Advance Study Assignment Analysis Of An Aluminum Zinc Alloy
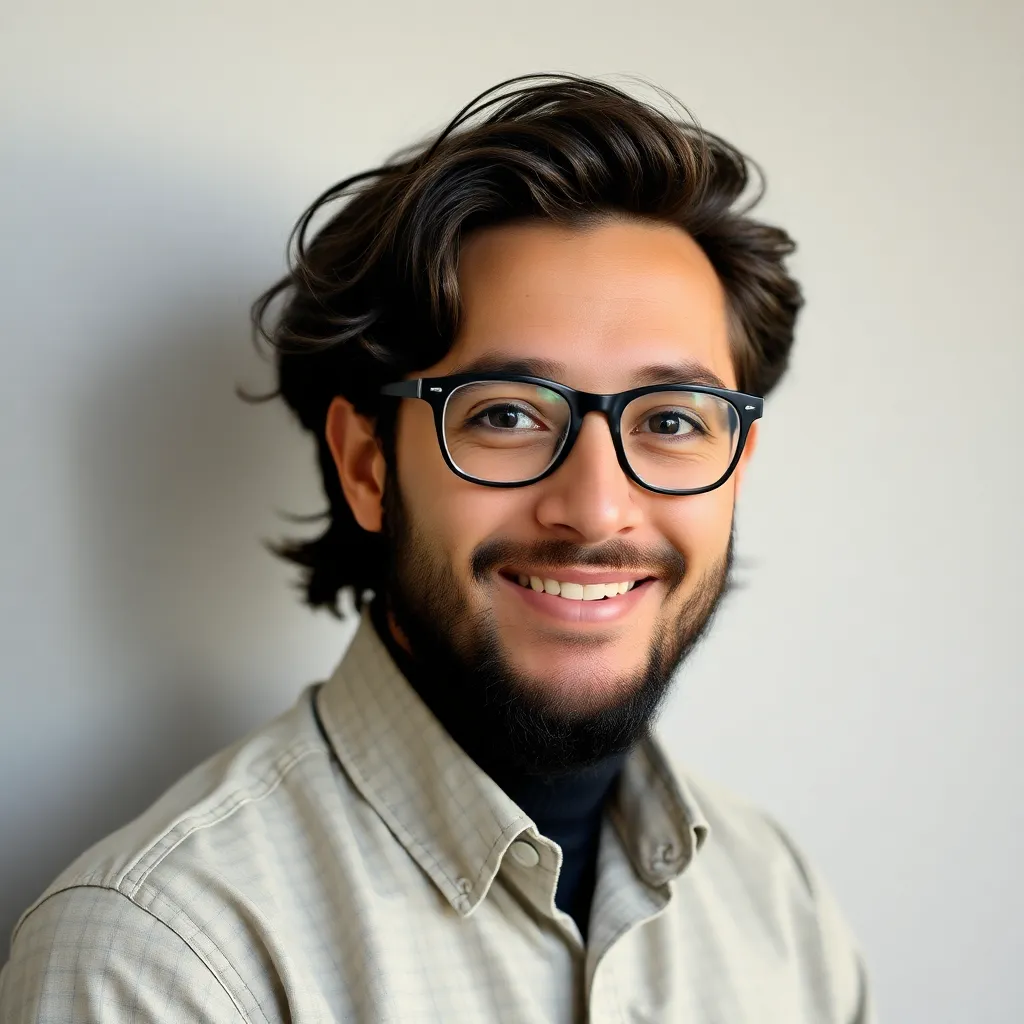
Holbox
Apr 04, 2025 · 6 min read

Table of Contents
- Advance Study Assignment Analysis Of An Aluminum Zinc Alloy
- Table of Contents
- Advanced Study Assignment Analysis of an Aluminum Zinc Alloy
- Understanding Aluminum Zinc Alloys
- Key Properties Influenced by Zinc Addition:
- Microstructural Analysis Techniques
- 1. Optical Microscopy:
- 2. Scanning Electron Microscopy (SEM):
- 3. Transmission Electron Microscopy (TEM):
- Mechanical Property Testing
- 1. Tensile Testing:
- 2. Hardness Testing:
- 3. Fatigue Testing:
- 4. Creep Testing:
- Influence of Processing Techniques
- 1. Casting:
- 2. Rolling:
- 3. Heat Treatment:
- 4. Welding:
- Applications of Aluminum Zinc Alloys
- Conclusion
- Latest Posts
- Latest Posts
- Related Post
Advanced Study Assignment Analysis of an Aluminum Zinc Alloy
This advanced study assignment delves into the comprehensive analysis of an aluminum zinc (Al-Zn) alloy, focusing on its microstructure, mechanical properties, and potential applications. We'll explore various analytical techniques used to characterize this material, examining its strengths, limitations, and the underlying principles governing its behavior.
