Consider A Cantilever Beam Shown In The Figure Below.
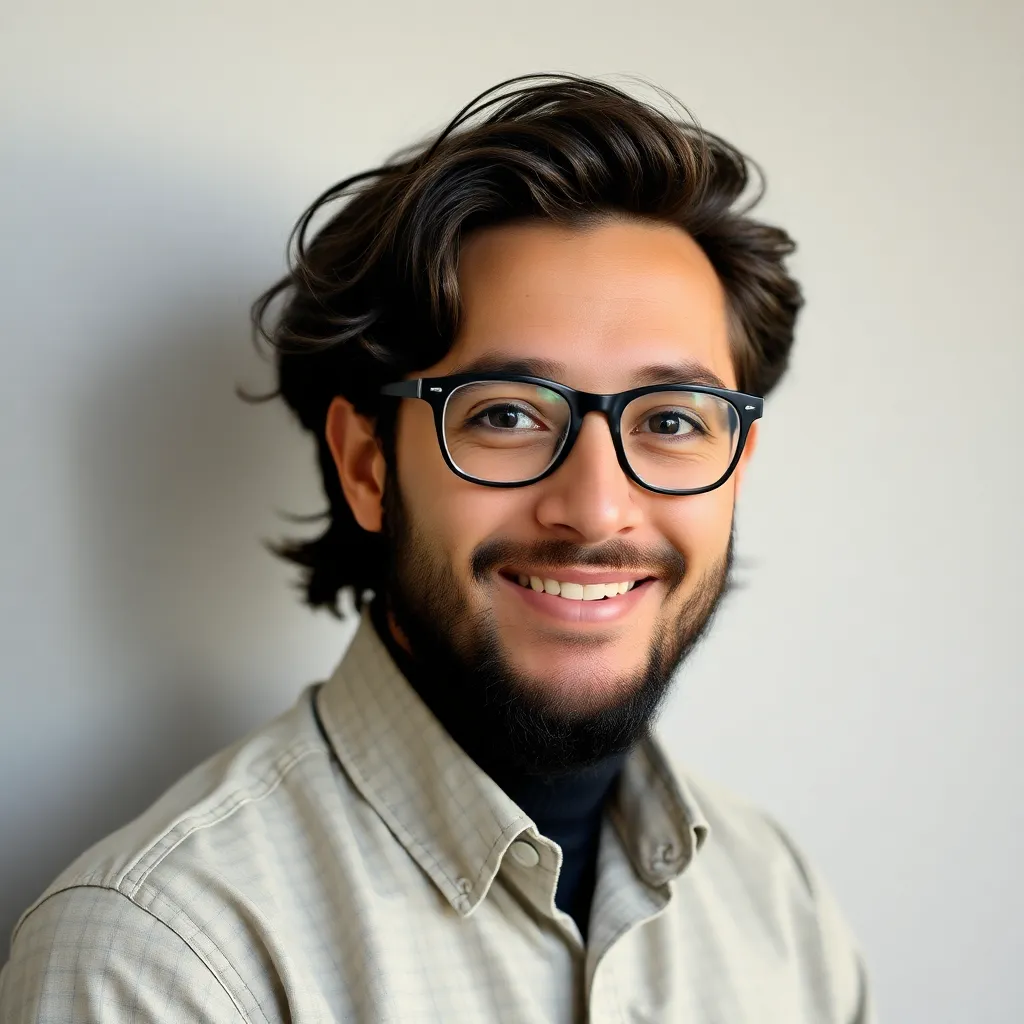
Holbox
Apr 13, 2025 · 7 min read
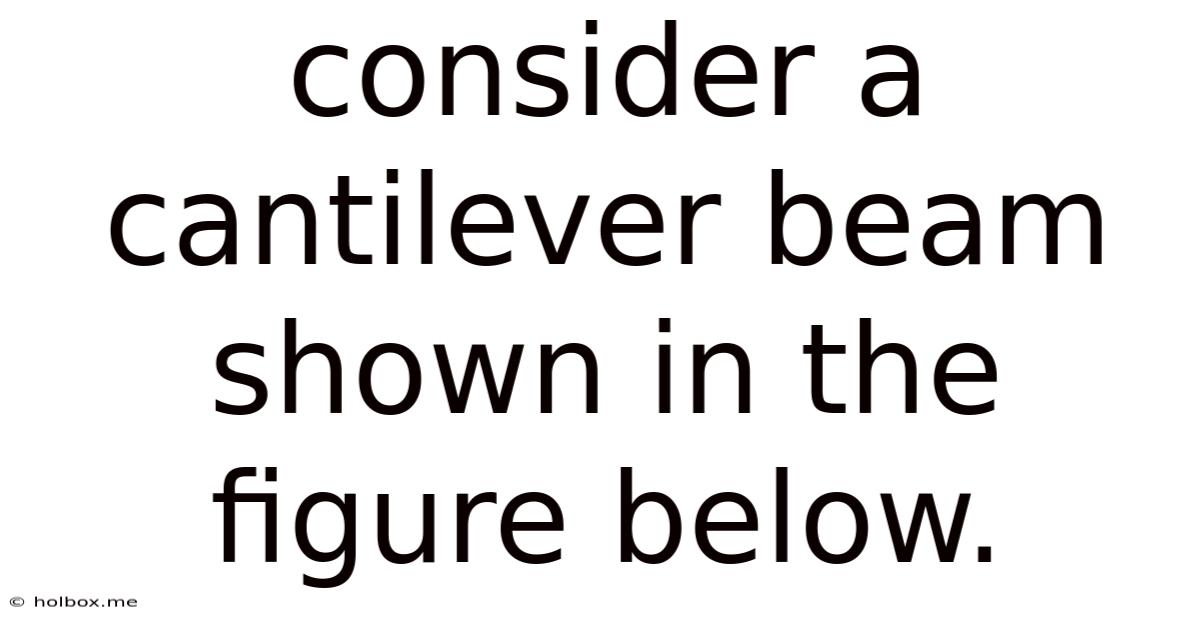
Table of Contents
- Consider A Cantilever Beam Shown In The Figure Below.
