A Rivet Is To Be Inserted Into A Hole
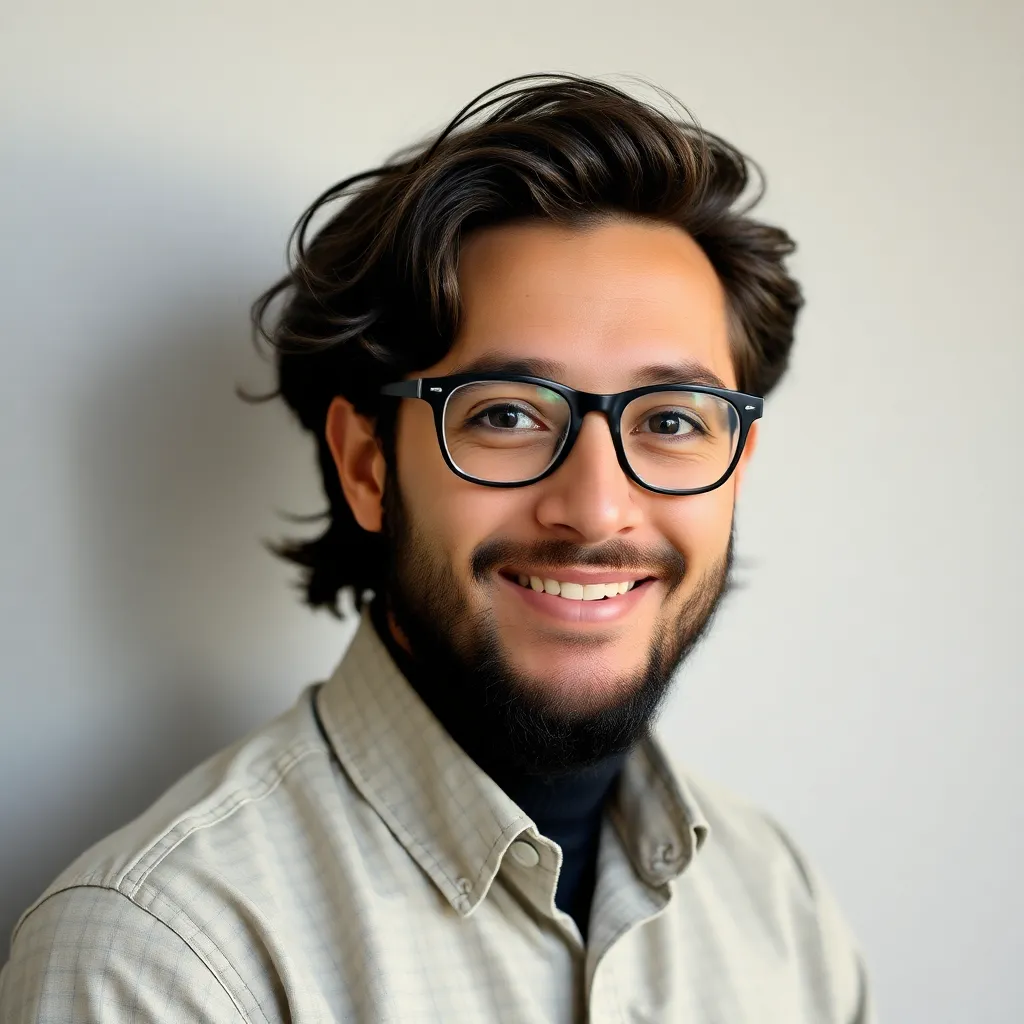
Holbox
Apr 14, 2025 · 7 min read

Table of Contents
- A Rivet Is To Be Inserted Into A Hole
- Table of Contents
- A Rivet Is to Be Inserted into a Hole: A Comprehensive Guide to Riveting
- Understanding Rivets: Types and Applications
- Solid Rivets: The Workhorses of Riveting
- Blind Rivets: Accessibility and Convenience
- Semi-Tubular Rivets: A Blend of Strength and Convenience
- Hole Preparation: The Foundation of a Successful Rivet Joint
- Determining the Correct Hole Size
- Ensuring Clean and Smooth Holes
- Accurate Hole Placement
- Rivet Insertion Techniques: Mastering the Process
- Solid Rivet Installation: The Traditional Approach
- Blind Rivet Installation: Ease and Efficiency
- Semi-Tubular Rivet Installation: A Balanced Approach
- Post-Installation Considerations: Ensuring Longevity
- Stress Relief: Preventing Premature Failures
- Protective Coatings: Enhancing Durability
- Troubleshooting Common Riveting Issues
- Choosing the Right Tools: Investing in Success
- Conclusion: The Art and Science of Riveting
- Latest Posts
- Latest Posts
- Related Post
A Rivet Is to Be Inserted into a Hole: A Comprehensive Guide to Riveting
Riveting, a time-tested joining method, secures materials by inserting a rivet into a hole. This seemingly simple process, however, involves a nuanced understanding of rivet types, hole preparation, insertion techniques, and the crucial post-installation considerations ensuring a strong, reliable joint. This comprehensive guide delves into every aspect, transforming your knowledge from novice to expert.
