A Motor Drives A Pulley And Belt System
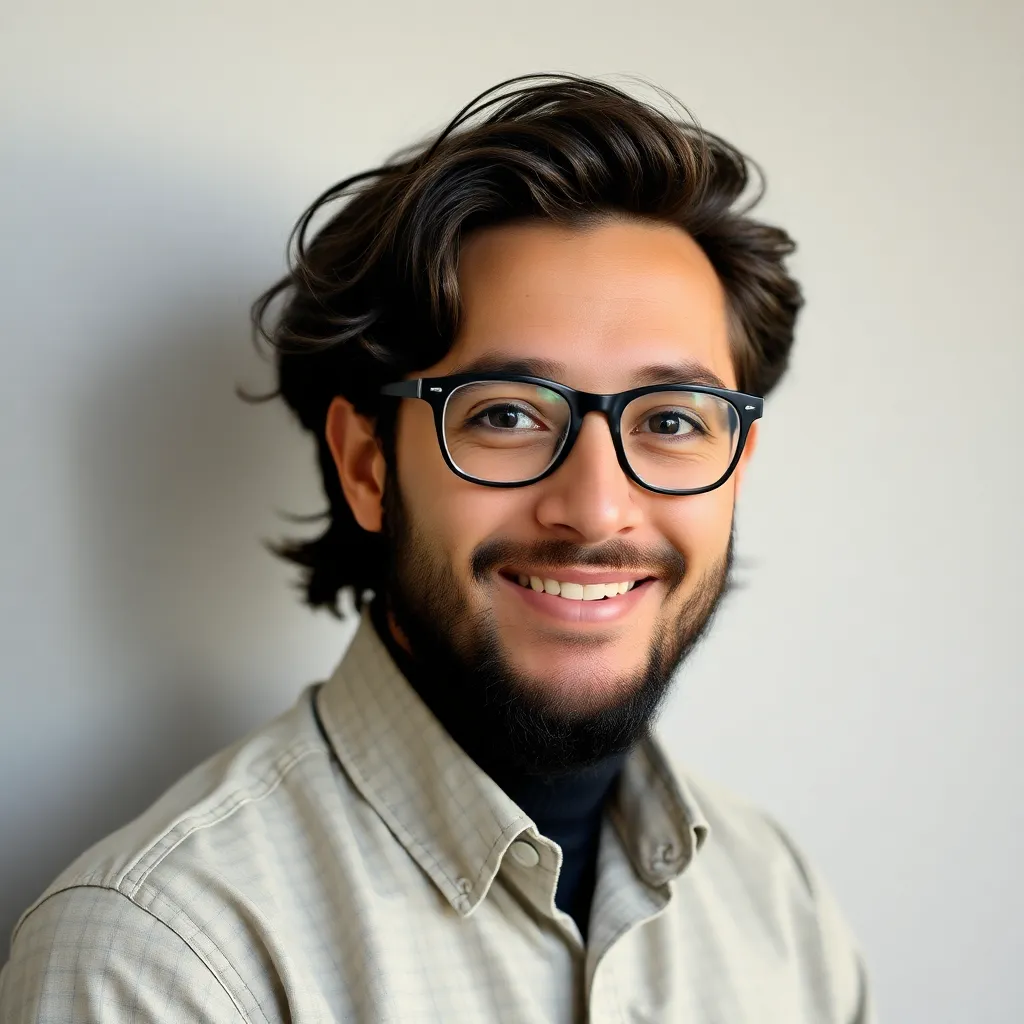
Holbox
Apr 02, 2025 · 6 min read
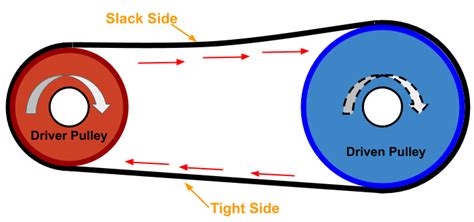
Table of Contents
- A Motor Drives A Pulley And Belt System
- Table of Contents
- Motor Drives a Pulley and Belt System: A Comprehensive Guide
- Understanding the Fundamentals: Motors, Pulleys, and Belts
- The Motor: The Power Source
- The Pulley: The Torque Transfer Agent
- The Belt: The Mechanical Link
- System Design and Calculations: Optimizing Performance
- Speed and Torque Ratios
- Belt Tension: Finding the Sweet Spot
- Pulley Alignment: Precision is Key
- Applications Across Industries
- Manufacturing and Industrial Automation:
- Automotive Industry:
- Agriculture:
- Household Appliances:
- Troubleshooting and Maintenance
- Common Problems:
- Maintenance Procedures:
- Advanced Considerations and Future Trends
- Advanced Belt Materials:
- Smart Sensors and Monitoring:
- Energy Efficiency Improvements:
- Conclusion
- Latest Posts
- Latest Posts
- Related Post
Motor Drives a Pulley and Belt System: A Comprehensive Guide
A motor driving a pulley and belt system is a fundamental mechanism in countless mechanical applications, from simple household appliances to complex industrial machinery. Understanding its principles, components, and applications is crucial for engineers, technicians, and anyone interested in mechanical systems. This comprehensive guide will delve into the intricacies of this system, covering everything from basic concepts to advanced considerations.
