An Organization That Fully Adopts The Six Sigma Methodology
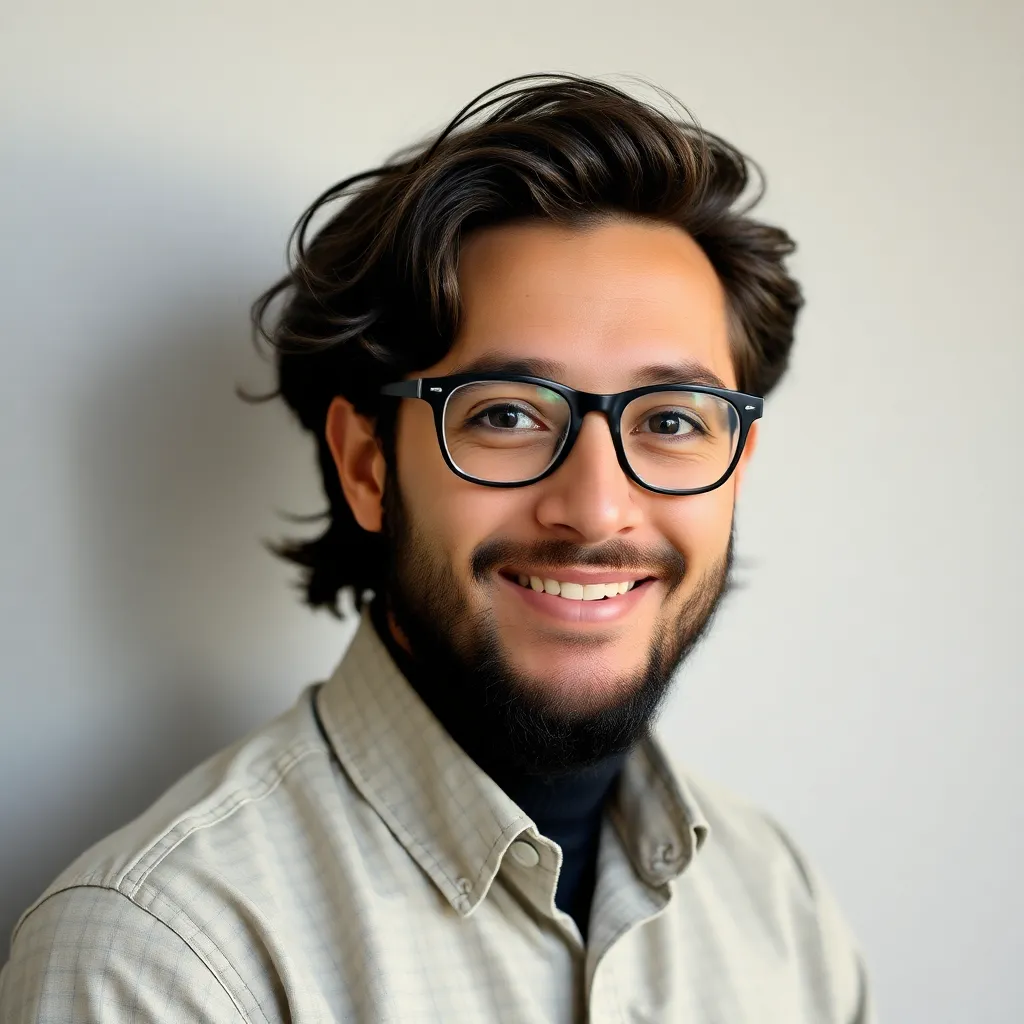
Holbox
Apr 05, 2025 · 6 min read

Table of Contents
- An Organization That Fully Adopts The Six Sigma Methodology
- Table of Contents
- Achieving Operational Excellence: A Case Study of Six Sigma Implementation at a Hypothetical Organization
- Phase 1: Building a Foundation for Success
- Champion Selection and Team Building:
- Training and Education:
- Defining Key Performance Indicators (KPIs):
- Project Selection:
- Phase 2: Implementing Six Sigma Projects
- Define:
- Measure:
- Analyze:
- Improve:
- Control:
- Phase 3: Expanding and Sustaining Six Sigma
- Scaling Six Sigma Across Departments:
- Embedding Six Sigma in the Organizational Culture:
- Measuring and Reporting on Results:
- Continuous Improvement Initiatives:
- Challenges Faced and Lessons Learned
- Quantifiable Results and Impact
- Conclusion: Sustaining the Six Sigma Journey
- Latest Posts
- Latest Posts
- Related Post
Achieving Operational Excellence: A Case Study of Six Sigma Implementation at a Hypothetical Organization
The pursuit of operational excellence is a continuous journey, demanding unwavering commitment and a robust methodology. Six Sigma, with its data-driven approach and focus on minimizing defects, has proven to be a powerful tool for organizations seeking significant improvements in quality, efficiency, and profitability. This article delves into a hypothetical case study, exploring how a fictional organization, "InnovateTech," successfully implemented Six Sigma across its operations, achieving remarkable results. We'll examine the key stages of their journey, the challenges faced, and the ultimate impact on the organization's performance and culture.
