A Process With A Calculated Positive Q
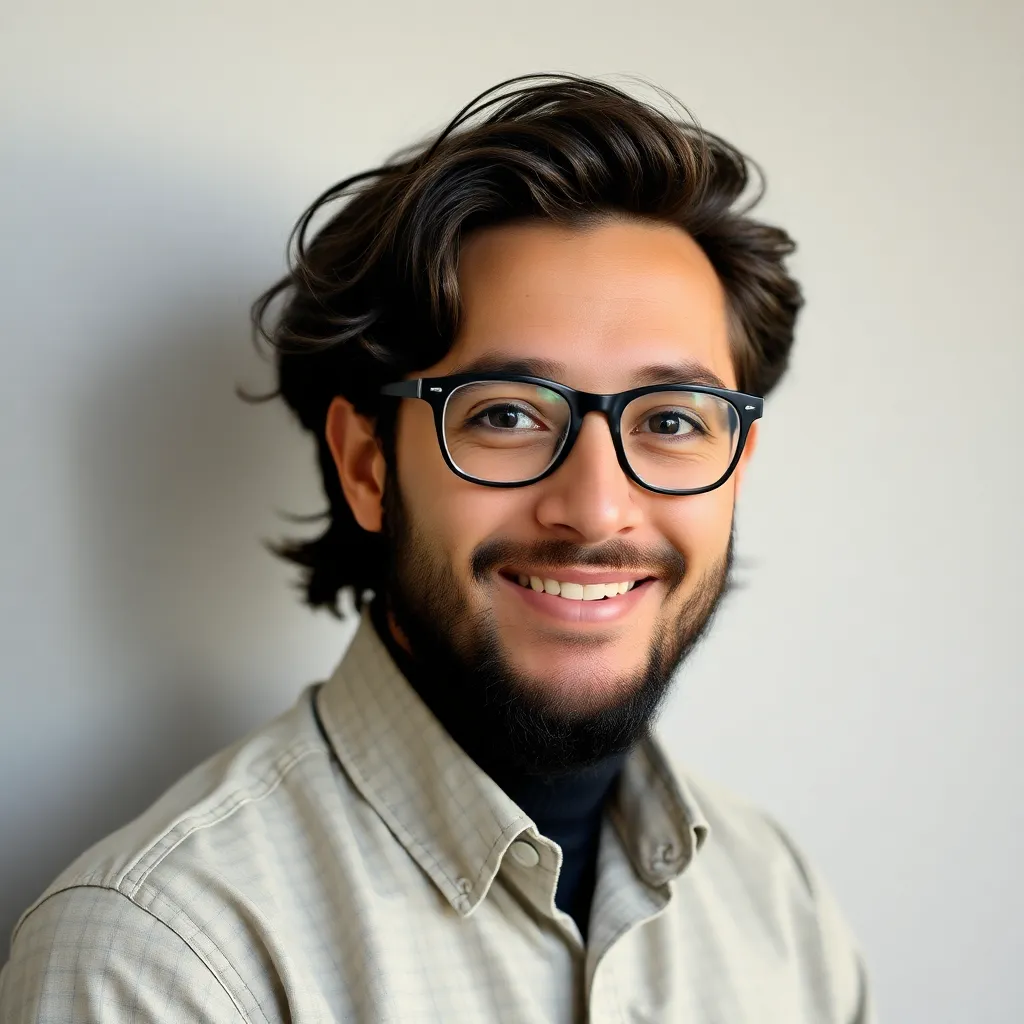
Holbox
Mar 27, 2025 · 6 min read
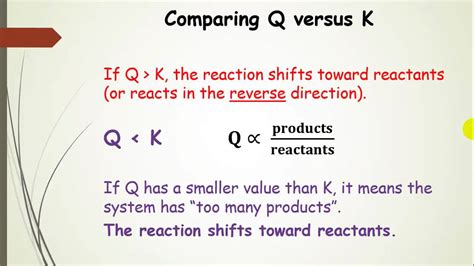
Table of Contents
- A Process With A Calculated Positive Q
- Table of Contents
- A Process with a Calculated Positive Q: Understanding and Achieving Process Efficiency
- What is a Process with a Calculated Positive Q?
