A Successful Quality Strategy Features Which Of The Following Elements
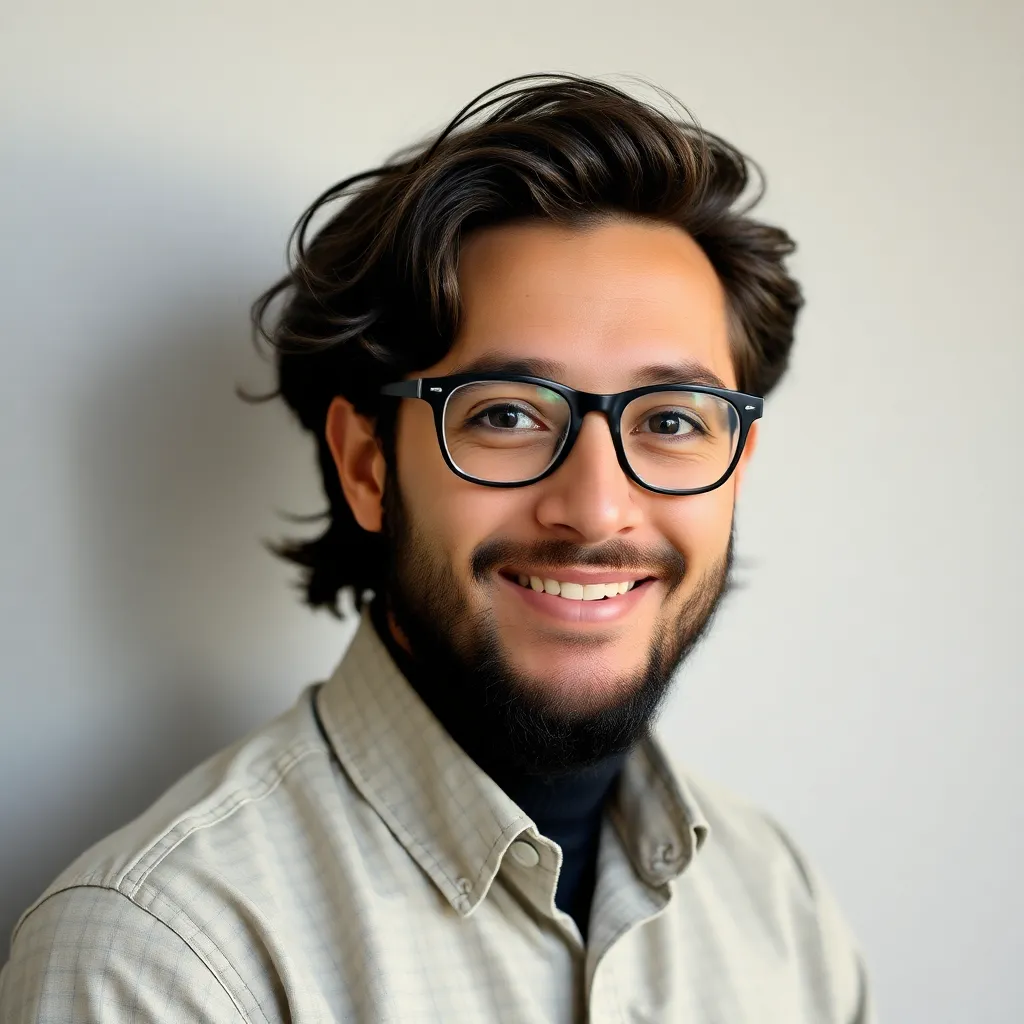
Holbox
May 10, 2025 · 7 min read
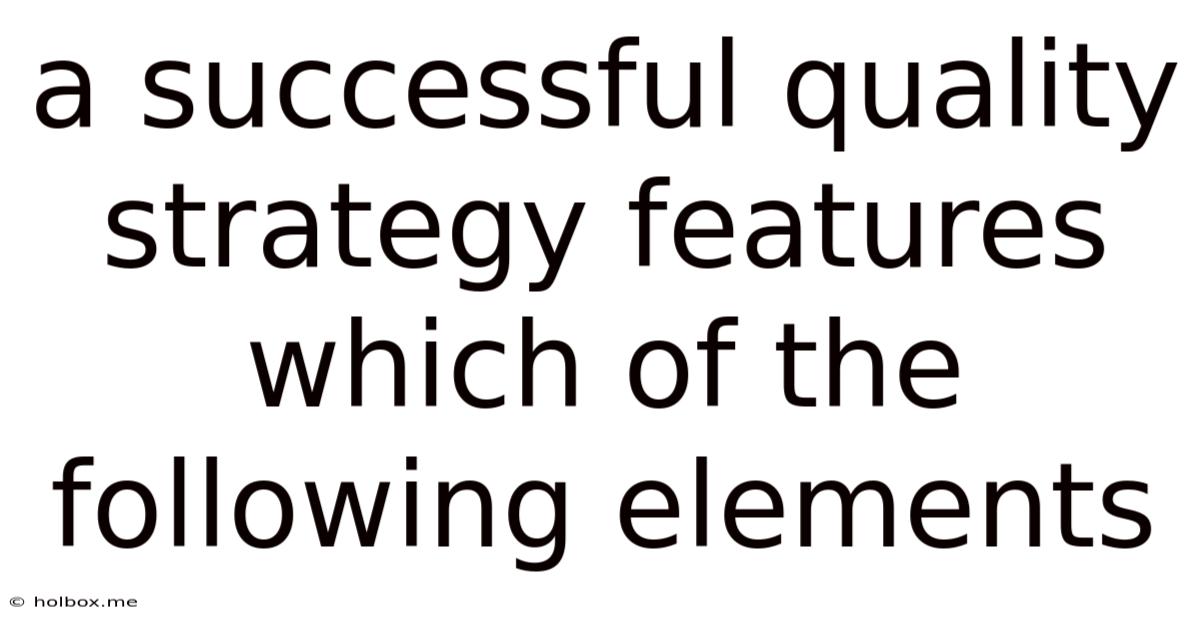
Table of Contents
- A Successful Quality Strategy Features Which Of The Following Elements
- Table of Contents
- A Successful Quality Strategy: Key Elements for Excellence
- 1. Strong Leadership Commitment and Vision
- 1.1 Setting Clear Quality Goals and Objectives:
- 1.2 Resource Allocation:
- 1.3 Fostering a Culture of Quality:
- 2. Customer Focus: Understanding and Meeting Needs
- 2.1 Voice of the Customer (VoC) Programs:
- 2.2 Proactive Customer Engagement:
- 2.3 Meeting and Exceeding Expectations:
- 3. Process Improvement and Optimization: Lean and Six Sigma
- 3.1 Lean Principles:
- 3.2 Six Sigma Methodology:
- 3.3 Continuous Improvement (Kaizen):
- 4. Robust Quality Management System (QMS):
- 4.1 Documented Processes:
- 4.2 Regular Audits and Reviews:
- 4.3 Corrective and Preventive Actions (CAPA):
- 5. Employee Empowerment and Training:
- 5.1 Empowerment and Ownership:
- 5.2 Comprehensive Training Programs:
- 5.3 Recognition and Rewards:
- 6. Data-Driven Decision Making: Metrics and Analysis
- 6.1 Key Performance Indicators (KPIs):
- 6.2 Data Analysis and Reporting:
- 6.3 Use of Statistical Tools:
- 7. Continuous Improvement and Adaptation:
- 7.1 Regular Review and Updates:
- 7.2 Benchmarking and Best Practices:
- 7.3 Embracing Technological Advancements:
- 8. Supplier Management: Ensuring Consistent Quality
- 8.1 Supplier Selection and Evaluation:
- 8.2 Supplier Relationship Management:
- 8.3 Supplier Audits and Inspections:
- Conclusion: Building a Culture of Quality
- Latest Posts
- Related Post
A Successful Quality Strategy: Key Elements for Excellence
A robust quality strategy isn't just about producing defect-free products or services; it's about fostering a culture of continuous improvement, exceeding customer expectations, and driving sustainable growth. This comprehensive approach requires a strategic blend of elements working in harmony. Let's delve into the critical features that define a truly successful quality strategy.
