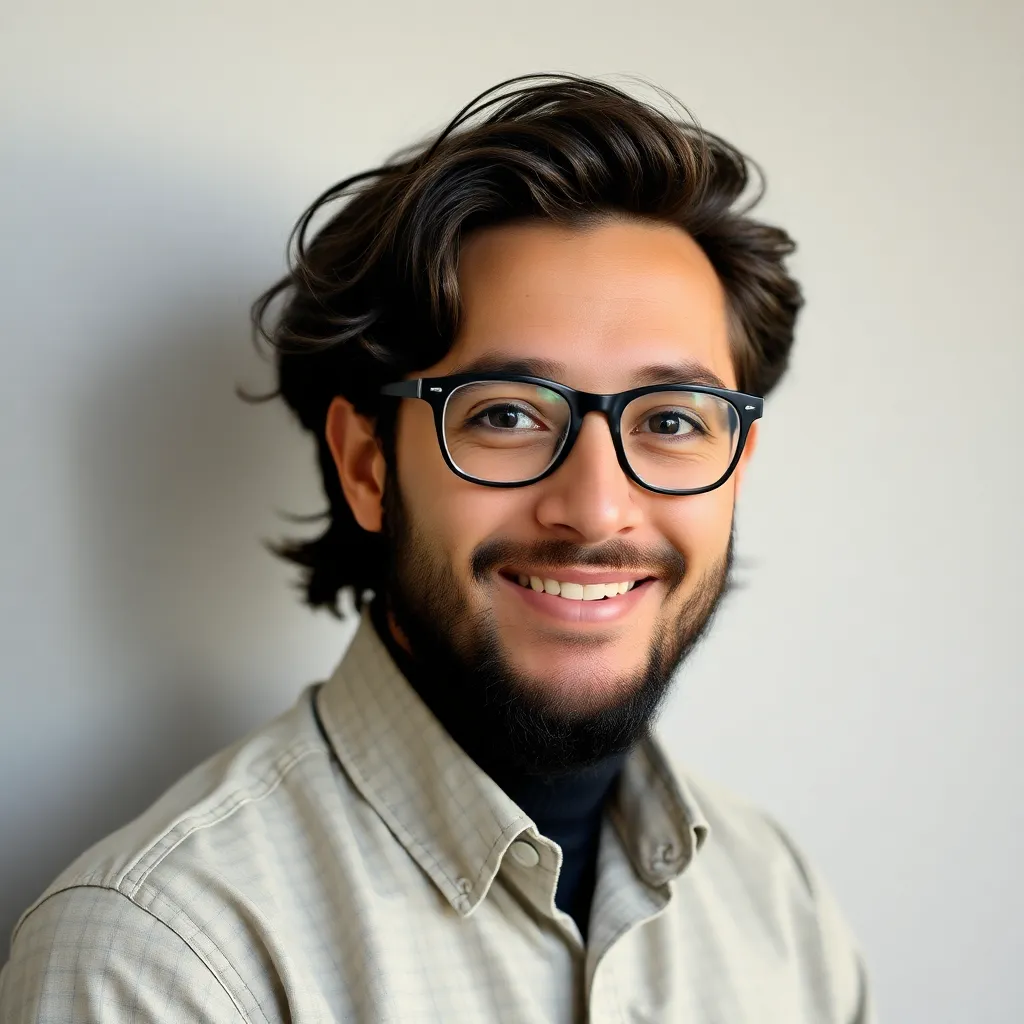
Holbox
May 12, 2025 · 6 min read
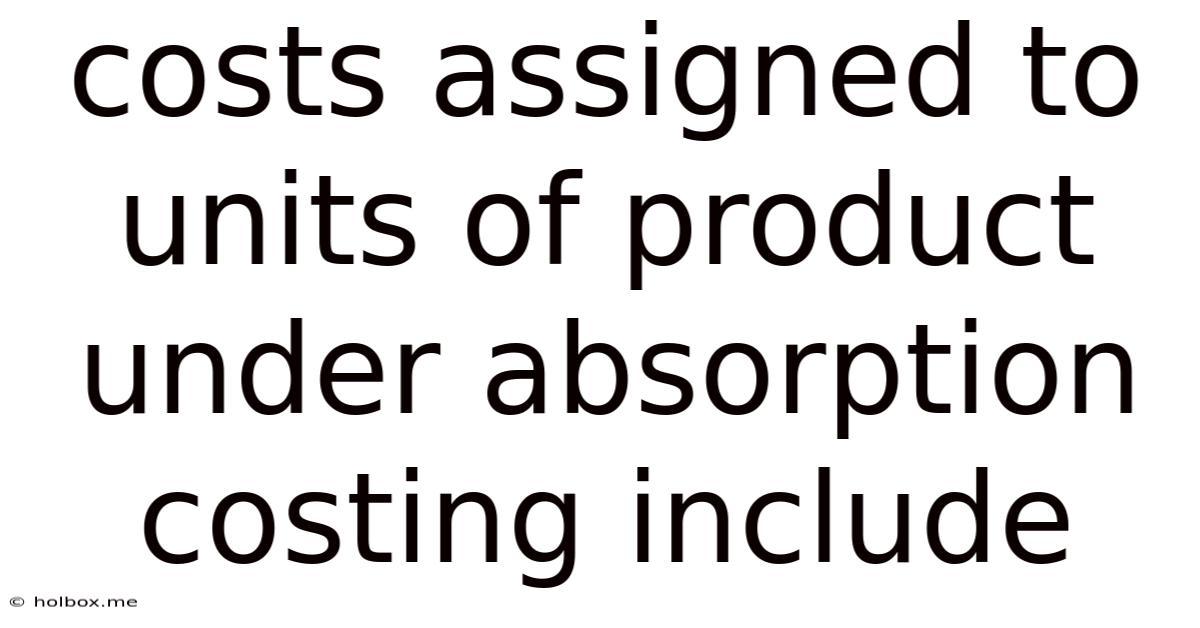
Table of Contents
- Costs Assigned To Units Of Product Under Absorption Costing Include
- Table of Contents
- Costs Assigned to Units of Product Under Absorption Costing Include
- Direct Materials: The Foundation of Production
- Identifying Direct Materials
- Cost Tracking and Allocation
- Direct Labor: The Human Element in Cost
- Accurately Calculating Direct Labor Costs
- Impact of Labor Efficiency
- Variable Manufacturing Overhead: Costs that Fluctuate with Production
- Allocating Variable Overhead
- Fixed Manufacturing Overhead: Consistent Costs Regardless of Production
- Allocating Fixed Overhead
- The Impact of Capacity Utilization
- Absorption Costing vs. Variable Costing: A Key Distinction
- Practical Example: Calculating Unit Cost Under Absorption Costing
- Implications of Absorption Costing for Decision Making
- Challenges and Considerations in Absorption Costing
- Conclusion: Mastering Absorption Costing for Accurate Financial Reporting and Strategic Decision Making
- Latest Posts
- Related Post
Costs Assigned to Units of Product Under Absorption Costing Include
Absorption costing, also known as full costing, is a method of inventory costing where all manufacturing costs—direct materials, direct labor, and both variable and fixed manufacturing overhead—are included in the cost of a product. Understanding what constitutes these costs and how they're allocated is crucial for accurate financial reporting and effective managerial decision-making. This article delves deep into the specific cost components included in absorption costing, highlighting their significance and providing practical examples.
Direct Materials: The Foundation of Production
Direct materials are the raw materials that are directly traceable to the finished product. These are the core components that undergo transformation during the manufacturing process. The cost of direct materials includes not only the purchase price but also any freight charges, handling fees, and other costs directly associated with acquiring and preparing the materials for use.
Identifying Direct Materials
