A Manufacturing Company Calculates Cost Of Goods Sold As Follows
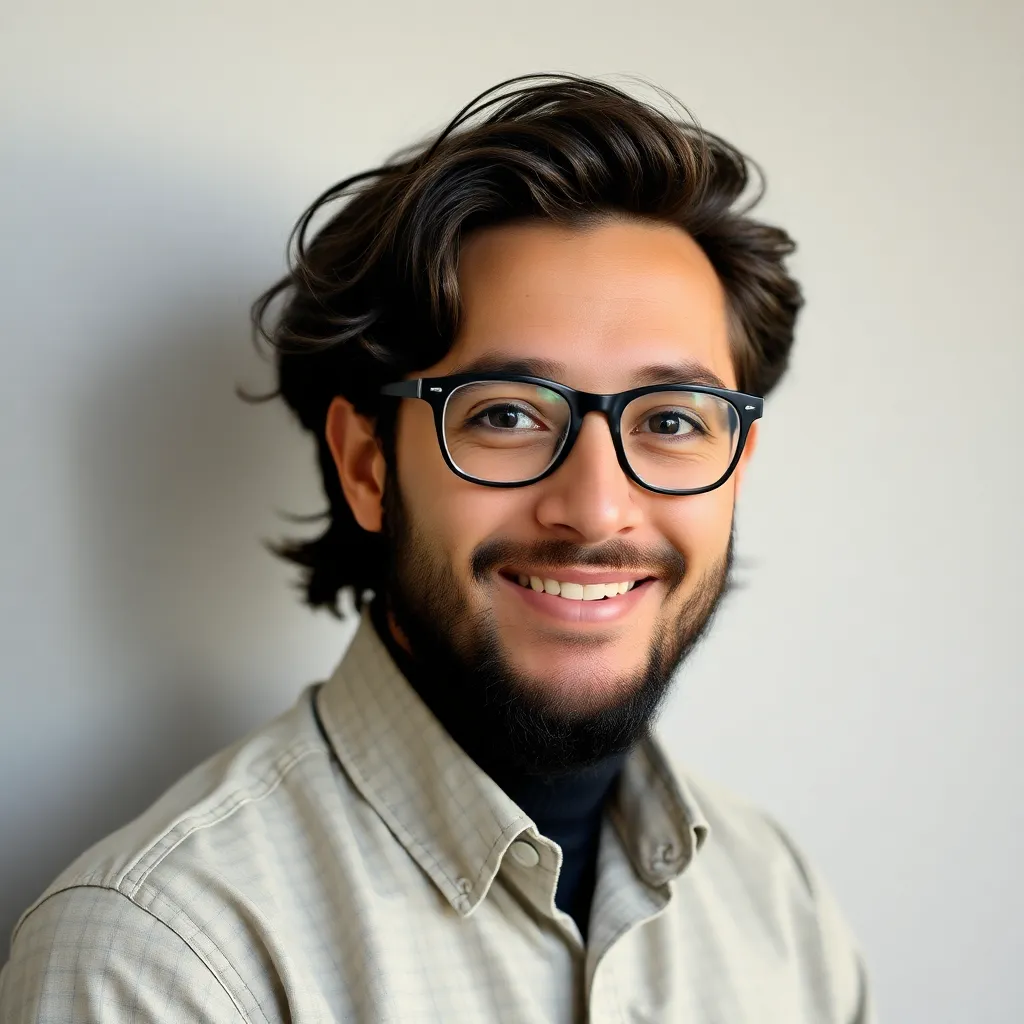
Holbox
Mar 27, 2025 · 6 min read
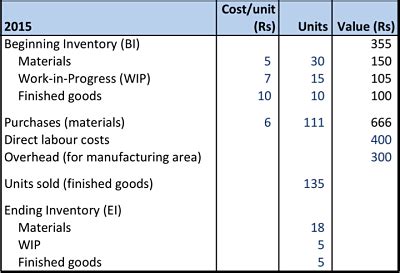
Table of Contents
- A Manufacturing Company Calculates Cost Of Goods Sold As Follows
- Table of Contents
- Calculating the Cost of Goods Sold (COGS) in a Manufacturing Company: A Comprehensive Guide
- Understanding the Components of COGS in Manufacturing
- 1. Direct Materials:
- 2. Direct Labor:
- 3. Manufacturing Overhead:
- Methods for Calculating COGS in Manufacturing
- 1. First-In, First-Out (FIFO):
- 2. Last-In, First-Out (LIFO):
- 3. Weighted-Average Cost:
- The COGS Formula for Manufacturing Companies
- Example Calculation of COGS for a Manufacturing Company
- Importance of Accurate COGS Calculation
- Advanced Considerations and Challenges in COGS Calculation
- Conclusion: Mastering COGS for Manufacturing Success
- Latest Posts
- Latest Posts
- Related Post
Calculating the Cost of Goods Sold (COGS) in a Manufacturing Company: A Comprehensive Guide
Calculating the cost of goods sold (COGS) accurately is crucial for any manufacturing company's financial health and profitability. COGS represents the direct costs associated with producing goods sold during a specific period. Understanding how to calculate COGS, and the nuances involved, is essential for accurate financial reporting, tax filings, and informed business decisions. This comprehensive guide delves into the intricacies of COGS calculation for manufacturing companies, exploring various methods and offering practical examples.
