Cost Of Goods Manufactured Is Calculated As Follows
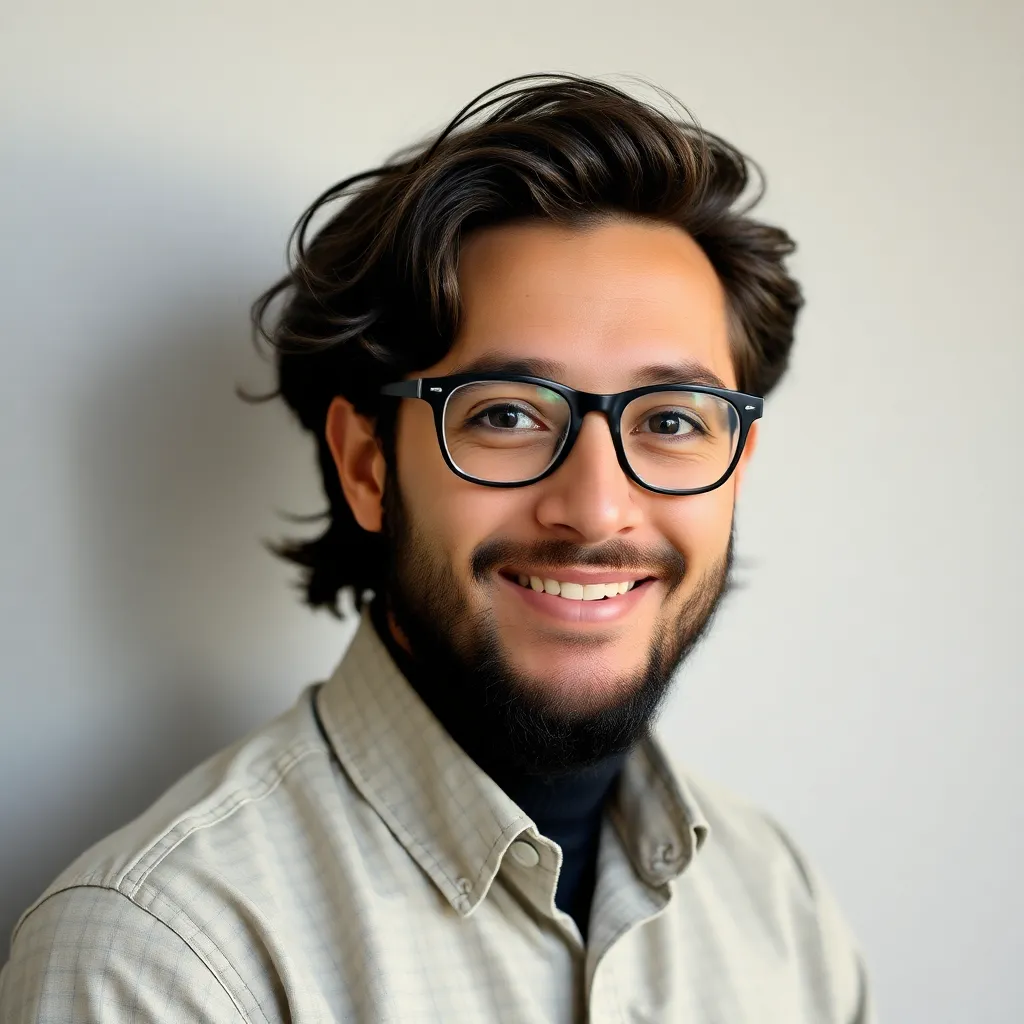
Holbox
Apr 05, 2025 · 5 min read

Table of Contents
- Cost Of Goods Manufactured Is Calculated As Follows
- Table of Contents
- Cost of Goods Manufactured (COGM): A Comprehensive Guide to Calculation and Analysis
- Understanding the Components of COGM
- 1. Beginning Work-in-Process (WIP) Inventory:
- 2. Direct Materials Used:
- 3. Direct Labor:
- 4. Manufacturing Overhead:
- The COGM Formula: A Step-by-Step Breakdown
- Distinguishing COGM from Cost of Goods Sold (COGS)
- Analyzing COGM: Identifying Areas for Improvement
- The Importance of Accurate COGM Calculation
- Advanced Considerations in COGM Calculation
- Conclusion: Mastering COGM for Business Success
- Latest Posts
- Latest Posts
- Related Post
Cost of Goods Manufactured (COGM): A Comprehensive Guide to Calculation and Analysis
The Cost of Goods Manufactured (COGM) is a crucial figure for any manufacturing business. It represents the total cost of producing finished goods during a specific period. Understanding how to calculate COGM and analyzing its components is vital for effective cost management, pricing strategies, and profitability assessment. This comprehensive guide will delve into the intricacies of COGM calculation, explore its key components, and illustrate its importance through practical examples.
Understanding the Components of COGM
The calculation of COGM involves several key components, each contributing to the final cost of producing goods. These components can be broadly categorized as:
1. Beginning Work-in-Process (WIP) Inventory:
This represents the cost of partially completed goods at the beginning of the accounting period. It includes direct materials, direct labor, and manufacturing overhead already incurred on these unfinished products. Accurately tracking WIP inventory is crucial for a precise COGM calculation.
2. Direct Materials Used:
These are the raw materials directly traceable to the production process. This includes the cost of raw materials purchased during the period, adjusted for any beginning and ending raw materials inventory. Efficient inventory management is crucial to minimize waste and optimize direct materials costs.