Understanding Rivets: Types and Applications
Before tackling the insertion process, it's crucial to understand the diverse world of rivets. The choice of rivet depends heavily on the materials being joined, the required strength, the accessibility of the joint, and the aesthetic requirements.
Solid Rivets: The Workhorses of Riveting
Solid rivets, the most common type, are cylindrical fasteners with a head on one end. They are driven into place, permanently deforming the shank to create a tight, secure joint. Solid rivets require a separate process to form the second head, usually via hammering or specialized tools. This ensures a robust mechanical lock.
- Common Materials: Steel, aluminum, copper, brass, and stainless steel, each offering varying strengths and corrosion resistance. The material selection is dictated by the application environment and the materials being fastened.
- Applications: Structural applications, automotive parts, aerospace components, and general fabrication. The versatility of solid rivets makes them suitable for a broad spectrum of projects.
- Advantages: High shear strength, simple design, relatively inexpensive.
- Disadvantages: Requires specialized tools for head formation, not suitable for applications requiring frequent disassembly.
Blind Rivets: Accessibility and Convenience
Blind rivets, also known as pop rivets, are designed for applications where access to only one side of the joint is possible. They are particularly advantageous in confined spaces where conventional riveting methods are impractical. A mandrel is pulled through the rivet body, expanding the shank to create the second head. This offers both efficiency and convenience.
- Materials: Aluminum, steel, stainless steel, and various specialized alloys, chosen based on application requirements.
- Applications: Automotive body panels, HVAC systems, electronics enclosures, and other applications where access is limited.
- Advantages: Ease of installation, requires access to only one side of the work, fast and efficient.
- Disadvantages: Potentially lower shear strength compared to some solid rivets, the mandrel must be broken off and removed after installation.
Semi-Tubular Rivets: A Blend of Strength and Convenience
Semi-tubular rivets offer a middle ground between solid and blind rivets. They have a pre-formed head and a hollow shank. While they don't provide the one-sided access of blind rivets, their ease of installation compared to solid rivets makes them a popular choice.
- Materials: Similar to solid and blind rivets, the selection depends on the application and desired properties.
- Applications: Applications where access to both sides is possible but using solid rivets may be cumbersome.
- Advantages: Relatively easy installation compared to solid rivets, stronger than blind rivets in some configurations.
- Disadvantages: Requires access to both sides of the joint, less convenient than blind rivets.
Hole Preparation: The Foundation of a Successful Rivet Joint
The success of any rivet joint hinges on meticulous hole preparation. Improperly sized or positioned holes lead to weak, unreliable joints prone to failure.
Determining the Correct Hole Size
The hole diameter must be carefully calculated to accommodate the rivet shank while preventing excessive deformation or loose fit. Rivet manufacturers provide detailed specifications, including recommended hole sizes for each rivet type and diameter. Using a drill bit of the incorrect size can result in either a rivet that doesn't fully fill the hole, leading to a weak joint, or a rivet that is excessively squeezed, leading to fracturing or deformation during installation.
Ensuring Clean and Smooth Holes
Cleanliness is paramount. Any burrs or irregularities in the holes can hinder rivet insertion, leading to uneven stress distribution and potential joint failure. Deburring tools, such as countersinks and deburring bits, are essential for preparing pristine holes. A sharp drill bit will minimize the risk of burr formation. The use of cutting oil or lubricant can also assist in producing cleaner holes and reducing friction.
Accurate Hole Placement
Precise hole placement is crucial. Any deviation from the design specifications can induce uneven stress, potentially leading to premature failure. Using accurate jigs, templates, or even simple marking tools is essential to maintain precision.
Rivet Insertion Techniques: Mastering the Process
The actual rivet insertion process varies depending on the rivet type, but some general principles apply across the board.
Solid Rivet Installation: The Traditional Approach
Installing solid rivets typically involves the following steps:
- Hole Preparation: Ensure the holes are clean, smooth, and the correct size.
- Rivet Insertion: Carefully insert the rivet into the holes.