Understanding Aluminum Zinc Alloys
Aluminum zinc alloys represent a significant class of materials within the broader family of aluminum alloys. These alloys are known for their unique combination of properties, primarily stemming from the addition of zinc to the aluminum matrix. Zinc, as an alloying element, significantly influences the microstructure and consequently, the mechanical properties of the resulting alloy. The specific properties of an Al-Zn alloy are highly dependent on the zinc concentration, the presence of other alloying elements (e.g., magnesium, copper), and the processing techniques employed during its manufacturing.
Key Properties Influenced by Zinc Addition:
-
Strength: Zinc additions substantially enhance the strength and hardness of the aluminum alloy, surpassing that of pure aluminum considerably. This strengthening effect arises from solid solution strengthening and, in some cases, precipitation hardening.
-
Ductility: While zinc enhances strength, it often reduces the ductility (ability to deform plastically) of the alloy. The optimal balance between strength and ductility is a crucial consideration in alloy design and selection.
-
Corrosion Resistance: Aluminum possesses inherent corrosion resistance due to the formation of a protective oxide layer. The addition of zinc can either enhance or diminish this resistance, depending on the alloy's composition and the environment.
-
Weldability: The weldability of Al-Zn alloys can vary depending on the specific composition. Higher zinc content might increase the susceptibility to hot cracking during welding.
-
Machinability: Generally, Al-Zn alloys exhibit good machinability, making them suitable for various manufacturing processes.
Microstructural Analysis Techniques
Understanding the microstructure of an Al-Zn alloy is crucial for correlating its properties with its internal structure. Several techniques are used to achieve this:
1. Optical Microscopy:
Optical microscopy provides a relatively simple and cost-effective method for examining the alloy's microstructure at lower magnifications. Sample preparation involves polishing and etching the surface to reveal the grain boundaries and different phases present. This technique allows for the observation of grain size, shape, and the distribution of different phases, giving a general overview of the microstructure. However, its resolution is limited, and finer details may be missed.
2. Scanning Electron Microscopy (SEM):
SEM offers higher resolution compared to optical microscopy. It allows for detailed visualization of the microstructure, including the observation of individual precipitates and their morphology. By employing techniques like energy-dispersive X-ray spectroscopy (EDS), the chemical composition of different phases can be determined. SEM is invaluable for studying the distribution of alloying elements and identifying secondary phases.
3. Transmission Electron Microscopy (TEM):
TEM provides the highest resolution among the microscopy techniques. It allows for the observation of individual dislocations, precipitates, and other microstructural features at the atomic level. This technique is particularly useful for studying the mechanisms of strengthening and understanding the role of specific precipitates in enhancing mechanical properties. However, TEM sample preparation is more complex and time-consuming.
Mechanical Property Testing
The mechanical properties of the Al-Zn alloy are critical for determining its suitability for various engineering applications. Commonly used tests include:
1. Tensile Testing:
Tensile testing provides essential information about the alloy's strength, ductility, and elastic modulus. A standardized tensile specimen is subjected to a uniaxial tensile load, and the stress-strain curve is obtained. From this curve, important parameters like yield strength, ultimate tensile strength, elongation, and reduction in area can be determined. These parameters directly relate to the alloy's ability to withstand stress and deformation.
