Companies Use Job Cost Sheets To Track The Costs Of:
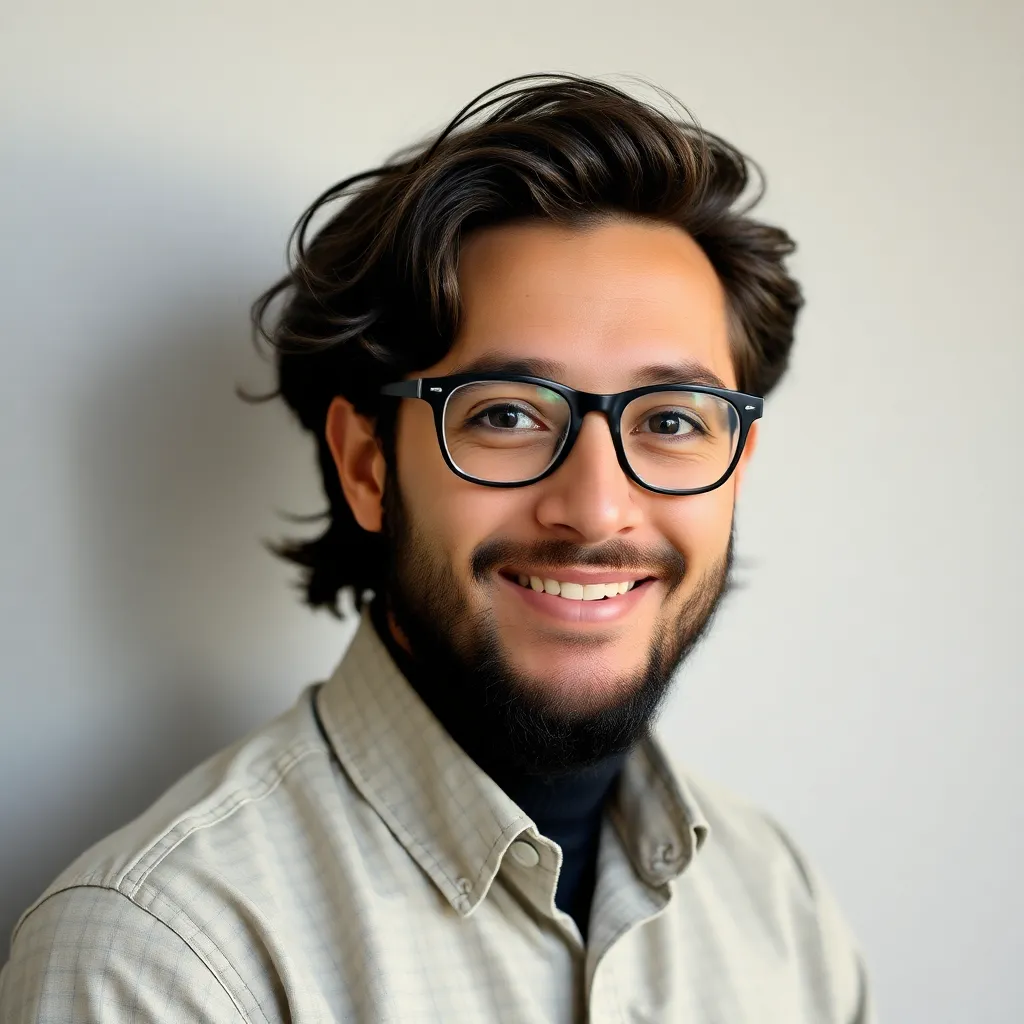
Holbox
Apr 04, 2025 · 7 min read

Table of Contents
- Companies Use Job Cost Sheets To Track The Costs Of:
- Table of Contents
- Companies Use Job Cost Sheets to Track the Costs of: A Comprehensive Guide
- What Costs Do Job Cost Sheets Track?