Understanding the Components of COGS in Manufacturing
Unlike simpler businesses, manufacturing COGS involves a more complex calculation due to the multi-stage production process. The key components include:
1. Direct Materials:
These are raw materials directly used in the production process and are easily traceable to the finished goods. Examples include:
- Raw materials: Steel for automotive parts, fabric for clothing, wood for furniture.
- Packaging materials: Boxes, labels, and containers directly associated with the product.
Calculating Direct Materials Costs: This involves tracking the cost of all raw materials used in production during the accounting period. Inventory management systems are crucial for accurate tracking.
2. Direct Labor:
This encompasses the wages and benefits paid to workers directly involved in the manufacturing process. This includes:
- Assembly line workers: Directly involved in assembling the product.
- Machine operators: Operating machinery used in production.
- Quality control inspectors: Ensuring the product meets quality standards.
Calculating Direct Labor Costs: This involves adding up all wages, salaries, and benefits paid to direct labor personnel during the accounting period. Overtime pay and other related expenses should also be included.
3. Manufacturing Overhead:
This represents indirect costs associated with the production process that are difficult to directly trace to specific products. Examples include:
- Factory rent: Cost of leasing or owning the manufacturing facility.
- Utilities: Electricity, gas, and water used in the factory.
- Depreciation of machinery and equipment: Allocation of the cost of equipment over its useful life.
- Factory supplies: Lubricants, cleaning supplies, and other consumables.
- Indirect labor: Wages of factory supervisors, maintenance personnel, and security guards.
Calculating Manufacturing Overhead Costs: This is often a complex process. Companies typically use a predetermined overhead rate to allocate overhead costs to individual products. This rate is calculated by dividing estimated total overhead costs by an allocation base, such as direct labor hours or machine hours.
Methods for Calculating COGS in Manufacturing
There are several methods used for calculating COGS, each with its own advantages and disadvantages:
1. First-In, First-Out (FIFO):
This method assumes that the oldest inventory items are sold first. It provides a more accurate reflection of current costs in times of fluctuating prices, as the cost of goods sold reflects the cost of older inventory.
Example: If a company purchases 100 units at $10 each and then 100 units at $12 each, and sells 150 units, the COGS under FIFO would be calculated as (100 units * $10) + (50 units * $12) = $1600.
2. Last-In, First-Out (LIFO):
This method assumes that the newest inventory items are sold first. It can be advantageous during periods of inflation as it results in a higher COGS and lower taxable income. However, LIFO is not permitted under IFRS (International Financial Reporting Standards).
Example: Using the same example as above, the COGS under LIFO would be calculated as (100 units * $12) + (50 units * $10) = $1700.
3. Weighted-Average Cost:
This method calculates the average cost of all inventory items available for sale during the period. This method is simpler to implement than FIFO or LIFO, but it may not reflect the true cost of goods sold if prices fluctuate significantly.
Example: Using the same example, the weighted average cost would be (($10 + $12)/2) = $11 per unit. The COGS for 150 units would be 150 units * $11 = $1650.