1. Strong Leadership Commitment and Vision
At the heart of any successful quality initiative lies unwavering leadership commitment. This isn't simply lip service; it requires active participation from top management, demonstrating their dedication through:
1.1 Setting Clear Quality Goals and Objectives:
A successful quality strategy begins with clearly defined, measurable, achievable, relevant, and time-bound (SMART) goals. These goals shouldn't be generic statements but specific targets related to defect rates, customer satisfaction, process efficiency, and other key performance indicators (KPIs). Leadership must champion these goals, ensuring they are integrated into the overall business strategy.
1.2 Resource Allocation:
Quality improvement isn't free. Leadership must allocate sufficient resources – financial, human, and technological – to support quality initiatives. This includes investing in training programs, advanced equipment, and quality management systems (QMS). Lack of resource commitment is a major impediment to successful quality implementation.
1.3 Fostering a Culture of Quality:
Leadership plays a pivotal role in cultivating a culture where quality is valued above all else. This involves leading by example, communicating the importance of quality consistently, and recognizing and rewarding employees for their contributions to quality improvement. A culture of quality permeates all levels of the organization, from the shop floor to the executive suite.
2. Customer Focus: Understanding and Meeting Needs
A truly successful quality strategy places the customer at its core. Understanding and exceeding customer expectations is paramount. This involves:
2.1 Voice of the Customer (VoC) Programs:
Effective VoC programs gather feedback from customers through surveys, interviews, focus groups, and social media monitoring. This feedback provides invaluable insights into customer needs, preferences, and pain points. Analyzing this data helps organizations identify areas for improvement and tailor products and services accordingly.
2.2 Proactive Customer Engagement:
Beyond simply gathering feedback, successful strategies involve proactively engaging with customers to build strong relationships. This might involve personalized communication, offering support and assistance, and actively seeking out customer input on new product development. Building trust and loyalty is a key outcome of customer-centric quality.
2.3 Meeting and Exceeding Expectations:
Understanding customer needs is just the first step. A successful strategy translates this understanding into tangible actions that exceed customer expectations. This might involve delivering products or services that are not only functional but also aesthetically pleasing, user-friendly, and reliable. Going the extra mile to delight customers builds brand loyalty and competitive advantage.
3. Process Improvement and Optimization: Lean and Six Sigma
Efficient and effective processes are the backbone of high quality. Successful quality strategies incorporate methodologies like Lean and Six Sigma to optimize processes, eliminate waste, and reduce variability.
3.1 Lean Principles:
Lean principles focus on eliminating waste (muda) in all forms – excess inventory, unnecessary movement, defects, waiting time, overproduction, over-processing, and unused talent. Implementing Lean techniques like value stream mapping, 5S, and Kanban helps streamline processes, reduce lead times, and improve efficiency.
3.2 Six Sigma Methodology:
Six Sigma utilizes statistical methods to identify and reduce variation in processes, aiming for near-zero defects. This involves using tools like DMAIC (Define, Measure, Analyze, Improve, Control) to systematically improve processes and achieve significant quality improvements.
3.3 Continuous Improvement (Kaizen):
Continuous improvement is a cornerstone of successful quality strategies. It involves a culture of ongoing learning and adaptation, where employees at all levels are encouraged to identify and implement improvements to processes. Kaizen emphasizes small, incremental changes that accumulate over time to produce significant results.
4. Robust Quality Management System (QMS):
A well-defined QMS provides the framework for managing quality across the organization. This includes:
4.1 Documented Processes:
Clearly documented processes ensure consistency and repeatability. These documents define how tasks are performed, the responsibilities of each individual, and the standards to be met. Standardization reduces errors and promotes efficiency.
4.2 Regular Audits and Reviews:
Regular internal and external audits assess the effectiveness of the QMS and identify areas for improvement. Management reviews provide an opportunity to evaluate performance against established goals and make necessary adjustments to the strategy.
4.3 Corrective and Preventive Actions (CAPA):
A robust CAPA system addresses quality issues promptly and effectively. This involves identifying root causes of problems, implementing corrective actions to prevent recurrence, and documenting all steps taken. A proactive CAPA system prevents future problems and improves overall quality.