- 1. Direct Materials Costs:
- 2. Direct Labor Costs:
- 3. Manufacturing Overhead Costs:
- 4. General and Administrative Costs:
- The Importance of Job Cost Sheets
- 1. Accurate Project Pricing:
- 2. Profitability Analysis:
- 3. Budget Control and Monitoring:
- 4. Improved Efficiency and Resource Allocation:
- 5. Enhanced Decision-Making:
- 6. Client Billing and Invoicing:
- 7. Inventory Management:
- How Job Cost Sheets are Used in Different Industries
- 1. Construction:
- 2. Manufacturing:
- 3. Software Development:
- 4. Consulting:
- 5. Advertising and Marketing Agencies:
- Implementing Effective Job Costing
- Conclusion:
- Latest Posts
- Latest Posts
- Related Post
Companies Use Job Cost Sheets to Track the Costs of: A Comprehensive Guide
Job costing is a crucial accounting method employed by businesses to meticulously track the expenses associated with individual projects or jobs. Unlike process costing, which averages costs across a large volume of identical products, job costing provides a granular view of each project's financial performance. This granular level of detail empowers businesses to make informed decisions, optimize resource allocation, and ultimately enhance profitability. This article delves deep into the multifaceted aspects of job cost sheets, exploring what they track, their importance, and how they contribute to a company's financial health.
What Costs Do Job Cost Sheets Track?
Job cost sheets are comprehensive documents that capture a wide spectrum of expenses related to a specific project. The specific costs tracked will vary depending on the nature of the business and the complexity of the project, but generally encompass the following categories:
1. Direct Materials Costs:
These are the raw materials directly used in the production or completion of a specific job. For example:
- Manufacturing: Wood, metal, fabric, electronic components.
- Construction: Cement, lumber, bricks, steel.
- Software Development: Purchased software licenses, specific hardware components.
- Consulting: Specialized software subscriptions used for the project.
Accurate tracking of direct materials is crucial. This necessitates a system for meticulously recording the quantity and cost of materials used on each job. Discrepancies can lead to inaccurate cost estimations and ultimately, project losses.
2. Direct Labor Costs:
This represents the wages and benefits paid to employees directly involved in the project. This includes:
- Hourly wages: The basic pay of workers involved in the project.
- Overtime pay: Compensation for extra hours worked.
- Employee benefits: Health insurance, retirement contributions, paid time off.
Identifying and allocating direct labor costs effectively is vital. Time tracking systems and accurate record-keeping are indispensable to ensure that labor costs are accurately assigned to the correct jobs.
3. Manufacturing Overhead Costs:
These are indirect costs incurred in the production process that cannot be directly traced to a specific job. They are often allocated to jobs based on a predetermined overhead rate. Examples include:
- Factory rent: Cost of leasing or owning the manufacturing facility.
- Utilities: Electricity, water, gas used in the production process.
- Depreciation of equipment: The gradual decline in value of machinery used in production.
- Factory insurance: Insurance coverage for the factory and its equipment.
- Maintenance and repairs: Costs associated with maintaining factory equipment.
- Supervisory salaries: Salaries of managers overseeing production.
Accurately allocating overhead costs is a complex but crucial step. Using a suitable allocation base, such as direct labor hours or machine hours, ensures fair distribution across projects.
4. General and Administrative Costs:
These are indirect costs related to the overall administration and management of the business, not directly attributable to any single project. While not always included on a job cost sheet, they can significantly impact the profitability analysis of a job when considered in overall project evaluation. Examples include:
- Salaries of administrative staff: Office managers, accounting staff, HR personnel.
- Office rent and utilities: Costs associated with maintaining office space.
- Legal and professional fees: Expenses related to legal counsel or consulting services.
- Marketing and advertising: Promoting the business and its services.
While not directly included in individual job cost sheets, understanding these costs is vital for overall profitability assessment. They should be factored into the final pricing of projects to ensure the business operates sustainably.
The Importance of Job Cost Sheets
The use of job cost sheets extends far beyond simple cost tracking. They are essential for several reasons:
1. Accurate Project Pricing:
By meticulously recording all direct and indirect costs, businesses can accurately determine the true cost of each project. This allows for more realistic and profitable pricing strategies, avoiding underselling and ensuring project viability.
2. Profitability Analysis:
Job cost sheets provide a detailed breakdown of all project expenses, enabling businesses to assess the profitability of each individual project. This data allows for identifying both profitable and unprofitable jobs, informing future decision-making and strategic planning.