- Table of Contents
- Analyzing Cantilever Beams: A Comprehensive Guide
- 1. Concentrated Load (Point Load):
- 2. Uniformly Distributed Load (UDL):
- 3. Uniformly Varying Load (UVL):
- 4. Moment Load:
- 1. Reactions at the Fixed Support:
- 2. Shear Force and Bending Moment Diagrams:
- 3. Deflection:
- 1. Bending Stress:
- 2. Shear Stress:
- Latest Posts
- Latest Posts
- Related Post
Analyzing Cantilever Beams: A Comprehensive Guide
Cantilever beams are structural elements fixed at one end and free at the other, frequently encountered in various engineering applications. Understanding their behavior under load is crucial for ensuring structural integrity and safety. This comprehensive guide delves into the analysis of cantilever beams, covering key concepts, equations, and practical applications. We will explore different loading conditions, deflection calculations, stress analysis, and design considerations.
What is a Cantilever Beam?
A cantilever beam is a structural member rigidly fixed at one end and free at the other. This fixed end provides support and resists both vertical and horizontal forces, as well as moments. The free end is unrestrained, allowing for deflection under load. This unique configuration makes cantilever beams suitable for various applications where a projecting structure is needed, such as balconies, diving boards, and aircraft wings.
Types of Loads on Cantilever Beams
Cantilever beams can experience various loading conditions, each affecting their response differently. The most common load types include:
1. Concentrated Load (Point Load):
A concentrated load acts at a single point on the beam. This is often represented as a force (F) acting vertically downwards. The effect of a concentrated load is localized at the point of application, leading to high stresses and deflections in that area.
Example: A heavy weight placed at the free end of a cantilever beam.
2. Uniformly Distributed Load (UDL):
A uniformly distributed load is a load spread evenly across the entire length of the beam. It's represented as a load intensity (w) measured in units of force per unit length (e.g., N/m or lb/ft). A UDL causes a gradual deflection along the beam's length.
Example: The weight of a uniformly thick beam itself, or a uniformly loaded walkway supported by a cantilever.
3. Uniformly Varying Load (UVL):
A uniformly varying load increases or decreases linearly along the beam's length. It can be represented by a triangular load distribution. The analysis of UVL requires integrating the load distribution to determine the reactions and deflections.
Example: A triangular dam wall resting on a cantilever foundation.
4. Moment Load:
A moment load is a couple acting on the beam, creating a rotational effect. This is represented by a moment (M) applied at a specific point. Moment loads can significantly influence the beam's internal stresses and deflection.
Example: A cantilevered beam supporting a rotating machine which creates a moment on the beam due to the rotation.
Analysis of Cantilever Beams: Key Equations and Concepts
Analyzing cantilever beams involves determining the reactions at the fixed support, the shear force and bending moment diagrams, and the deflection at various points along the beam. Several fundamental equations govern this analysis:
1. Reactions at the Fixed Support:
For a cantilever beam, the fixed support must counteract the applied loads to maintain equilibrium. The reactions consist of a vertical reaction (R) equal to the total vertical load and a moment reaction (M<sub>R</sub>) equal to the total moment acting on the beam.
2. Shear Force and Bending Moment Diagrams:
Shear force and bending moment diagrams are graphical representations of the shear force and bending moment along the beam's length. These diagrams are essential for understanding the internal forces and stresses within the beam. They are usually obtained by considering the equilibrium of sections of the beam.
Key Points about Shear Force and Bending Moment Diagrams:
- Shear Force: The shear force at any point along the beam is the algebraic sum of the vertical forces acting to the left or right of that point.
- Bending Moment: The bending moment at any point is the algebraic sum of the moments of the forces to the left or right of that point about that point.
- Concentrated Load: Causes a sudden change in the shear force diagram and a linear change in the bending moment diagram.