Understanding the Fundamentals: Motors, Pulleys, and Belts
The core of this system lies in three interconnected components: the motor, the pulley, and the belt. Let's examine each individually before exploring their synergistic operation.
The Motor: The Power Source
The motor serves as the power source, converting electrical energy into mechanical rotational energy. Various motor types can be employed, each with its own advantages and disadvantages:
-
AC Motors: These are widely used due to their robustness, simplicity, and relatively low cost. Subtypes include induction motors (common in industrial settings), synchronous motors (known for precise speed control), and universal motors (found in many household appliances).
-
DC Motors: These offer precise speed control and are often used in applications requiring variable speed, such as robotics and automation systems. Brushed DC motors are simpler but require more maintenance, while brushless DC motors are more efficient and durable.
-
Stepper Motors: These motors provide precise rotational control, allowing for accurate positioning and movement. They are commonly used in applications like 3D printers and CNC machines.
The selection of the appropriate motor depends heavily on the application's specific power requirements, speed needs, control precision, and environmental conditions. Torque, speed, and power are crucial motor specifications to consider when designing a pulley and belt system.
The Pulley: The Torque Transfer Agent
Pulleys are wheels with grooved rims designed to guide and grip belts. They act as intermediaries, transferring rotational motion and torque from the motor to the driven component. Key considerations for pulley selection include:
-
Diameter: The pulley diameter directly affects the speed and torque ratios. A smaller pulley increases speed but reduces torque, while a larger pulley decreases speed but increases torque.
-
Groove Profile: The shape of the pulley groove is designed to match the belt profile, ensuring efficient power transmission and minimizing slippage. Common profiles include V-belts, flat belts, and toothed belts.
-
Material: Pulley materials are selected based on strength, durability, and resistance to wear and tear. Common materials include steel, cast iron, aluminum, and various plastics.
The proper selection of pulley diameter and material is essential for optimal performance and longevity of the system.
The Belt: The Mechanical Link
The belt acts as the mechanical link between the motor pulley and the driven pulley, transmitting power through friction or positive engagement. Different belt types offer distinct characteristics:
-
V-Belts: These are widely used in industrial applications due to their ability to transmit high power with minimal slippage. The V-shaped profile enhances grip within the pulley groove.
-
Flat Belts: These are suitable for applications requiring high speed and smooth operation. They are less effective at transmitting high torque compared to V-belts.
-
Toothed Belts (Timing Belts): These provide precise speed and timing control, eliminating slippage. They are commonly used in applications requiring synchronized movement, such as camshafts in engines and conveyor systems.
-
Conveyor Belts: While not directly part of a traditional pulley and belt system, conveyor belts utilize the same principle for material handling.
The choice of belt type depends on the power transmission requirements, speed, torque, and the need for precise timing.
System Design and Calculations: Optimizing Performance
Designing an efficient pulley and belt system requires careful consideration of several factors.
