All Of The Following Are Ways To Improve Quality Except
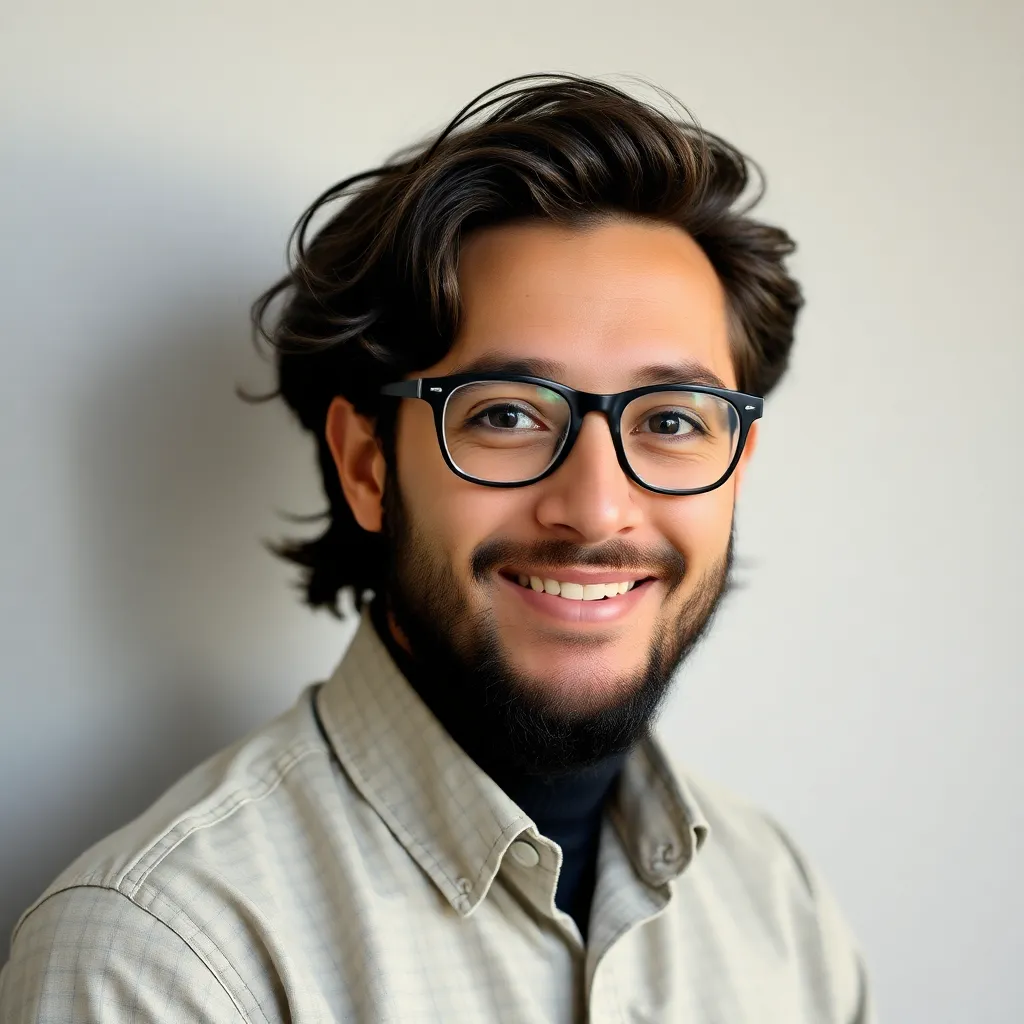
Holbox
May 11, 2025 · 5 min read
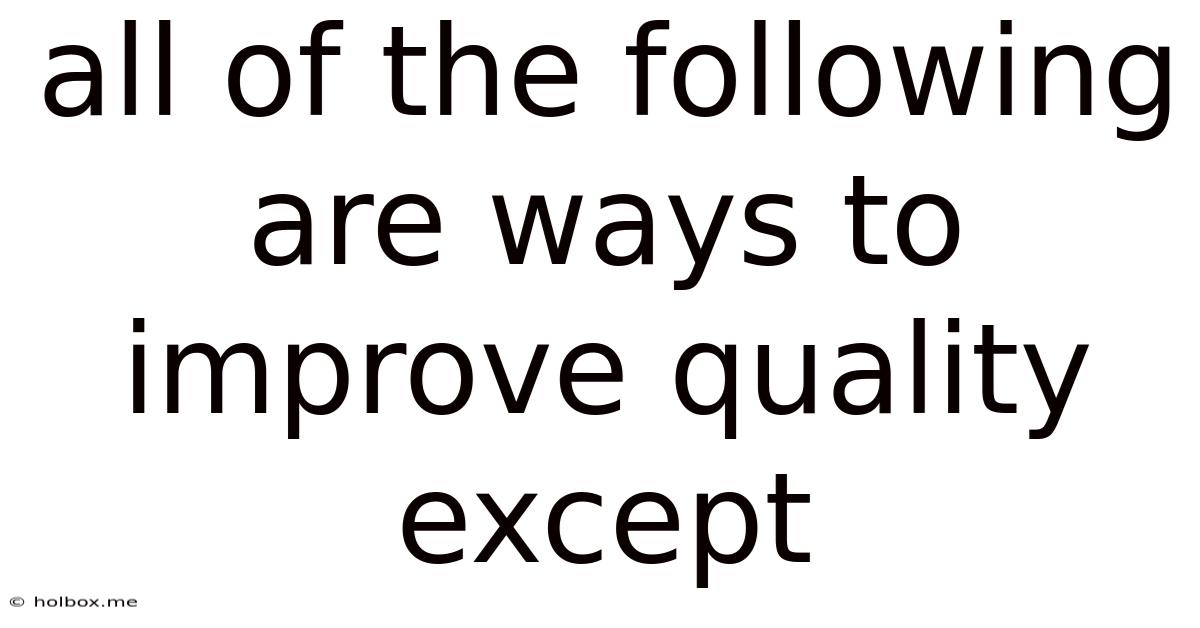
Table of Contents
- All Of The Following Are Ways To Improve Quality Except
- Table of Contents
- All of the Following Are Ways to Improve Quality Except… Understanding the Exceptions in Quality Enhancement
- Common Methods for Improving Quality
- 1. Implementing Robust Quality Management Systems (QMS)
- 2. Investing in Employee Training and Development
- 3. Utilizing Advanced Technologies and Automation
- 4. Fostering a Culture of Quality
- 5. Implementing Robust Quality Control Measures
- The Exception: Ignoring Customer Feedback
- Latest Posts
- Latest Posts
- Related Post
All of the Following Are Ways to Improve Quality Except… Understanding the Exceptions in Quality Enhancement
Quality improvement is a continuous journey, a relentless pursuit of excellence in any field, be it manufacturing, service provision, or even personal development. Numerous strategies and techniques exist to elevate quality, but understanding what doesn't improve quality is equally crucial. This article delves into various methods for enhancing quality, highlighting the exception that stands in stark contrast to the others. We'll explore the nuances of quality improvement and identify the common pitfalls that hinder progress.
Common Methods for Improving Quality
Before pinpointing the exception, let's establish a firm understanding of the proven methods for enhancing quality. These strategies are widely adopted across diverse industries and disciplines.
1. Implementing Robust Quality Management Systems (QMS)
A well-defined QMS provides a structured framework for managing and improving quality. This often involves adhering to internationally recognized standards like ISO 9001. A strong QMS emphasizes:
- Process Mapping & Analysis: Understanding and documenting processes helps identify bottlenecks and areas for improvement. Tools like flowcharts and value stream mapping are invaluable here.
