Bourdon Gauges Are Commonly Used To Measure
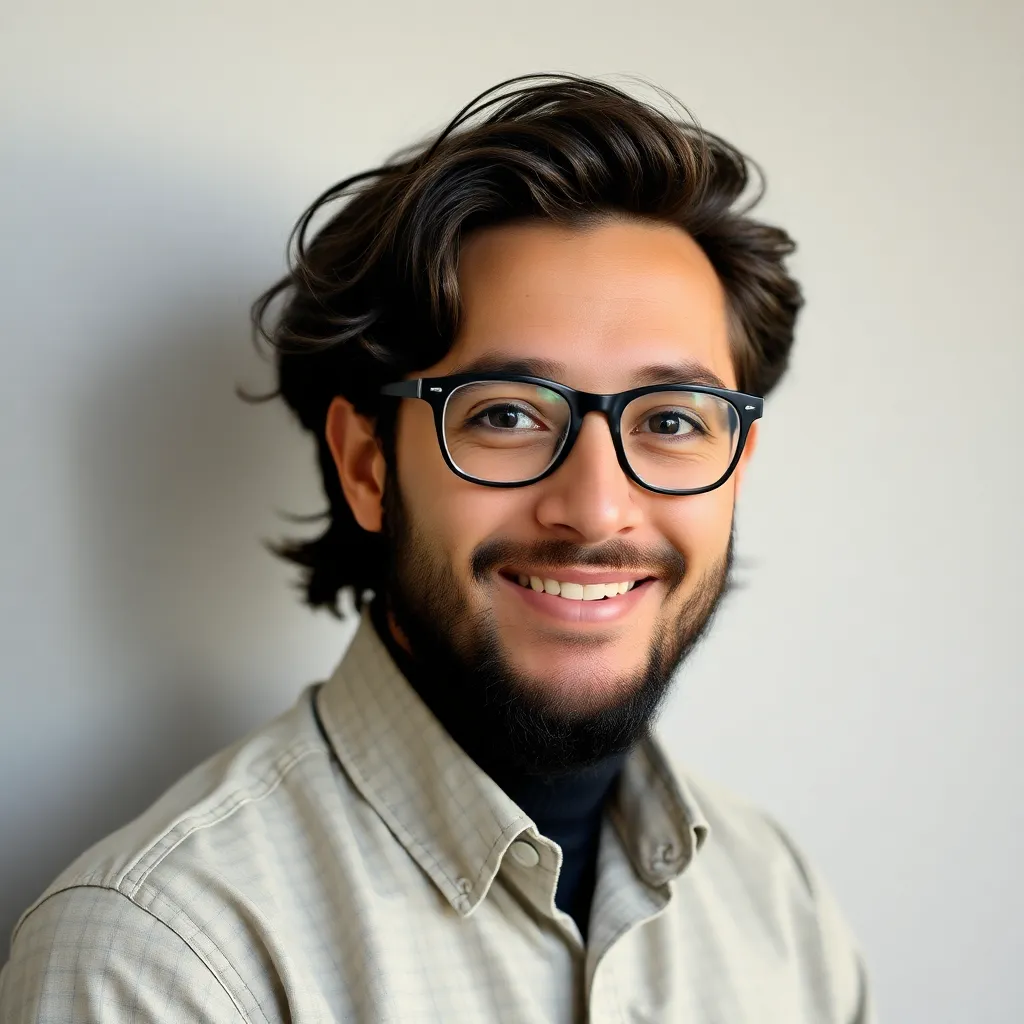
Holbox
Apr 06, 2025 · 6 min read

Table of Contents
- Bourdon Gauges Are Commonly Used To Measure
- Table of Contents
- Bourdon Gauges: Commonly Used to Measure Pressure
- Understanding the Mechanics of a Bourdon Gauge
- How the Deflection is Measured:
- Key Components of a Bourdon Gauge:
- Advantages of Bourdon Gauges:
- Applications of Bourdon Gauges:
- Types of Bourdon Gauges:
- Limitations of Bourdon Gauges:
- Calibration and Maintenance of Bourdon Gauges:
- Selecting the Right Bourdon Gauge:
- Future Trends in Bourdon Gauge Technology:
- Conclusion:
- Latest Posts
- Latest Posts
- Related Post
Bourdon Gauges: Commonly Used to Measure Pressure
Bourdon gauges are ubiquitous in various industries, serving as reliable instruments for pressure measurement. Their widespread use stems from a combination of factors including their robust design, relative affordability, and ease of use. This comprehensive guide delves deep into the world of Bourdon gauges, exploring their working principles, applications, advantages, limitations, and future trends.
