Both Direct Materials And Indirect Materials Are
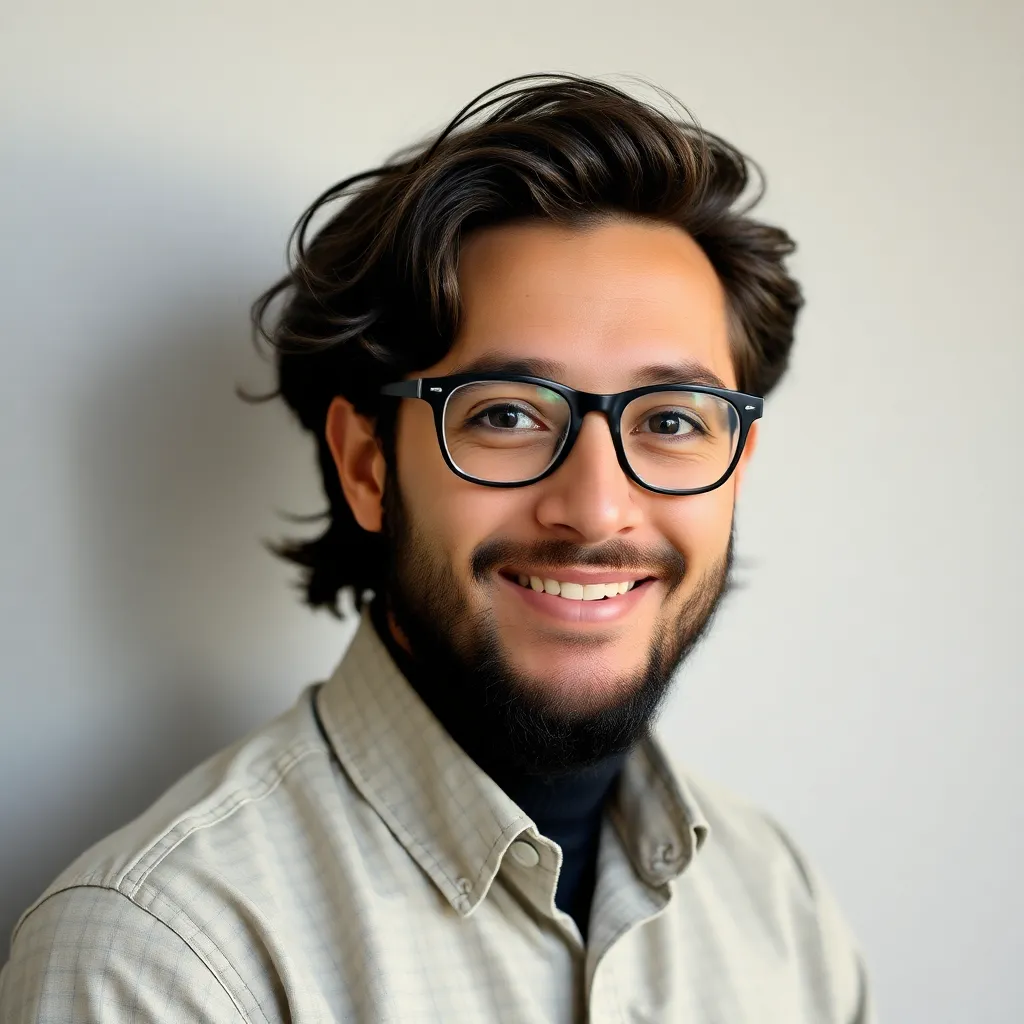
Holbox
May 09, 2025 · 6 min read
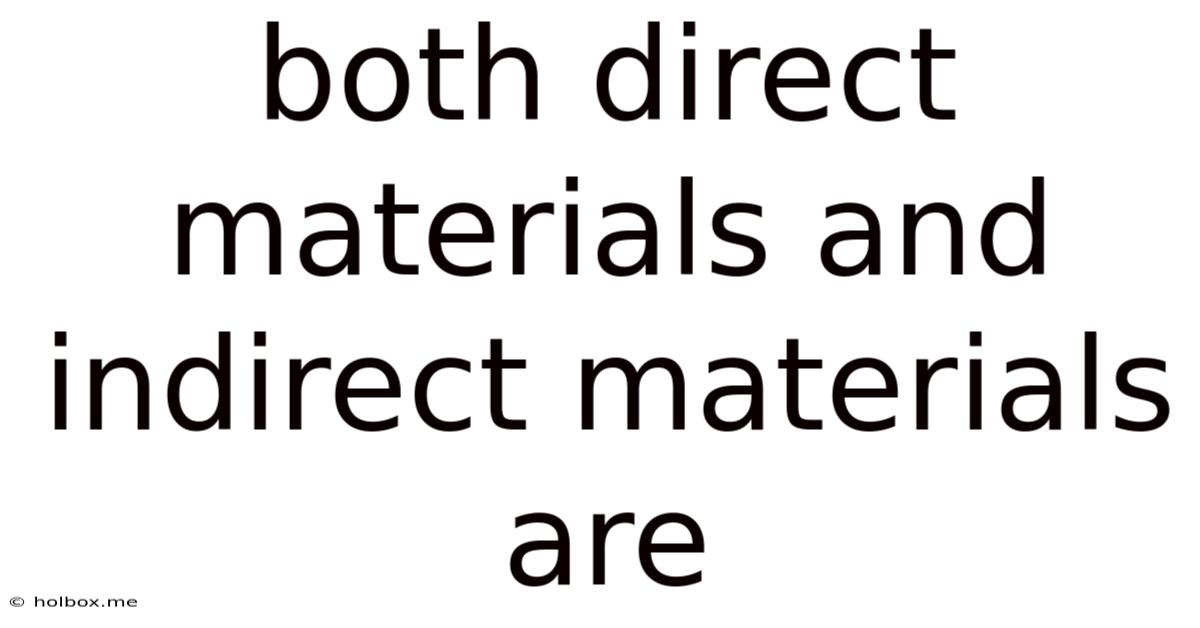
Table of Contents
- Both Direct Materials And Indirect Materials Are
- Table of Contents
- Both Direct Materials and Indirect Materials Are: A Comprehensive Guide to Understanding Material Costs in Manufacturing
- What are Direct Materials?
- Key Characteristics of Direct Materials:
- Examples of Direct Materials:
- What are Indirect Materials?
- Key Characteristics of Indirect Materials:
- Examples of Indirect Materials:
- The Impact on Costing: Direct vs. Indirect Materials
- Cost Allocation Methods for Indirect Materials:
- Managing Direct and Indirect Materials Effectively
- Strategies for Managing Direct Materials:
- Strategies for Managing Indirect Materials:
- The Importance of Accurate Record Keeping
- The Interplay Between Direct and Indirect Materials
- Conclusion: A Holistic Approach to Material Management
- Latest Posts
- Related Post
Both Direct Materials and Indirect Materials Are: A Comprehensive Guide to Understanding Material Costs in Manufacturing
Understanding the different types of materials used in manufacturing is crucial for accurate cost accounting and efficient production planning. This article delves deep into the crucial distinction between direct materials and indirect materials, exploring their definitions, examples, how they impact costing, and their role in overall business profitability. We'll also touch upon best practices for managing both types effectively.
What are Direct Materials?
Direct materials are the raw materials that are directly used in the production process and can be easily traced to the finished goods. These materials form the essential components of the final product, and their cost is directly attributable to the manufactured item. Think of them as the core ingredients of your product recipe. The more direct materials you use, generally the higher the cost of the product. Accurate tracking and cost management of direct materials are therefore critical to profitability.