Phase 1: Building a Foundation for Success
InnovateTech, a mid-sized manufacturer of advanced electronics, recognized the need for a comprehensive improvement strategy. Years of incremental changes had yielded only marginal gains, and competition was intensifying. Their leadership team, understanding the potential of Six Sigma, initiated a phased rollout. This first phase focused on laying the groundwork for successful implementation.
Champion Selection and Team Building:
A critical first step was identifying champions—high-level executives who would actively support and sponsor the initiative. These champions were instrumental in securing resources, overcoming resistance, and ensuring alignment across departments. They also played a vital role in selecting and training Black Belts (highly skilled Six Sigma experts) and Green Belts (employees trained in Six Sigma principles who apply them to their projects).
Training and Education:
InnovateTech invested heavily in comprehensive Six Sigma training for all levels of employees. This wasn't just a technical training program; it emphasized the importance of a data-driven culture, problem-solving skills, and teamwork. The training covered DMAIC (Define, Measure, Analyze, Improve, Control), the core methodology of Six Sigma, and provided practical tools and techniques for applying it to real-world problems.
Defining Key Performance Indicators (KPIs):
Before embarking on projects, InnovateTech defined clear and measurable KPIs aligned with its strategic goals. These KPIs provided a baseline for measuring progress and demonstrating the impact of Six Sigma initiatives. Examples included reducing defect rates in manufacturing, improving customer satisfaction scores, and shortening lead times.
Project Selection:
The initial projects were carefully selected based on their potential impact, feasibility, and alignment with organizational priorities. Projects were chosen across different departments to showcase the versatility of Six Sigma and encourage cross-functional collaboration. This inclusive approach helped build momentum and demonstrate the benefits early on.
Phase 2: Implementing Six Sigma Projects
With a solid foundation in place, InnovateTech embarked on a series of Six Sigma projects. Each project followed the DMAIC methodology rigorously:
Define:
This phase involved clearly defining the problem, setting project goals, and identifying stakeholders. Using tools like SIPOC (Suppliers, Inputs, Process, Outputs, Customers) diagrams, teams precisely mapped the process under scrutiny.
Measure:
This stage focused on collecting data to understand the current state of the process. InnovateTech utilized various data collection methods, including statistical process control (SPC) charts, surveys, and process mapping. This quantitative approach provided a factual basis for subsequent analysis.
Analyze:
Here, teams analyzed the data to identify root causes of defects and inefficiencies. Powerful statistical tools like Pareto charts, fishbone diagrams, and regression analysis were employed to pinpoint areas for improvement.
Improve:
This crucial phase involved developing and implementing solutions to address the root causes identified during the analysis phase. InnovateTech embraced creative problem-solving techniques, such as brainstorming and design of experiments (DOE), to develop and test potential solutions.