Understanding the Mechanics of a Bourdon Gauge
At its core, a Bourdon gauge is a simple yet ingenious device that leverages the principle of elasticity. The heart of the gauge is the Bourdon tube, a C-shaped or helical tube with an elliptical cross-section. When pressure is applied to the inside of the tube, the elliptical cross-section attempts to become circular. This causes the tube to straighten slightly, a deflection that is proportional to the applied pressure.
How the Deflection is Measured:
This minute straightening of the Bourdon tube is then mechanically amplified. The end of the tube is connected to a linkage system, which translates the subtle movement into a larger, more readily measurable rotation. This rotation drives a pointer across a calibrated dial, indicating the pressure value.
- C-shaped tubes: These are commonly used for measuring lower pressures and offer a good balance between sensitivity and robustness.
- Helical tubes: These are more sensitive and suitable for measuring higher pressures due to their longer length and increased deflection. They are also more resistant to vibration.
Key Components of a Bourdon Gauge:
- Bourdon Tube: The pressure-sensing element.
- Linkage System: Translates the tube's movement into pointer rotation.
- Pointer: Indicates the pressure reading on the dial.
- Dial: A calibrated scale showing pressure units (e.g., psi, bar, kPa).
- Case: Protects the internal components from environmental factors.
Advantages of Bourdon Gauges:
Bourdon gauges offer several advantages that contribute to their enduring popularity:
- Simplicity and Robustness: Their relatively straightforward design makes them highly reliable and easy to maintain. They can withstand harsh environments and vibrations.
- Direct Reading: Pressure is indicated directly on the dial, eliminating the need for complex calculations or interpretations.
- Cost-Effectiveness: Bourdon gauges are generally less expensive than other pressure measurement technologies, making them accessible for a wide range of applications.
- Wide Pressure Range: Bourdon gauges are available in a wide range of pressure scales, from vacuum to extremely high pressures, catering to diverse needs.
- Easy Installation: Their compact size and simple connection methods simplify installation.
Applications of Bourdon Gauges:
The versatility of Bourdon gauges makes them indispensable across a multitude of industries and applications. Some key examples include:
- HVAC Systems: Monitoring pressures in air conditioning and refrigeration systems.
- Industrial Processes: Measuring pressures in manufacturing processes, pipelines, and compressed air systems.
- Automotive Industry: Used in various automotive applications, including tire pressure monitoring and engine pressure sensing.
- Hydraulic Systems: Measuring pressures in hydraulic machinery and systems.
- Pneumatic Systems: Measuring pressures in compressed air systems.
- Medical Equipment: In some medical devices requiring pressure measurement.
- Water Treatment Plants: Monitoring water pressure throughout the process.
- Oil and Gas Industry: Pressure monitoring in drilling, extraction, and refining.
Types of Bourdon Gauges:
While the fundamental principle remains the same, several variations of Bourdon gauges exist, each designed for specific applications:
- Liquid-Filled Gauges: These gauges contain a liquid (usually glycerine) within the case to dampen oscillations and protect the gauge from damage caused by pulsating pressures or vibrations. This enhances the gauge's longevity and accuracy, particularly in harsh conditions.
- Dry Gauges: These are simpler and less expensive than liquid-filled gauges but are more susceptible to damage from vibration and pulsating pressures. They are suitable for applications with relatively stable and steady pressure.
