An Effective Process Management Program Requires
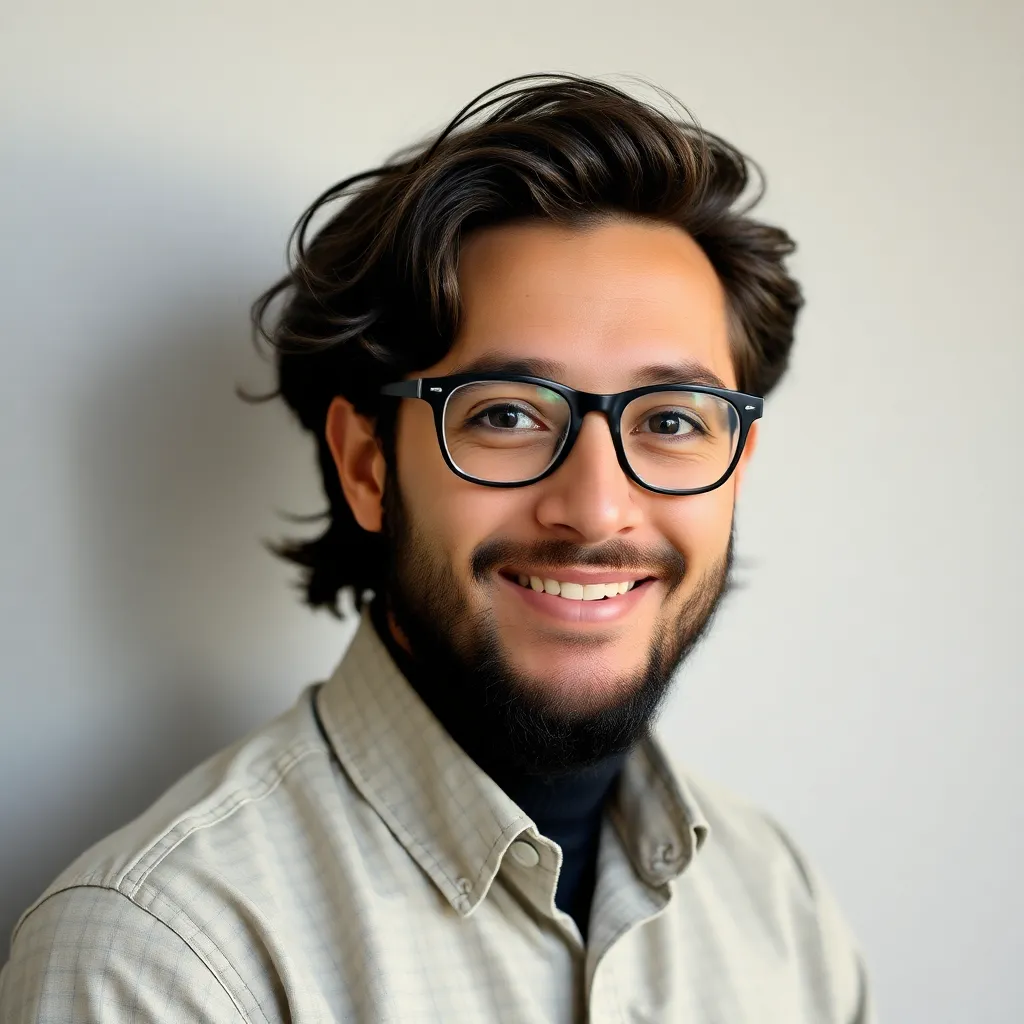
Holbox
Apr 13, 2025 · 6 min read

Table of Contents
- An Effective Process Management Program Requires
- Table of Contents
- An Effective Process Management Program Requires: A Comprehensive Guide
- 1. Clear Definition of Goals and Objectives
- Defining SMART Goals:
- 2. Comprehensive Process Mapping and Analysis
- Process Mapping Techniques:
- 3. Effective Communication and Collaboration
- Communication Strategies:
- 4. Robust Technology and Tools
- Technology Solutions:
- 5. Continuous Improvement and Monitoring
- Continuous Improvement Strategies:
- 6. Clear Roles and Responsibilities
- Defining Roles:
- 7. Change Management Strategy
- Change Management Best Practices:
- 8. Metrics and Measurement
- Key Performance Indicators (KPIs):
- 9. Documentation and Knowledge Management
- Documentation Best Practices:
- 10. Leadership Support and Commitment
- Leadership Roles:
- Latest Posts
- Latest Posts
- Related Post
An Effective Process Management Program Requires: A Comprehensive Guide
Implementing a successful process management program is crucial for organizational efficiency, productivity, and growth. It's not a one-size-fits-all solution; the specific requirements vary depending on the organization's size, industry, and goals. However, several key elements consistently contribute to the effectiveness of any process management initiative. This comprehensive guide delves into these essential components, providing insights and best practices to help you build a robust and impactful program.