- Uniformly Distributed Load: Causes a linear change in the shear force diagram and a parabolic change in the bending moment diagram.
- Uniformly Varying Load: Causes a parabolic change in the shear force diagram and a cubic change in the bending moment diagram.
3. Deflection:
Deflection refers to the vertical displacement of the beam under load. Calculating deflection is crucial for ensuring the beam remains within acceptable limits and doesn't exceed its allowable deformation. The methods for calculating deflection include:
-
Double Integration Method: This method uses the differential equation of the elastic curve to determine the deflection equation. It involves integrating the bending moment equation twice, with the constants of integration determined from boundary conditions (e.g., zero deflection and zero slope at the fixed end).
-
Superposition Method: This method is used when dealing with multiple loads on the beam by finding the deflection caused by each individual load and then summing them up to find the total deflection.
Equations for Deflection (Illustrative Examples):
-
Concentrated Load (F) at the free end: Maximum deflection, δ<sub>max</sub> = FL³/3EI, where L is the beam length, E is the modulus of elasticity, and I is the area moment of inertia.
-
Uniformly Distributed Load (w) over the entire length: Maximum deflection, δ<sub>max</sub> = wL⁴/8EI.
Understanding Modulus of Elasticity (E) and Area Moment of Inertia (I):
-
Modulus of Elasticity (E): A material property representing its stiffness or resistance to deformation. A higher E indicates greater stiffness.
-
Area Moment of Inertia (I): A geometrical property that depends on the cross-sectional shape of the beam. A larger I indicates greater resistance to bending. The I-value is crucial in structural analysis as it determines how a section distributes stresses under load.
Stress Analysis in Cantilever Beams
Stress analysis helps determine the internal stresses within the beam, particularly bending stress and shear stress.
1. Bending Stress:
Bending stress is caused by the bending moment and is highest at the outermost fibers of the beam. The bending stress (σ) is calculated using the bending stress formula:
σ = My/I
where:
- M is the bending moment
- y is the distance from the neutral axis to the outermost fiber
- I is the area moment of inertia
2. Shear Stress:
Shear stress is caused by the shear force and is generally highest near the neutral axis. The shear stress calculation varies depending on the beam's cross-section.
Design Considerations for Cantilever Beams
Designing cantilever beams involves selecting appropriate materials, dimensions, and ensuring the beam's strength and stiffness meet the required criteria. Key considerations include:
-
Material Selection: Choosing a material with high strength, stiffness (high E), and appropriate durability.
-
Cross-sectional Shape: Optimizing the beam's cross-section to maximize the area moment of inertia (I) for improved bending resistance. Common shapes include rectangular, I-beams, and T-beams, each offering different strengths and stiffness characteristics.
-
Deflection Limits: Ensuring the maximum deflection under load remains within acceptable limits to prevent damage or excessive vibrations. These limits are often specified in design codes.
-
Stress Limits: Verifying that the maximum bending and shear stresses within the beam remain below the material's allowable stress limits to prevent failure.
-
Fatigue Considerations: For beams subjected to repeated or cyclic loading, fatigue analysis is essential to account for potential fatigue failure.
-
Buckling: For slender cantilever beams, buckling may be a concern, especially under compressive loads. Buckling analysis may be necessary to ensure stability.
Practical Applications of Cantilever Beams
Cantilever beams are used extensively in various engineering disciplines:
- Civil Engineering: Bridges, balconies, building overhangs, retaining walls, highway signs.
- Mechanical Engineering: Aircraft wings, robotic arms, machine components, spring leaves, diving boards.
- Aerospace Engineering: Aircraft wings, helicopter rotor blades, satellite components.
Conclusion
The analysis of cantilever beams is a fundamental aspect of structural engineering and mechanics. Understanding the principles of load distribution, shear force and bending moment diagrams, deflection calculations, and stress analysis is crucial for designing safe and efficient structures. This guide provides a comprehensive overview of the key concepts, equations, and design considerations involved in cantilever beam analysis, equipping engineers and students with the necessary knowledge for tackling diverse engineering challenges. Remember that this guide provides a theoretical foundation; practical applications often require more sophisticated analysis techniques and consideration of factors beyond the scope of this article, including material imperfections, temperature effects, and dynamic loading. Consult relevant design codes and standards for specific applications.
Latest Posts
Latest Posts
-
An It Company Commissions A New Software For Human Resources
Apr 25, 2025
-
When Is The Predetermined Manufacturing Overhead Rate Computed
Apr 25, 2025
-
Assign Each Characteristic To The Appropriate Type Of Muscle
Apr 25, 2025
-
Why Is Iodine Called An Indicator
Apr 25, 2025
-
The Current Amplitude I Versus Driving Angular
Apr 25, 2025
Related Post
Thank you for visiting our website which covers about Consider A Cantilever Beam Shown In The Figure Below. . We hope the information provided has been useful to you. Feel free to contact us if you have any questions or need further assistance. See you next time and don't miss to bookmark.