The key to accurate cost assignment is correctly identifying direct materials. For example, in furniture manufacturing, the wood, fabric, and hardware are clear-cut direct materials. In contrast, cleaning supplies or lubricants for machinery, while essential for production, are usually classified as indirect materials (part of manufacturing overhead).
Cost Tracking and Allocation
Accurate tracking of direct material costs is vital. Businesses often employ inventory management systems to monitor material usage, allowing for precise cost allocation to each product unit. This meticulous tracking ensures that the absorption costing calculation reflects the actual material consumption.
Direct Labor: The Human Element in Cost
Direct labor refers to the wages and benefits paid to employees directly involved in the production process. This includes the time spent assembling, machining, or otherwise transforming raw materials into finished goods. It's important to distinguish direct labor from indirect labor, such as supervisors or maintenance personnel.
Accurately Calculating Direct Labor Costs
Accurate calculation requires detailed timekeeping and payroll records. Companies might use time-study techniques to determine the labor time required for each product, enhancing the precision of cost allocation. Overtime premiums, shift differentials, and employee benefits are all incorporated into the direct labor cost per unit.
Impact of Labor Efficiency
Variations in labor efficiency directly affect the cost per unit. Improved efficiency reduces labor costs, leading to lower product costs under absorption costing. Conversely, inefficiencies increase costs. Careful management of the workforce and continuous improvement initiatives are critical to controlling this aspect.
Variable Manufacturing Overhead: Costs that Fluctuate with Production
Variable manufacturing overhead encompasses costs that change directly with the level of production. These costs increase as production volume rises and decrease as it falls. Examples include:
- Indirect Materials: These are materials used in the production process but are not directly traceable to specific products. Examples include lubricants, cleaning supplies, and small tools.
- Utilities: The portion of electricity, gas, and water consumed in the production facilities is often considered variable overhead.