- Data-Driven Decision Making: Collecting and analyzing data on key quality metrics allows for informed decision-making and targeted interventions.
- Continuous Improvement (Kaizen): Embracing a culture of continuous improvement means consistently seeking opportunities for refinement and optimization. This often involves implementing small, incremental changes over time.
- Regular Audits & Reviews: Periodic audits ensure adherence to standards and highlight areas needing attention. Regular reviews help assess the effectiveness of implemented improvements.
2. Investing in Employee Training and Development
A skilled and knowledgeable workforce is the backbone of any high-quality operation. Investing in employee training and development results in:
- Enhanced Skills & Expertise: Training equips employees with the necessary skills and knowledge to perform their tasks effectively.
- Improved Efficiency & Productivity: Well-trained employees are more efficient and productive, reducing errors and waste.
- Increased Job Satisfaction & Morale: Investment in employee development demonstrates a commitment to their growth, boosting morale and job satisfaction.
- Reduced Errors & Defects: Proper training minimizes errors and defects, resulting in higher quality outputs.
3. Utilizing Advanced Technologies and Automation
Technology plays a crucial role in quality enhancement. Advanced technologies such as:
- Automated Inspection Systems: Automated systems can perform inspections with greater speed and accuracy than manual methods.
- Data Analytics & Predictive Modeling: Analyzing data can identify trends and predict potential quality issues before they arise.
- Robotics & Automation: Automation can reduce human error and improve consistency in manufacturing and other processes.
- Simulation & Modeling: Simulating processes helps identify potential problems and optimize designs before implementation.