1. Clear Definition of Goals and Objectives
Before embarking on any process improvement journey, a crystal-clear understanding of the desired outcomes is paramount. This isn't simply about identifying areas for improvement; it's about setting specific, measurable, achievable, relevant, and time-bound (SMART) goals.
Defining SMART Goals:
- Specific: Instead of "Improve customer service," aim for "Reduce customer service call resolution time by 15% within the next quarter."
- Measurable: Establish quantifiable metrics to track progress. This might involve key performance indicators (KPIs) like cycle time, defect rates, or customer satisfaction scores.
- Achievable: Goals should be challenging yet realistic, considering available resources and organizational capabilities.
- Relevant: Goals must align with the overall strategic objectives of the organization. They should directly contribute to the company's mission and vision.
- Time-bound: Set deadlines to create a sense of urgency and ensure accountability.
Without well-defined goals, your process management program will lack direction, making it difficult to measure success and demonstrate ROI.
2. Comprehensive Process Mapping and Analysis
Once the goals are established, a thorough process mapping exercise is essential. This involves visually representing the steps involved in each key process. Several techniques can be employed, including:
Process Mapping Techniques:
- Flowcharts: These diagrams use standard symbols to illustrate the sequence of steps, decision points, and potential bottlenecks.
- Swimlane diagrams: These extend flowcharts by adding "swimlanes" to represent different departments or roles involved in the process. This helps identify handoffs and potential areas of communication breakdown.
- Value stream mapping: This technique focuses on identifying and eliminating waste in a process, highlighting value-added activities versus non-value-added ones.
Thorough analysis of the mapped processes is crucial. This involves identifying:
- Bottlenecks: Points in the process where work slows down or gets stuck.
- Redundancies: Steps or activities that add no value and can be eliminated.
- Errors: Areas prone to mistakes or defects.
- Inefficiencies: Areas where resources are wasted or processes could be streamlined.
This analysis forms the basis for identifying improvement opportunities.
3. Effective Communication and Collaboration
Successful process management requires strong communication and collaboration across all levels of the organization. This involves:
Communication Strategies:
- Transparency: Keep all stakeholders informed about the process improvement initiative, its goals, and progress.
- Open Feedback: Encourage feedback and input from employees involved in the processes being improved.
- Regular Updates: Provide regular updates on the progress of the initiative and address any concerns or challenges.
- Training and Education: Provide employees with the necessary training and resources to understand and implement the improved processes.
Collaboration is particularly crucial when processes span multiple departments or teams. Establishing cross-functional teams can ensure buy-in and facilitate efficient implementation of changes.
4. Robust Technology and Tools
Technology plays a vital role in supporting a process management program. This may involve:
Technology Solutions:
- Business Process Management (BPM) software: These platforms offer tools for process modeling, automation, monitoring, and analysis.
- Document Management Systems (DMS): These systems help streamline document workflows and reduce the risk of errors.
- Data Analytics Tools: These tools provide insights into process performance, allowing for data-driven decision-making.
- Collaboration Platforms: Platforms like Slack or Microsoft Teams facilitate communication and collaboration among team members.
The choice of technology should align with the organization's specific needs and budget. It's crucial to choose user-friendly tools that integrate seamlessly with existing systems.
5. Continuous Improvement and Monitoring
An effective process management program isn't a one-time project; it's an ongoing journey of continuous improvement. This requires:
Continuous Improvement Strategies:
- Regular Monitoring: Establish key performance indicators (KPIs) to track the effectiveness of improved processes.
- Data Analysis: Analyze data regularly to identify areas for further improvement.