Key Characteristics of Direct Materials:
- Directly traceable: You can easily identify and quantify the amount of direct material used in each finished product.
- Significant cost: The cost of direct materials represents a substantial portion of the total cost of goods sold (COGS).
- Essential components: They are fundamental to the product's functionality and physical existence.
- Easily quantifiable: The amount used per unit can be accurately measured and recorded.
Examples of Direct Materials:
The examples of direct materials will vary vastly depending on the industry. However, here are some illustrative examples across different sectors:
- Manufacturing: Steel for automobiles, wood for furniture, fabric for clothing, silicon for semiconductors, plastic for toys.
- Food Processing: Flour for bread, sugar for candy, meat for sausages, coffee beans for coffee.
- Construction: Cement, bricks, timber, steel bars, roofing tiles.
What are Indirect Materials?
Indirect materials, unlike their direct counterparts, are materials used in the production process that are not easily traced to specific finished products. They are essential for manufacturing, but their cost cannot be directly linked to a single unit. These materials are often consumed in smaller quantities and contribute to the overall manufacturing process rather than being a core component of the final product.
Key Characteristics of Indirect Materials:
- Difficult to trace: It's impractical or impossible to track their usage for each individual product.
- Minor cost: Their cost is relatively small compared to direct materials.
- Supporting role: They support the production process but aren't directly incorporated into the finished product.