5. Employee Empowerment and Training:
A successful quality strategy relies heavily on the skills and commitment of its employees. This requires:
5.1 Empowerment and Ownership:
Empowering employees to take ownership of quality involves giving them the authority and resources to identify and resolve quality issues. This encourages proactive problem-solving and fosters a culture of accountability.
5.2 Comprehensive Training Programs:
Providing employees with the necessary training and skills is crucial for successful quality implementation. This might involve training in quality management principles, statistical process control, problem-solving techniques, and specific software applications. Continuous learning ensures employees remain up-to-date with best practices.
5.3 Recognition and Rewards:
Recognizing and rewarding employees for their contributions to quality improvement reinforces the importance of quality and motivates employees to continue striving for excellence. This might involve offering bonuses, promotions, or public acknowledgment of achievements.
6. Data-Driven Decision Making: Metrics and Analysis
A successful quality strategy relies on data to monitor progress, identify areas for improvement, and make informed decisions. This involves:
6.1 Key Performance Indicators (KPIs):
Establishing relevant KPIs provides a clear picture of quality performance. KPIs might include defect rates, customer satisfaction scores, process cycle times, and cost of poor quality. Regular monitoring of KPIs helps track progress and identify potential problems.
6.2 Data Analysis and Reporting:
Analyzing data from various sources, including customer feedback, process data, and inspection results, provides insights into the effectiveness of quality initiatives. Regular reporting helps communicate progress and identify areas requiring attention.
6.3 Use of Statistical Tools:
Utilizing statistical tools like control charts, histograms, and scatter plots helps analyze data, identify trends, and make data-driven decisions. These tools provide a more objective and scientific approach to quality improvement.
7. Continuous Improvement and Adaptation:
The quality landscape is constantly evolving. A successful quality strategy embraces continuous improvement and adaptation.
7.1 Regular Review and Updates:
Regular review of the quality strategy is essential to ensure it remains aligned with business objectives and adapts to changing customer needs and market conditions. This involves reviewing KPIs, analyzing feedback, and making necessary adjustments to processes and procedures.
7.2 Benchmarking and Best Practices:
Benchmarking against industry leaders and adopting best practices helps identify areas for improvement and stay ahead of the competition. This involves learning from other organizations' successes and failures and implementing those lessons learned within your own organization.
7.3 Embracing Technological Advancements:
Technology plays a significant role in improving quality. Embracing new technologies, such as automation, data analytics, and AI, can help improve efficiency, reduce errors, and enhance customer satisfaction. Staying ahead of the technological curve is crucial for maintaining a competitive edge.
8. Supplier Management: Ensuring Consistent Quality
In many industries, the quality of supplied materials and components directly impacts the quality of the final product. Successful quality strategies incorporate robust supplier management practices:
8.1 Supplier Selection and Evaluation:
Careful selection and evaluation of suppliers are critical. This involves assessing suppliers' capabilities, quality systems, and past performance. Choosing reliable suppliers who adhere to high quality standards is crucial for consistent product quality.
8.2 Supplier Relationship Management:
Building strong relationships with suppliers fosters collaboration and communication. This involves working closely with suppliers to identify and resolve quality issues, share best practices, and continuously improve the quality of supplied goods and services.
8.3 Supplier Audits and Inspections:
Regular audits and inspections of suppliers' facilities and processes ensure they meet established quality standards. This proactive approach helps prevent quality problems from occurring in the first place.
Conclusion: Building a Culture of Quality
Implementing a successful quality strategy is an ongoing journey, not a destination. It requires a holistic approach that integrates all the elements discussed above. Ultimately, the key to success lies in fostering a culture where quality is not just a priority but an ingrained value—a culture where every employee feels empowered to contribute to excellence. By prioritizing these elements, organizations can not only improve product and service quality but also enhance operational efficiency, increase customer satisfaction, and drive sustainable growth.
Latest Posts
Related Post
Thank you for visiting our website which covers about A Successful Quality Strategy Features Which Of The Following Elements . We hope the information provided has been useful to you. Feel free to contact us if you have any questions or need further assistance. See you next time and don't miss to bookmark.