2. Hardness Testing:
Hardness testing is a simpler and faster method for assessing the alloy's resistance to indentation. Common techniques include Brinell, Rockwell, and Vickers hardness tests. Hardness is a good indicator of strength, and it correlates well with tensile strength. Hardness testing is especially useful for quality control during manufacturing and for evaluating the effect of heat treatments.
3. Fatigue Testing:
Fatigue testing evaluates the alloy's resistance to failure under cyclic loading. A specimen is subjected to repeated cycles of stress, and the number of cycles to failure is determined. This test is important for determining the alloy's suitability for applications involving dynamic loading, such as automotive components or aircraft parts.
4. Creep Testing:
Creep testing investigates the alloy's behavior under sustained high-temperature loading. A specimen is subjected to a constant load at an elevated temperature, and the strain over time is measured. This test is crucial for applications where the alloy will be subjected to high temperatures and stresses, such as in aerospace or power generation industries.
Influence of Processing Techniques
The processing techniques employed during the manufacturing of Al-Zn alloys have a significant impact on their final microstructure and properties.
1. Casting:
Casting is a commonly used method for producing Al-Zn alloys in various shapes. The casting process influences the grain size and segregation of alloying elements, which can affect the mechanical properties.
2. Rolling:
Rolling is a plastic deformation process used to reduce the thickness of the alloy and improve its mechanical properties. Rolling affects the grain structure, leading to a preferred orientation, which can enhance strength in specific directions.
3. Heat Treatment:
Heat treatment plays a critical role in controlling the microstructure and mechanical properties of Al-Zn alloys. Solution treatment and aging are commonly used to achieve precipitation hardening, resulting in significantly increased strength. The parameters of the heat treatment, such as temperature and time, need to be carefully controlled to optimize the mechanical properties.
4. Welding:
Welding techniques need to be carefully selected for Al-Zn alloys to avoid issues such as porosity or hot cracking. The specific welding process and parameters depend on the alloy composition and the thickness of the material.
Applications of Aluminum Zinc Alloys
The unique combination of properties makes Al-Zn alloys suitable for a wide range of applications:
-
Aerospace Industry: Al-Zn alloys find use in aircraft structures due to their high strength-to-weight ratio.
-
Automotive Industry: Their good machinability and strength make them suitable for various automotive components.
-
Electronics: Al-Zn alloys can be employed in electronic packaging due to their good electrical conductivity.
-
Transportation: Their strength and corrosion resistance make them suitable for railway cars and other transportation equipment.
-
Construction: These alloys can be utilized in building construction where high strength and lightweight are essential.
Conclusion
This advanced study assignment provides a comprehensive overview of Al-Zn alloys, covering their microstructural analysis, mechanical property testing, processing techniques, and applications. The interplay between composition, processing, and microstructure determines the ultimate properties of these alloys. Understanding these relationships is crucial for selecting the appropriate Al-Zn alloy for a given application and optimizing its performance. Further research into specific Al-Zn alloy compositions and their tailored applications would provide more specific and detailed information on this important class of materials. Continued advancements in processing techniques and alloy design will likely lead to the development of even stronger and more versatile Al-Zn alloys in the future. This analysis serves as a foundational understanding of the subject, encouraging further exploration and specialized research within this fascinating area of materials science.
Latest Posts
Latest Posts
-
All Three Joints In The Figure Are Classified As
Apr 15, 2025
-
Disney Has Different Divisions For Movies
Apr 15, 2025
-
Based On The Data Which Foreign Holder Of Us Debt
Apr 15, 2025
-
Q Purchases A 500 000 Life
Apr 15, 2025
-
Which Of The Following Is A Passive Process
Apr 15, 2025
Related Post
Thank you for visiting our website which covers about Advance Study Assignment Analysis Of An Aluminum Zinc Alloy . We hope the information provided has been useful to you. Feel free to contact us if you have any questions or need further assistance. See you next time and don't miss to bookmark.