- Often consumed in bulk: Purchased in larger quantities for general use.
Examples of Indirect Materials:
Again, the specific examples vary based on the industry. Here are some illustrations:
- Manufacturing: Cleaning supplies, lubricants for machinery, small tools (screwdrivers, wrenches), adhesives, sandpaper.
- Food Processing: Cleaning agents for equipment, packaging materials (boxes, labels), small repair parts for machinery.
- Construction: Lubricants for heavy machinery, cleaning supplies for tools and equipment, small hardware items.
The Impact on Costing: Direct vs. Indirect Materials
The distinction between direct and indirect materials is crucial for accurate cost accounting. Direct material costs are directly added to the cost of goods sold (COGS) for each unit produced, contributing directly to the product's selling price. In contrast, indirect material costs are considered part of manufacturing overhead and are allocated to products based on predetermined methods, such as machine hours or direct labor costs.
Cost Allocation Methods for Indirect Materials:
Several methods are used to allocate indirect material costs to products, including:
- Predetermined Overhead Rate: A predetermined rate, calculated based on historical data or projections, is used to allocate indirect costs.
- Activity-Based Costing (ABC): This more sophisticated method allocates costs based on specific activities involved in the production process.
- Plantwide Overhead Rate: A single overhead rate is used for the entire plant, simplifying the allocation process but potentially lacking precision.
Managing Direct and Indirect Materials Effectively
Efficient management of both direct and indirect materials is critical for optimizing production costs and maintaining profitability. Effective management involves several key strategies:
Strategies for Managing Direct Materials:
- Inventory Management: Implementing robust inventory control systems like Just-in-Time (JIT) inventory to minimize storage costs and waste.
- Supplier Relationships: Developing strong relationships with reliable suppliers to ensure timely delivery and consistent quality.
- Quality Control: Establishing stringent quality control procedures to reduce material defects and minimize waste.
- Demand Forecasting: Accurately forecasting demand to optimize purchasing decisions and prevent stockouts or overstocking.
- Material Requirements Planning (MRP): Using MRP systems to plan material needs based on production schedules and inventory levels.
Strategies for Managing Indirect Materials:
- Centralized Purchasing: Consolidating purchasing to negotiate better prices and streamline the procurement process.
- Inventory Control: Implementing a system to manage the inventory of indirect materials, preventing shortages and excessive stock.
- Standardization: Using standardized indirect materials wherever possible to reduce variety and simplify inventory management.
- Waste Reduction: Implementing programs to minimize waste and improve efficiency in the use of indirect materials.
- Regular Audits: Conducting regular audits to ensure that indirect materials are being used efficiently and that costs are controlled.
The Importance of Accurate Record Keeping
Maintaining accurate records for both direct and indirect materials is paramount. This ensures the accuracy of cost calculations, facilitates efficient inventory management, and provides valuable data for decision-making. A well-organized system will allow you to:
- Track material usage: Know precisely how much of each material is used in production.
- Monitor costs: Keep a close eye on the cost of materials over time to identify trends and potential areas for cost savings.
- Identify waste: Pinpoint areas where materials are being wasted or used inefficiently.
- Improve purchasing decisions: Make informed decisions about purchasing materials based on accurate data.
- Comply with regulations: Ensure compliance with industry regulations related to material handling and disposal.
The Interplay Between Direct and Indirect Materials
While distinct, direct and indirect materials are interconnected within the manufacturing process. Efficient management of one directly impacts the other. For instance, a breakdown in the supply of indirect materials, such as lubricants, could halt production, impacting the consumption of direct materials and overall output. Conversely, poor inventory management of direct materials can lead to production delays, increasing the consumption of indirect materials (e.g., overtime pay for workers).
Conclusion: A Holistic Approach to Material Management
Successfully navigating the complexities of manufacturing requires a well-rounded understanding of both direct and indirect materials. By implementing effective strategies for managing both, businesses can significantly reduce costs, optimize production processes, and ultimately improve profitability. Remember that accurate record keeping, efficient inventory control, and strategic supplier relationships are critical components of a successful material management strategy. A holistic approach, considering the interplay between these two categories, is key to long-term success in any manufacturing environment. Continuous improvement and adaptation to changing market conditions will ensure your business stays competitive and profitable.
Latest Posts
Related Post
Thank you for visiting our website which covers about Both Direct Materials And Indirect Materials Are . We hope the information provided has been useful to you. Feel free to contact us if you have any questions or need further assistance. See you next time and don't miss to bookmark.