Control:
Finally, the improved process was standardized and monitored to ensure sustained improvements. Control charts and other monitoring tools helped track performance and identify any deviations from the target. This phase was vital in embedding the changes and preventing backsliding.
Phase 3: Expanding and Sustaining Six Sigma
The initial success of the projects fueled further adoption of Six Sigma across InnovateTech. The organization expanded its Black Belt and Green Belt programs, creating a network of internal experts. This approach fostered continuous improvement and knowledge sharing.
Scaling Six Sigma Across Departments:
InnovateTech systematically applied Six Sigma to various departments, including manufacturing, supply chain, customer service, and research and development. This broad implementation ensured that improvements weren't isolated to specific areas but had a systemic impact on the entire organization.
Embedding Six Sigma in the Organizational Culture:
Beyond specific projects, InnovateTech worked on embedding Six Sigma principles into its organizational culture. This involved promoting data-driven decision-making, encouraging continuous improvement, and fostering a culture of collaboration and learning. Regular meetings, workshops, and shared learning sessions reinforced the importance of Six Sigma.
Measuring and Reporting on Results:
InnovateTech established a robust system for tracking and reporting on the results of its Six Sigma initiatives. This involved regularly updating KPIs, documenting project successes, and communicating the benefits to all stakeholders. Transparency was crucial in maintaining momentum and securing continued support.
Continuous Improvement Initiatives:
Even after achieving significant improvements, InnovateTech understood that operational excellence is an ongoing process. The organization maintained its focus on continuous improvement, regularly identifying new opportunities for optimization and refinement. This commitment to continuous improvement ensured that the benefits of Six Sigma were sustained over time.
Challenges Faced and Lessons Learned
InnovateTech's journey wasn't without its challenges. Resistance to change, especially from employees unfamiliar with Six Sigma, was a significant hurdle. Overcoming this required strong leadership, clear communication, and demonstrating the benefits of the methodology through tangible results. Another challenge involved balancing the demands of ongoing operations with the time and resources required for Six Sigma projects. Careful project selection and efficient project management were crucial in mitigating this challenge.
Quantifiable Results and Impact
The successful implementation of Six Sigma at InnovateTech led to substantial improvements across various key performance indicators. Defect rates in manufacturing decreased by 70%, lead times were reduced by 40%, and customer satisfaction scores increased by 25%. These tangible results directly translated to improved profitability, increased market share, and enhanced brand reputation. Furthermore, the improved processes and enhanced efficiency led to significant cost savings, freeing up resources for investment in innovation and growth. The improved employee engagement and empowerment fostered a more positive and productive work environment.
Conclusion: Sustaining the Six Sigma Journey
InnovateTech's journey demonstrates the transformative power of a fully adopted Six Sigma methodology. The success wasn't solely due to the methodology itself but also to the commitment of leadership, the effective training and development of employees, and the focus on embedding Six Sigma into the organizational culture. The organization's success underscores the importance of continuous improvement and the value of a data-driven approach to problem-solving. Their story serves as a compelling case study for organizations seeking to achieve operational excellence and unlock their full potential. The continuous monitoring and adaptation of Six Sigma principles, along with regular reviews and adjustments, are key factors in long-term success. By integrating Six Sigma into every facet of the business, InnovateTech ensures that its drive for excellence remains a constant force, propelling future growth and innovation.
Latest Posts
Latest Posts
-
All Of The Following Are Popular Linux Distributions Except
Apr 12, 2025
-
Benefits Of Activity Based Costing Include
Apr 12, 2025
-
A Description That Predicts What Happens But Not How
Apr 12, 2025
-
Following Are Transactions For Vitalo Company
Apr 12, 2025
-
Who Is The Famous Football Coach Mentioned In This Segment
Apr 12, 2025
Related Post
Thank you for visiting our website which covers about An Organization That Fully Adopts The Six Sigma Methodology . We hope the information provided has been useful to you. Feel free to contact us if you have any questions or need further assistance. See you next time and don't miss to bookmark.