4. Fostering a Culture of Quality
A culture of quality permeates every aspect of an organization, emphasizing a shared commitment to excellence. This involves:
- Clear Quality Goals & Objectives: Defining clear goals provides direction and focus for quality improvement efforts.
- Open Communication & Feedback: Encouraging open communication and feedback from all levels ensures that issues are identified and addressed promptly.
- Customer Focus: Prioritizing customer needs and satisfaction is essential for delivering high-quality products or services.
- Empowerment & Accountability: Empowering employees to take ownership of quality and holding them accountable for their actions fosters a culture of responsibility.
5. Implementing Robust Quality Control Measures
Rigorous quality control measures are essential to ensure that products or services meet specified standards. This involves:
- Incoming Material Inspection: Inspecting incoming materials ensures that they meet the required quality specifications.
- In-Process Inspection: Monitoring processes during production helps identify and correct problems early on.
- Final Product Inspection: Inspecting the final product ensures that it meets all quality standards before delivery.
- Statistical Process Control (SPC): SPC uses statistical methods to monitor and control processes, reducing variation and improving quality.
The Exception: Ignoring Customer Feedback
While all the aforementioned strategies are vital for improving quality, there's one glaring exception: ignoring customer feedback. This stands in stark contrast to all other methods because it actively undermines the very foundation of quality improvement.
Customer feedback is the ultimate measure of quality. It provides invaluable insights into customer satisfaction, product performance, and areas for improvement. Ignoring this crucial information is akin to navigating without a map—you might reach your destination eventually, but it will be far less efficient and likely result in numerous setbacks.
Ignoring customer feedback leads to:
- Missed Opportunities for Improvement: Valuable insights into product flaws, unmet needs, and areas for innovation are lost.
- Decreased Customer Satisfaction: Customers feel unheard and undervalued, leading to lower satisfaction and loyalty.
- Increased Customer Churn: Dissatisfied customers are more likely to switch to competitors.
- Damaged Brand Reputation: Negative word-of-mouth and online reviews can severely damage a brand's reputation.
- Stagnant Product Development: Without understanding customer needs, product development stagnates, hindering innovation and competitiveness.
Why is ignoring customer feedback so detrimental? Because quality is ultimately defined by the customer. While internal metrics and processes are important, they don't provide the complete picture. Only by actively seeking and acting upon customer feedback can an organization truly understand and meet customer expectations.
To avoid this critical mistake, organizations must establish robust mechanisms for collecting and analyzing customer feedback. This includes:
- Surveys & Questionnaires: Gathering feedback through structured surveys and questionnaires allows for systematic data collection.
- Customer Reviews & Testimonials: Monitoring online reviews and testimonials provides valuable insights into customer experiences.
- Focus Groups & Interviews: In-depth interviews and focus groups provide richer, qualitative data.
- Social Media Monitoring: Tracking social media mentions and conversations can identify emerging issues and trends.
- Customer Service Interactions: Analyzing customer service interactions can highlight common problems and areas for improvement.
Acting upon Customer Feedback:
Collecting feedback is only half the battle. Organizations must also take concrete steps to act upon the feedback they receive. This involves:
- Prioritizing Feedback: Not all feedback is created equal. Prioritize feedback based on its impact and frequency.
- Implementing Changes: Make tangible changes based on the feedback received.
- Measuring the Impact of Changes: Track the impact of implemented changes to ensure they are effective.
- Communicating with Customers: Keep customers informed about the actions taken in response to their feedback.
- Continuous Monitoring & Improvement: Continuously monitor customer feedback and make ongoing improvements.
In conclusion, while implementing robust QMS, investing in employee training, leveraging technology, fostering a culture of quality, and establishing rigorous quality control measures are all crucial for improving quality, ignoring customer feedback is the exception that undermines all other efforts. Actively seeking, analyzing, and acting upon customer feedback is paramount to achieving true quality excellence and building lasting customer relationships. Only through a customer-centric approach can organizations truly understand and meet the expectations that define quality in the eyes of those who matter most – their customers.
Latest Posts
Latest Posts
-
How Tall Is 130 Cm In Feet
May 21, 2025
-
How Much Is 83 Kg In Stones
May 21, 2025
-
183 Cm To Inches And Feet
May 21, 2025
-
22 Lbs Is How Many Kg
May 21, 2025
-
122 Cm To Feet And Inches
May 21, 2025
Related Post
Thank you for visiting our website which covers about All Of The Following Are Ways To Improve Quality Except . We hope the information provided has been useful to you. Feel free to contact us if you have any questions or need further assistance. See you next time and don't miss to bookmark.