- Supplies: Items like cutting oil, solvents, and other consumable materials used in manufacturing.
Allocating Variable Overhead
Variable manufacturing overhead costs are typically allocated based on a predetermined rate, often linked to a cost driver such as machine hours or direct labor hours. For instance, if the total variable overhead budget is $10,000 for 10,000 machine hours, the predetermined overhead rate would be $1 per machine hour.
Fixed Manufacturing Overhead: Consistent Costs Regardless of Production
Unlike variable overhead, fixed manufacturing overhead costs remain relatively constant regardless of the production volume. These are essential expenses necessary for maintaining the production facility and infrastructure. Examples include:
- Rent or Depreciation of Factory Building: The cost of occupying the factory space remains largely unchanged irrespective of production output.
- Salaries of Factory Supervisors and Maintenance Personnel: These are fixed costs regardless of the number of units produced.
- Insurance and Property Taxes on Factory: These costs are typically unaffected by production volume.
- Depreciation of Factory Equipment: The expense of using factory equipment is usually spread over its useful life, regardless of production levels.
Allocating Fixed Overhead
Allocating fixed overhead is more complex than variable overhead. It's usually assigned based on a predetermined overhead rate, using a suitable cost driver (e.g., machine hours, direct labor hours, or units produced). The choice of cost driver significantly influences the cost assigned to each product unit.
The Impact of Capacity Utilization
The accuracy of fixed overhead allocation depends on the utilization of production capacity. Higher capacity utilization means the fixed costs are spread over more units, leading to a lower cost per unit. Conversely, low capacity utilization leads to a higher cost per unit, impacting profitability.
Absorption Costing vs. Variable Costing: A Key Distinction
It's crucial to contrast absorption costing with variable costing. Variable costing includes only variable manufacturing costs (direct materials, direct labor, and variable manufacturing overhead) in the cost of a product. Fixed manufacturing overhead is treated as a period expense, expensed in the period incurred.
The choice between these methods depends on the specific needs and objectives. Absorption costing is required for financial reporting under Generally Accepted Accounting Principles (GAAP), while variable costing is often preferred for internal managerial decision-making as it provides a clearer picture of the contribution margin of each product.
Practical Example: Calculating Unit Cost Under Absorption Costing
Let's illustrate with a simple example. Assume a company manufactures chairs. For one chair:
- Direct Materials: $20
- Direct Labor: $15
- Variable Manufacturing Overhead: $5 (based on 1 machine hour at $5/hour)
- Fixed Manufacturing Overhead: $10,000 total for the year, based on 10,000 units produced ($1 per unit)
Total Unit Cost (Absorption Costing): $20 + $15 + $5 + $1 = $41
This illustrates how all manufacturing costs are absorbed into the cost of each chair under absorption costing.
Implications of Absorption Costing for Decision Making
Understanding absorption costing has profound implications for several managerial decisions:
- Pricing Decisions: Accurate costing is essential for setting appropriate product prices that ensure profitability.
- Inventory Valuation: Absorption costing significantly affects the valuation of finished goods inventory, influencing the balance sheet and the cost of goods sold.
- Performance Evaluation: Absorption costing data helps in evaluating the efficiency of production and identifying areas for cost reduction.
- Break-Even Analysis: Accurate cost information is crucial for determining the break-even point, which represents the sales volume required to cover all costs.
Challenges and Considerations in Absorption Costing
While absorption costing provides a comprehensive cost picture, it has certain limitations:
- Arbitrary Allocation of Fixed Overhead: The allocation of fixed overhead can be arbitrary, especially when multiple products are manufactured. This can lead to inaccurate cost assignment.
- Inventory Valuation Issues: The inclusion of fixed overhead in inventory valuation can distort the reported profitability if inventory levels fluctuate significantly.
- Complexity: Absorption costing involves more complex calculations than variable costing, which can be time-consuming and potentially increase the risk of errors.
Conclusion: Mastering Absorption Costing for Accurate Financial Reporting and Strategic Decision Making
Absorption costing offers a complete and detailed picture of product costs, including both variable and fixed manufacturing overhead. Mastering this costing method is crucial for accurate financial reporting, effective inventory management, and informed managerial decision-making. While challenges exist, the benefits of a comprehensive cost understanding far outweigh the complexities involved. By carefully tracking and allocating costs, businesses can leverage absorption costing to optimize their operations, improve profitability, and strengthen their competitive position. Continuous monitoring and refinement of the costing system ensure its ongoing relevance and accuracy in the ever-evolving business landscape.
Latest Posts
Related Post
Thank you for visiting our website which covers about Costs Assigned To Units Of Product Under Absorption Costing Include . We hope the information provided has been useful to you. Feel free to contact us if you have any questions or need further assistance. See you next time and don't miss to bookmark.