- Understanding Q: Cpk and Ppk
- Calculating Q (Cpk and Ppk)
- Achieving a Positive Q Value: Practical Strategies
- 1. Process Mapping and Analysis:
- 2. Data Collection and Analysis:
- 3. Root Cause Analysis:
- 4. Process Improvement Techniques:
- 5. Implementing Change and Monitoring Results:
- 6. Training and Employee Engagement:
- 7. Regular Process Audits:
- Applications of Positive Q Processes Across Industries
- Conclusion: The Importance of a Positive Q Value
- Latest Posts
- Latest Posts
- Related Post
A Process with a Calculated Positive Q: Understanding and Achieving Process Efficiency
In the realm of process improvement and operational excellence, the concept of "Q" – often represented as Process Capability Index (Cpk) or Process Performance Index (Ppk) – plays a pivotal role in evaluating process effectiveness and identifying areas for enhancement. A positive Q value signifies that a process is capable of meeting pre-defined specifications, while a negative value indicates a significant deviation and the need for immediate corrective actions. This comprehensive guide delves into the intricacies of processes with calculated positive Q values, exploring its significance, calculation methods, practical applications, and implications for overall business success.
What is a Process with a Calculated Positive Q?
A process with a calculated positive Q signifies that the process consistently produces outputs within the acceptable limits defined by the specifications. This indicates a high level of process control and predictability. A positive Q value demonstrates that the process is not only meeting requirements but is also exhibiting a degree of robustness against potential variations or disruptions. The higher the Q value, the more capable and reliable the process is deemed to be. It's a key metric for continuous improvement initiatives.
Understanding Q: Cpk and Ppk
The Q value itself doesn't exist as a standalone metric. Instead, it's represented by either Cpk (Process Capability Index) or Ppk (Process Performance Index). Both provide insights into process capability, but they differ in their approach:
-
Cpk (Process Capability Index): Focuses on the process's inherent capability under controlled conditions. It assesses the ability of a process to consistently produce outputs within specified tolerance limits, assuming that the process is stable and in control. A Cpk value greater than 1 generally indicates that the process is capable of meeting the specified requirements.
-
Ppk (Process Performance Index): Considers the actual process performance over a given period, encompassing both controlled and uncontrolled variations. It accounts for both the inherent variability of the process and any external factors that might impact its output. A Ppk value greater than 1 also signals an acceptable level of process performance.
In essence, Cpk offers a snapshot of the process's potential, while Ppk reveals its actual performance. Both, however, contribute to the overall understanding of "Q" – the process's ability to deliver as expected.
Calculating Q (Cpk and Ppk)
The calculation of Cpk and Ppk involves several key parameters:
- Mean (μ): The average of the process output.
- Standard Deviation (σ): A measure of the process variability or dispersion around the mean.
- Upper Specification Limit (USL): The maximum acceptable value of the process output.
- Lower Specification Limit (LSL): The minimum acceptable value of the process output.
Cpk Calculation:
Cpk is calculated as the minimum of two values:
- Cpk (Upper) = (USL - μ) / (3σ)
- Cpk (Lower) = (μ - LSL) / (3σ)
Cpk = min[Cpk (Upper), Cpk (Lower)]
Ppk Calculation:
Ppk is similar but uses the process's overall standard deviation (σ) calculated from historical data, which reflects actual performance, including both common and special cause variation:
- Ppk (Upper) = (USL - μ) / (3σ<sub>p</sub>) where σ<sub>p</sub> is the overall standard deviation from the historical data
- Ppk (Lower) = (μ - LSL) / (3σ<sub>p</sub>) where σ<sub>p</sub> is the overall standard deviation from the historical data
Ppk = min[Ppk (Upper), Ppk (Lower)]
Interpreting the Results:
- Cpk/Ppk > 1.33: Indicates excellent process capability; the process consistently produces outputs within the specifications with minimal variation.
- Cpk/Ppk > 1.00: Suggests adequate process capability; the process mostly meets the requirements, but there's room for improvement.
- Cpk/Ppk < 1.00: Signals inadequate process capability; the process frequently produces outputs outside the acceptable limits, requiring immediate corrective actions.