Speed and Torque Ratios
The speed and torque ratios between the motor and the driven component are determined by the relative diameters of the pulleys. The formula is:
(Speed of driven pulley) / (Speed of motor pulley) = (Diameter of motor pulley) / (Diameter of driven pulley)
(Torque of driven pulley) / (Torque of motor pulley) = (Diameter of driven pulley) / (Diameter of motor pulley)
This relationship demonstrates the inverse relationship between speed and torque. Increasing the driven pulley's diameter increases torque but decreases speed, and vice versa.
Belt Tension: Finding the Sweet Spot
Appropriate belt tension is crucial. Insufficient tension leads to slippage and reduced power transmission, while excessive tension increases wear and tear on the belt and pulleys, potentially leading to premature failure. A tensioning mechanism, such as an adjustable mounting bracket or a spring-loaded system, is often incorporated to maintain optimal belt tension.
Pulley Alignment: Precision is Key
Precise alignment of the pulleys is critical to prevent premature belt wear and ensure efficient power transmission. Misalignment causes uneven belt loading, leading to increased friction and potential failure. Proper alignment tools and procedures should be used during installation.
Applications Across Industries
The motor-driven pulley and belt system finds widespread applications in various industries:
Manufacturing and Industrial Automation:
- Conveyor Systems: Moving materials along production lines.
- Machine Tools: Powering cutting, grinding, and shaping operations.
- Packaging Machinery: Driving packaging processes.
- Robotics: Controlling robotic arm movements.
Automotive Industry:
- Engine Timing: Synchronizing engine components.
- Accessory Drives: Powering alternators, water pumps, and power steering.
Agriculture:
- Farm Machinery: Powering harvesting and tillage equipment.
Household Appliances:
- Washing Machines: Driving the drum's rotation.
- Blenders: Rotating the blades.
Troubleshooting and Maintenance
Regular maintenance is essential for ensuring the longevity and efficiency of a pulley and belt system.
Common Problems:
- Belt Slippage: Caused by insufficient tension, worn belt, or misaligned pulleys.
- Belt Wear: Caused by excessive tension, misalignment, or poor quality belt.
- Pulley Wear: Caused by excessive load, misalignment, or poor lubrication.
- Bearing Failure: Caused by lack of lubrication or excessive load.
Maintenance Procedures:
- Regular Inspection: Check for belt wear, pulley alignment, and signs of bearing damage.
- Tension Adjustment: Adjust belt tension as needed.
- Lubrication: Lubricate bearings as recommended by the manufacturer.
- Belt Replacement: Replace worn or damaged belts promptly.
Advanced Considerations and Future Trends
While the fundamental principles remain consistent, advancements in materials, designs, and control systems are continually refining pulley and belt systems.
Advanced Belt Materials:
New materials are being developed to enhance belt durability, strength, and resistance to wear and tear. This includes high-strength composites and specialized elastomers.
Smart Sensors and Monitoring:
Incorporating smart sensors can provide real-time monitoring of belt tension, speed, and temperature, enabling predictive maintenance and reducing downtime.
Energy Efficiency Improvements:
Focus is shifting towards designing more energy-efficient systems through optimized pulley ratios, low-friction belts, and advanced motor controls.
Conclusion
The motor driving a pulley and belt system is a fundamental and versatile mechanism with applications across numerous industries. Understanding the underlying principles, component selection, system design, and maintenance procedures is essential for maximizing efficiency, reliability, and longevity. Ongoing advancements in materials science and control systems promise to further enhance the capabilities and performance of this vital mechanical system. The future of pulley and belt systems lies in improved efficiency, enhanced monitoring capabilities, and the integration of smart technologies for optimized performance and reduced maintenance.
Latest Posts
Latest Posts
-
Select The Correct Iupac Name For The Branched Chain Alkane
Apr 04, 2025
-
What Types Of Orbital Overlap Occur In Cumulene
Apr 04, 2025
-
When Does A Router Use Arp
Apr 04, 2025
-
Choose Correct Interpretation For Staphylococcus Epidermidis Result
Apr 04, 2025
-
Molander Corporation Is A Distributor Of A Sun Umbrella
Apr 04, 2025
Related Post
Thank you for visiting our website which covers about A Motor Drives A Pulley And Belt System . We hope the information provided has been useful to you. Feel free to contact us if you have any questions or need further assistance. See you next time and don't miss to bookmark.