3. Budget Control and Monitoring:
Through continuous tracking and comparison against predetermined budgets, job cost sheets facilitate effective budget control. Any deviations from the budget are quickly identified, enabling timely corrective actions to prevent cost overruns.
4. Improved Efficiency and Resource Allocation:
Analyzing job cost data can uncover areas of inefficiency within the production process. This information can be leveraged to optimize resource allocation, streamline workflows, and ultimately improve overall productivity.
5. Enhanced Decision-Making:
Comprehensive cost data from job cost sheets enables informed decision-making across various aspects of the business. This includes decisions regarding project acceptance, pricing strategies, resource allocation, and process improvement initiatives.
6. Client Billing and Invoicing:
Job cost sheets serve as a reliable source of information for accurate client billing and invoicing. This ensures that businesses receive fair compensation for the services rendered, while maintaining transparent and accurate financial records.
7. Inventory Management:
For businesses that use a significant amount of materials, job cost sheets help track materials consumption, aiding in the management of inventory levels. This helps minimize waste, reduce storage costs, and prevent stockouts.
How Job Cost Sheets are Used in Different Industries
The application of job cost sheets varies slightly depending on the industry, but the core principles remain consistent.
1. Construction:
In construction, job cost sheets meticulously track the costs of materials like cement, lumber, and steel; labor costs of workers, foremen, and subcontractors; and overhead costs including equipment rental, permits, and insurance.
2. Manufacturing:
Manufacturers use job cost sheets to track direct materials like raw materials and components; direct labor costs of assembly line workers and specialized technicians; and overhead costs such as factory rent, utilities, and machine depreciation.
3. Software Development:
Software development companies use job cost sheets to track the costs of purchased software licenses, hardware, developer salaries, testing expenses, and project management costs.
4. Consulting:
Consulting firms use job cost sheets to track consultant fees, travel expenses, research costs, software subscriptions, and other project-related expenses. These sheets are crucial for accurate project pricing and billing.
5. Advertising and Marketing Agencies:
These agencies use job cost sheets to track employee hours, media buys, design and production costs, printing and distribution costs, and other expenses associated with specific marketing campaigns. This data is essential for reporting to clients and measuring campaign effectiveness.
Implementing Effective Job Costing
Implementing a successful job costing system requires careful planning and execution. Key considerations include:
-
Choosing the right software: Investing in appropriate accounting software can significantly streamline the process, automating data entry and providing insightful reports.
-
Establishing a clear coding system: Developing a consistent and easily understandable coding system for materials, labor, and overhead costs is crucial for accurate data tracking.
-
Implementing robust time-tracking methods: Accurate time tracking is crucial for allocating labor costs correctly. This can involve timesheets, project management software, or other methods.
-
Developing a reliable overhead allocation method: Selecting an appropriate method for allocating overhead costs—such as direct labor hours or machine hours—is crucial for fair cost distribution.
-
Regularly reviewing and refining the system: Regular reviews and adjustments ensure the system remains effective and accurate, adapting to changing business needs.
-
Training employees: Proper employee training is crucial for accurate data entry and the effective use of the job costing system.
Conclusion:
Job cost sheets are an indispensable tool for businesses seeking to gain granular control over project costs, improve profitability, and make informed decisions. By meticulously tracking direct materials, direct labor, and overhead costs, businesses can accurately assess project performance, optimize resource allocation, and achieve greater financial success. Investing time and resources in developing and implementing a robust job costing system is an investment in the long-term health and sustainability of any project-based business. The detailed insights provided by job cost sheets empower businesses to thrive in competitive markets by ensuring efficient operations, accurate pricing, and maximized profitability.
Latest Posts
Latest Posts
-
Block Diagram Analysis And Interpretation Activity 10 6
Apr 14, 2025
-
Ways Of The World 5th Edition
Apr 14, 2025
-
Provide The Correct Iupac Systematic Name For The Following Compound
Apr 14, 2025
-
Select All Of The Following That Are True About Protists
Apr 14, 2025
-
Which Of The Following Is Not A Function Of Lipids
Apr 14, 2025
Related Post
Thank you for visiting our website which covers about Companies Use Job Cost Sheets To Track The Costs Of: . We hope the information provided has been useful to you. Feel free to contact us if you have any questions or need further assistance. See you next time and don't miss to bookmark.