Achieving a Positive Q Value: Practical Strategies
Achieving and maintaining a positive Q value requires a systematic and data-driven approach. Here are some key strategies:
1. Process Mapping and Analysis:
Begin by thoroughly mapping the entire process to understand its various steps, inputs, outputs, and potential points of failure. Techniques like Value Stream Mapping (VSM) can be valuable in visualizing the process flow and identifying areas for improvement.
2. Data Collection and Analysis:
Gather comprehensive data on the process outputs, paying close attention to the variability and distribution of the data. Statistical process control (SPC) charts, such as control charts and histograms, are crucial tools for monitoring process behavior and identifying potential problems.
3. Root Cause Analysis:
Once areas of concern are identified, conduct a thorough root cause analysis to pinpoint the underlying reasons for the process variability or deviations from specifications. Tools such as the "5 Whys" technique or Fishbone diagrams can be helpful in this stage.
4. Process Improvement Techniques:
Employ appropriate process improvement techniques to address the identified root causes and enhance process capability. Some effective approaches include:
- Lean Manufacturing Principles: Focuses on eliminating waste and optimizing the process flow.
- Six Sigma Methodology: Aims to reduce process variation and achieve near-zero defects.
- Design of Experiments (DOE): Helps to systematically identify the optimal process parameters to minimize variability.
- Kaizen (Continuous Improvement): Emphasizes incremental improvements over time.
5. Implementing Change and Monitoring Results:
Once improvements are implemented, carefully monitor the process performance to assess their effectiveness. Continue to collect and analyze data to track the changes in the Q value and make further adjustments as needed.
6. Training and Employee Engagement:
Properly train employees on the improved processes and empower them to identify and address potential issues. Engaging employees in the continuous improvement process is crucial for sustained success.
7. Regular Process Audits:
Conduct regular audits to ensure that the improved processes are being consistently followed and that the desired level of process capability is being maintained. These audits should be part of a larger quality management system.
Applications of Positive Q Processes Across Industries
Processes with consistently positive Q values are vital across various industries. Examples include:
- Manufacturing: Maintaining tight tolerances in manufacturing processes to produce high-quality products that meet customer specifications.
- Healthcare: Ensuring accurate and timely delivery of medical services to maintain patient safety and improve outcomes.
- Finance: Implementing robust risk management processes to minimize financial losses and ensure regulatory compliance.
- Software Development: Developing reliable and high-quality software products that meet user requirements and minimize bugs.
- Customer Service: Delivering consistent and high-quality customer service experiences to enhance customer satisfaction and loyalty.
In each of these industries, a process with a calculated positive Q value translates directly to improved efficiency, reduced costs, enhanced quality, and increased customer satisfaction.
Conclusion: The Importance of a Positive Q Value
A process with a calculated positive Q value is a cornerstone of operational excellence. By focusing on improving process capability and reducing variation, organizations can achieve significant improvements in efficiency, quality, and overall business performance. The pursuit of a positive Q value is not just a statistical exercise; it's a continuous improvement journey that requires a commitment to data-driven decision-making, process optimization, and employee engagement. Organizations that consistently strive for positive Q values across their operations are better positioned to thrive in today's competitive landscape. The consistent monitoring and refinement of processes ensures sustained excellence and provides a robust foundation for future growth and success. Investing the time and resources in achieving and maintaining high Q values is an investment in the long-term viability and prosperity of any organization. The principles outlined above provide a roadmap for achieving and sustaining this crucial aspect of operational excellence.
Latest Posts
Latest Posts
-
Which Statement Is True Regarding Primary Dysmenorrhea Select All
Mar 30, 2025
-
Acids Bases Ph And Buffers Lab
Mar 30, 2025
-
Which Of The Following Is Not A Characteristic Of Neurons
Mar 30, 2025
-
For Which Of The Following Is Potential Energy Decreasing
Mar 30, 2025
-
How Should You Begin Your Sales Presentation
Mar 30, 2025
Related Post
Thank you for visiting our website which covers about A Process With A Calculated Positive Q . We hope the information provided has been useful to you. Feel free to contact us if you have any questions or need further assistance. See you next time and don't miss to bookmark.