Calculating Direct Materials Used:
Beginning Raw Materials Inventory + Purchases - Ending Raw Materials Inventory = Direct Materials Used
3. Direct Labor:
This represents the wages and salaries paid to workers directly involved in the manufacturing process. This includes compensation for assembly line workers, machine operators, and other personnel directly contributing to the production of goods. Accurate labor tracking and efficient workforce management are key to controlling direct labor costs.
4. Manufacturing Overhead:
This encompasses all indirect costs associated with the manufacturing process. These costs are not directly traceable to specific products but are necessary for production. Examples include:
- Indirect Labor: Wages paid to factory supervisors, maintenance staff, and quality control personnel.
- Factory Rent and Utilities: Costs associated with operating the manufacturing facility.
- Depreciation of Factory Equipment: The allocation of the cost of factory equipment over its useful life.
- Factory Supplies: Consumables used in the manufacturing process, such as lubricants, cleaning supplies, and small tools.
- Insurance: Costs related to insuring the factory and its equipment.
Accurate allocation of manufacturing overhead is crucial for an accurate COGM calculation. Common methods include:
- Direct Labor Hours: Allocating overhead based on the number of labor hours worked.
- Machine Hours: Allocating overhead based on the number of machine hours used.
- Predetermined Overhead Rate: Setting a predetermined rate based on estimated overhead costs and a chosen allocation base.
The COGM Formula: A Step-by-Step Breakdown
The formula for calculating the Cost of Goods Manufactured (COGM) is as follows:
COGM = Beginning WIP Inventory + Direct Materials Used + Direct Labor + Manufacturing Overhead - Ending WIP Inventory
Let's illustrate this with a practical example:
Example:
Assume a company has the following data for the year:
- Beginning WIP Inventory: $10,000
- Direct Materials Used: $50,000
- Direct Labor: $30,000
- Manufacturing Overhead: $20,000
- Ending WIP Inventory: $5,000
Calculation:
COGM = $10,000 + $50,000 + $30,000 + $20,000 - $5,000 = $105,000
Therefore, the Cost of Goods Manufactured for the year is $105,000. This figure represents the total cost of goods that were completed during the year and transferred to finished goods inventory.
Distinguishing COGM from Cost of Goods Sold (COGS)
While COGM is crucial, it's important to distinguish it from the Cost of Goods Sold (COGS). COGM reflects the cost of goods produced, while COGS reflects the cost of goods sold. The relationship between them is as follows:
Beginning Finished Goods Inventory + COGM - Ending Finished Goods Inventory = COGS
This means that the COGM calculated previously is used to determine the COGS, which is reported on the income statement.
Analyzing COGM: Identifying Areas for Improvement
Analyzing the components of COGM can provide valuable insights into areas for improvement in a manufacturing business. By breaking down the costs, management can identify inefficiencies and implement strategies to reduce costs and improve profitability. For instance:
- High Direct Materials Costs: This could indicate a need for better sourcing, negotiation with suppliers, or waste reduction strategies.
- High Direct Labor Costs: This could suggest a need for improved workforce training, automation, or more efficient production processes.
- High Manufacturing Overhead Costs: This could warrant a review of factory operations, utility consumption, and equipment maintenance to identify potential savings.
The Importance of Accurate COGM Calculation
Accurate COGM calculation is paramount for several reasons:
- Accurate Financial Reporting: It's essential for preparing accurate financial statements, including the income statement and balance sheet.
- Inventory Valuation: It's a crucial component in determining the value of inventory on hand.
- Pricing Decisions: Understanding the cost of producing goods is vital for setting competitive prices that ensure profitability.
- Performance Evaluation: Analyzing COGM over time can help assess the efficiency of manufacturing operations and identify areas for improvement.
- Investment Decisions: Accurate COGM data is crucial for evaluating the financial viability of new investments in equipment or processes.
Advanced Considerations in COGM Calculation
While the basic COGM formula provides a foundation, several advanced considerations may apply in specific situations:
- Joint Products: When multiple products are produced from the same manufacturing process, the cost allocation becomes more complex, requiring methods like market value or net realizable value.
- By-Products: By-products are secondary products generated during the primary manufacturing process. Their cost is often deducted from the COGM of the main product.
- Spoilage and Waste: The costs associated with spoiled or wasted materials need to be accounted for and appropriately allocated.
- Process Costing vs. Job Order Costing: Different costing methods are appropriate depending on the nature of the manufacturing process. Process costing is used for mass production, while job order costing is suitable for customized products.
Conclusion: Mastering COGM for Business Success
The Cost of Goods Manufactured is a fundamental concept in manufacturing accounting. Understanding its calculation, components, and implications is crucial for effective cost management, accurate financial reporting, and informed business decisions. By meticulously tracking costs, analyzing trends, and implementing improvements, businesses can leverage COGM data to enhance efficiency, profitability, and overall success. Regularly reviewing and refining your COGM calculation process ensures the continued health and growth of your manufacturing enterprise. The insights gained from a comprehensive COGM analysis empowers informed strategic decisions, leading to a more sustainable and competitive business model.
Latest Posts
Latest Posts
-
How Is Alveolar Air Different Than Inspired Air
Apr 11, 2025
-
Operant Conditioning Most Importantly Involves Forming Associations Between
Apr 11, 2025
-
Drag The Line To Finish The Sequence
Apr 11, 2025
-
Which Criterion Fo Rmarket Segmentation Is Lest Liekto To Enable
Apr 11, 2025
-
A Special Order Generally Should Be Accepted If
Apr 11, 2025
Related Post
Thank you for visiting our website which covers about Cost Of Goods Manufactured Is Calculated As Follows . We hope the information provided has been useful to you. Feel free to contact us if you have any questions or need further assistance. See you next time and don't miss to bookmark.