- Head Formation: Use a rivet set (usually a hammer and a specialized anvil) to form the second head. This process requires skill and precision to ensure uniform deformation and a secure joint. Incorrect hammering can lead to deformation of the material being joined or cause the rivet to snap.
- Inspection: Check for any imperfections or loose rivets.
Blind Rivet Installation: Ease and Efficiency
Blind rivets offer a more straightforward installation process:
- Hole Preparation: As with solid rivets, the holes must be correctly sized and clean.
- Rivet Insertion: Insert the rivet into the holes.
- Setting Tool: Use a specialized setting tool that pulls the mandrel, expanding the rivet shank and forming the second head on the opposite side.
- Mandrel Removal: Break off the protruding mandrel after the head is formed.
- Inspection: Verify the proper head formation and ensure the rivet is securely installed.
Semi-Tubular Rivet Installation: A Balanced Approach
Semi-tubular rivet installation is simpler than solid rivets but requires access to both sides:
- Hole Preparation: Clean, correctly sized holes are essential.
- Rivet Insertion: Insert the rivet into the holes, ensuring the pre-formed head is on the accessible side.
- Head Formation: Use a rivet set to form the second head on the other side of the workpiece.
- Inspection: Check for flaws and ensure the rivet is firmly seated.
Post-Installation Considerations: Ensuring Longevity
Even after successful installation, certain steps are crucial for ensuring the longevity of the rivet joint.
Stress Relief: Preventing Premature Failures
Some types of riveting can induce stress in the joined materials. In sensitive applications, stress-relief techniques, such as annealing, might be necessary to prevent premature failures. This is particularly relevant for high-strength materials where stress concentrations can compromise the joint integrity.
Protective Coatings: Enhancing Durability
Applying protective coatings, such as paints, primers, or specialized sealants, can significantly enhance the durability of the rivet joint, especially in harsh environments. This prevents corrosion and protects the rivet and the surrounding materials from environmental degradation.
Troubleshooting Common Riveting Issues
Several common issues can arise during the riveting process. Knowing how to troubleshoot them is vital:
- Buckled or Damaged Rivets: This usually indicates incorrect hole size or excessive force during installation.
- Loose Rivets: This suggests insufficient force during head formation or incorrect hole size.
- Uneven Head Formation: This indicates improper tool usage or insufficient force.
- Rivet Breakage: This can result from using a rivet that's not suitable for the materials or excessive force.
Careful attention to detail and proper technique minimize these problems.
Choosing the Right Tools: Investing in Success
Choosing the right tools for the job is crucial for achieving successful and reliable rivet joints. The tools needed vary greatly depending on the type of rivet being used:
- Drill Bits: High-quality drill bits are essential for creating accurate and smooth holes. The correct diameter is essential to ensure a proper fit.
- Rivet Sets: These specialized tools are necessary for forming the heads of solid and semi-tubular rivets.
- Blind Rivet Setting Tools: These tools are specifically designed for setting blind rivets, pulling the mandrel and forming the second head.
- Countersinks: These tools create a countersunk hole, allowing the rivet head to sit flush with the surface.
- Deburring Tools: These tools remove burrs and irregularities from the holes, ensuring a smooth insertion and reducing the risk of damage to the rivet.
Investing in quality tools will ensure efficient and reliable riveting.
Conclusion: The Art and Science of Riveting
Successfully inserting a rivet into a hole is more than just a mechanical process. It's a blend of art and science, requiring a thorough understanding of rivet types, hole preparation techniques, and the intricacies of the insertion process. By carefully selecting the appropriate rivet type, meticulously preparing the holes, employing the right tools, and diligently observing post-installation procedures, you can create strong, durable, and reliable joints that stand the test of time. Mastering the art of riveting opens up a world of possibilities for projects ranging from simple repairs to complex engineering feats. Remember that consistent practice and attention to detail are essential for achieving consistently high-quality results.
Latest Posts
Latest Posts
-
Exercise 14 Review Sheet Nervous Tissue
Apr 24, 2025
-
The Cutaneous Membrane Is Blank To The Muscles
Apr 24, 2025
-
In The Passage Wilde Uses To Achieve An Aesthetic Impact
Apr 24, 2025
-
From Which Source Is A Decision Most Likely
Apr 24, 2025
-
Z 1 3 5 Tribromo 2 Pentene
Apr 24, 2025
Related Post
Thank you for visiting our website which covers about A Rivet Is To Be Inserted Into A Hole . We hope the information provided has been useful to you. Feel free to contact us if you have any questions or need further assistance. See you next time and don't miss to bookmark.