The COGS Formula for Manufacturing Companies
The general formula for calculating COGS in a manufacturing setting is:
Beginning Inventory + Purchases (Direct Materials) + Direct Labor + Manufacturing Overhead - Ending Inventory = Cost of Goods Sold
Let's break down each element:
- Beginning Inventory: The value of the finished goods inventory at the beginning of the accounting period.
- Purchases (Direct Materials): The cost of all direct materials purchased during the period.
- Direct Labor: The total cost of direct labor incurred during the period.
- Manufacturing Overhead: The total indirect costs associated with production during the period.
- Ending Inventory: The value of the finished goods inventory at the end of the accounting period.
Example Calculation of COGS for a Manufacturing Company
Let's illustrate with a hypothetical example:
XYZ Manufacturing Company – Year 2024
- Beginning Finished Goods Inventory: $50,000
- Direct Materials Purchased: $200,000
- Direct Labor: $150,000
- Manufacturing Overhead: $75,000
- Ending Finished Goods Inventory: $60,000
Calculation:
$50,000 (Beginning Inventory) + $200,000 (Direct Materials) + $150,000 (Direct Labor) + $75,000 (Manufacturing Overhead) - $60,000 (Ending Inventory) = $415,000 (Cost of Goods Sold)
Therefore, XYZ Manufacturing Company's cost of goods sold for 2024 is $415,000.
Importance of Accurate COGS Calculation
Accurate COGS calculation is critical for several reasons:
- Profitability Analysis: COGS is a crucial component in calculating gross profit and net profit. Inaccurate COGS can lead to misinterpretations of profitability.
- Inventory Management: Tracking COGS helps in monitoring inventory levels and identifying potential inefficiencies in the production process.
- Pricing Decisions: Understanding COGS enables businesses to set appropriate prices for their products to ensure profitability.
- Tax Reporting: COGS is a deductible expense, impacting the calculation of taxable income. Accurate reporting is crucial for compliance.
- Financial Reporting: Accurate COGS is essential for preparing accurate financial statements, including the income statement and balance sheet.
Advanced Considerations and Challenges in COGS Calculation
While the basic formula is relatively straightforward, several factors can complicate COGS calculation in manufacturing:
- Joint Products and By-Products: When multiple products are produced from a single production process, allocating costs to each product can be challenging. This often involves using allocation methods based on market values or production quantities.
- Work-in-Progress (WIP) Inventory: Managing and accounting for partially finished goods requires careful tracking and costing methodologies.
- Spoilage and Waste: Accounting for materials lost due to spoilage or waste requires adjusting the COGS calculation to reflect these losses.
- Obsolescence: Inventory that becomes obsolete due to technological advancements or changes in market demand necessitates adjustments to COGS.
- Changes in Accounting Methods: Switching between inventory costing methods (FIFO, LIFO, weighted-average) can require adjustments to COGS and necessitates careful planning and adherence to accounting principles.
Conclusion: Mastering COGS for Manufacturing Success
Calculating the cost of goods sold accurately is paramount for the success of any manufacturing company. Understanding the components of COGS, choosing an appropriate inventory costing method, and carefully tracking costs throughout the production process are all crucial steps in ensuring accurate financial reporting and informed business decisions. By mastering COGS calculation, manufacturing companies can optimize their operations, enhance profitability, and gain a stronger competitive edge in the marketplace. Regularly reviewing and refining your COGS calculation methods will ensure that your financial reporting remains accurate and reflects the true cost of producing your goods. This not only facilitates efficient internal management but also builds trust with stakeholders and regulatory bodies. Investing in robust inventory management systems and seeking professional accounting advice when necessary are crucial steps to ensure the accuracy and reliability of your COGS calculations.
Latest Posts
Latest Posts
-
Which Of The Following Elements Is Present In This Image
Mar 31, 2025
-
You Have Important Time Sensitive Information
Mar 31, 2025
-
Liquid Sodium Is Being Considered As An Engine Coolant
Mar 31, 2025
-
A Runner Runs Around The Track At A Constant Speed
Mar 31, 2025
-
Cause Of Doody Out Of Business
Mar 31, 2025
Related Post
Thank you for visiting our website which covers about A Manufacturing Company Calculates Cost Of Goods Sold As Follows . We hope the information provided has been useful to you. Feel free to contact us if you have any questions or need further assistance. See you next time and don't miss to bookmark.