- Feedback Loops: Establish mechanisms for gathering feedback from employees and customers to identify areas needing attention.
- Process Audits: Conduct regular process audits to ensure processes are being followed and identify any deviations.
- Adaptability: Be prepared to adapt processes as needed to respond to changing business needs or market conditions.
By embracing a culture of continuous improvement, organizations can ensure that their processes remain efficient, effective, and aligned with their strategic goals.
6. Clear Roles and Responsibilities
A successful process management program requires clear roles and responsibilities for all stakeholders. This includes:
Defining Roles:
- Process Owner: Responsible for the overall performance and management of a specific process.
- Process Manager: Responsible for the day-to-day execution and improvement of a process.
- Process Analyst: Responsible for analyzing processes, identifying improvement opportunities, and developing solutions.
- Process Improvement Team: A cross-functional team responsible for implementing process improvements.
Clearly defined roles and responsibilities help avoid confusion and ensure accountability. Everyone should understand their contribution to the overall success of the program.
7. Change Management Strategy
Implementing process improvements inevitably involves change, and effective change management is critical for success. This includes:
Change Management Best Practices:
- Communication: Clearly communicate the reasons for the changes, the benefits they will bring, and how they will affect employees.
- Training: Provide employees with the necessary training and support to adapt to the new processes.
- Involvement: Involve employees in the process improvement process to build buy-in and ownership.
- Incentives: Recognize and reward employees who contribute to successful process improvements.
- Addressing Resistance: Anticipate and address potential resistance to change proactively.
A well-defined change management strategy helps minimize disruption and maximize employee acceptance of new processes.
8. Metrics and Measurement
The success of a process management program hinges on the ability to measure its impact. This requires:
Key Performance Indicators (KPIs):
- Cycle Time: The time it takes to complete a process.
- Defect Rate: The percentage of processes that result in errors.
- Throughput: The rate at which processes are completed.
- Customer Satisfaction: Measures of customer happiness with the process outcomes.
- Cost Reduction: Savings realized through process improvements.
Regularly monitoring these KPIs provides valuable insights into process performance and allows for timely adjustments. Data-driven decision making is paramount for continuous improvement.
9. Documentation and Knowledge Management
Comprehensive documentation is essential for maintaining process consistency and enabling knowledge transfer. This includes:
Documentation Best Practices:
- Process Maps: Detailed visual representations of processes.
- Standard Operating Procedures (SOPs): Step-by-step instructions for executing processes.
- Training Materials: Materials to help employees understand and implement processes.
- Knowledge Base: A centralized repository of information related to processes.
Well-maintained documentation ensures that processes are consistently executed and that knowledge is readily accessible to all stakeholders. This is crucial for maintaining efficiency and minimizing errors, even with staff turnover.
10. Leadership Support and Commitment
Ultimately, the success of a process management program depends on strong leadership support and commitment. Leaders must:
Leadership Roles:
- Champion the initiative: Communicate the importance of process improvement and provide the necessary resources.
- Set the tone: Foster a culture of continuous improvement and encourage innovation.
- Provide support: Provide the necessary support and guidance to process improvement teams.
- Recognize accomplishments: Recognize and reward teams and individuals who contribute to process improvements.
Leadership's commitment sets the stage for a successful process management program. Without it, initiatives are likely to encounter resistance and ultimately fail to deliver the desired results.
By incorporating these ten key elements into your process management program, you significantly increase your chances of achieving significant improvements in efficiency, productivity, and overall organizational performance. Remember that process management is an iterative process; continuous monitoring, evaluation, and adaptation are crucial for long-term success.
Latest Posts
Latest Posts
-
The Diagram Depicts The Cost Curves And The Marginal Revenue
Apr 16, 2025
-
At The Instant Shown Cars A And B
Apr 16, 2025
-
All Natural Resources Human Resources And Manufactured Goods
Apr 16, 2025
-
At January 1 2024 Cafe Med Leased Restaurant Equipment
Apr 16, 2025
-
Where Should Students Dispose Of Solid Anhydrous Sulfate
Apr 16, 2025
Related Post
Thank you for visiting our website which covers about An Effective Process Management Program Requires . We hope the information provided has been useful to you. Feel free to contact us if you have any questions or need further assistance. See you next time and don't miss to bookmark.