- Compound Gauges: These gauges display both positive and negative pressures (vacuum and pressure) on a single dial. This is useful in applications where both vacuum and positive pressure monitoring are required.
- Dial Gauges: The most common type, with pressure displayed directly on a circular dial.
- Digital Gauges: Combining the simplicity of Bourdon tubes with digital readout capabilities, these offer enhanced precision and readability. These usually incorporate a sensor that measures the Bourdon tube deflection, and a display unit shows the digital reading.
Limitations of Bourdon Gauges:
Despite their numerous advantages, Bourdon gauges do have certain limitations:
- Accuracy: While generally accurate, they are not as precise as some other pressure measurement technologies, such as digital pressure transducers.
- Sensitivity to Vibrations: Dry Bourdon gauges can be affected by vibrations, potentially leading to inaccurate readings or damage.
- Hysteresis: A slight difference in readings may occur depending on whether the pressure is increasing or decreasing (due to the elasticity of the tube).
- Limited Lifespan: The Bourdon tube can fatigue over time, leading to inaccuracies or failure. Regular calibration and replacement are necessary.
- Temperature Sensitivity: The accuracy of the gauge can be affected by temperature fluctuations.
Calibration and Maintenance of Bourdon Gauges:
Regular calibration and maintenance are crucial for ensuring the accuracy and longevity of Bourdon gauges. Calibration involves comparing the gauge reading to a known standard, typically a deadweight tester or another high-accuracy pressure gauge. Regular maintenance involves checking for any damage to the tube or linkage system, ensuring proper cleanliness, and lubrication of moving parts as necessary.
Selecting the Right Bourdon Gauge:
Choosing the right Bourdon gauge involves considering several factors:
- Pressure Range: Select a gauge with a pressure range that encompasses the expected pressure values.
- Accuracy Required: Consider the level of accuracy needed for the application.
- Type of Gauge: Choose between liquid-filled or dry, depending on the application environment and the presence of vibrations.
- Material Compatibility: Ensure the gauge's construction materials are compatible with the process fluid.
- Size and Mounting: Select a gauge size and mounting style that is suitable for the installation location.
Future Trends in Bourdon Gauge Technology:
While Bourdon gauges have been a mainstay for decades, ongoing innovations are refining their performance and expanding their capabilities:
- Integration with Smart Sensors: Incorporating smart sensors to provide remote monitoring capabilities, data logging, and predictive maintenance alerts.
- Improved Materials: Utilizing advanced materials to enhance durability, lifespan, and resistance to harsh environmental conditions.
- Miniaturization: Developing smaller and more compact designs for applications with space constraints.
- Enhanced Accuracy: Improving manufacturing processes and designs to achieve greater precision and reduce hysteresis.
Conclusion:
Bourdon gauges remain a cornerstone of pressure measurement technology due to their simplicity, reliability, and cost-effectiveness. While newer technologies offer higher precision in certain applications, the robustness and ease of use of Bourdon gauges ensure their continued relevance across a broad spectrum of industries. Understanding their working principles, limitations, and maintenance requirements is crucial for maximizing their performance and longevity. By carefully selecting the appropriate gauge and implementing proper maintenance practices, users can leverage the many advantages of this time-tested pressure measurement technology.
Latest Posts
Latest Posts
-
Which Is A Wildlife Characteristic To Consider When Identifying Game
Apr 13, 2025
-
Freight Charges On Goods Sold Are Accounted For As
Apr 13, 2025
-
Anatomy And Physiology The Unity Of Form And Function
Apr 13, 2025
-
Which Of The Following Exemplifies The Empirical Method
Apr 13, 2025
-
Agglutinogens Of The Various Blood Types Are Examples Of
Apr 13, 2025
Related Post
Thank you for visiting our website which covers about Bourdon Gauges Are Commonly Used To Measure . We hope the information provided has been useful to you. Feel free to contact us if you have any questions or need further assistance. See you next time and don't miss to bookmark.