A Maintenance Firm Has Gathered The Following
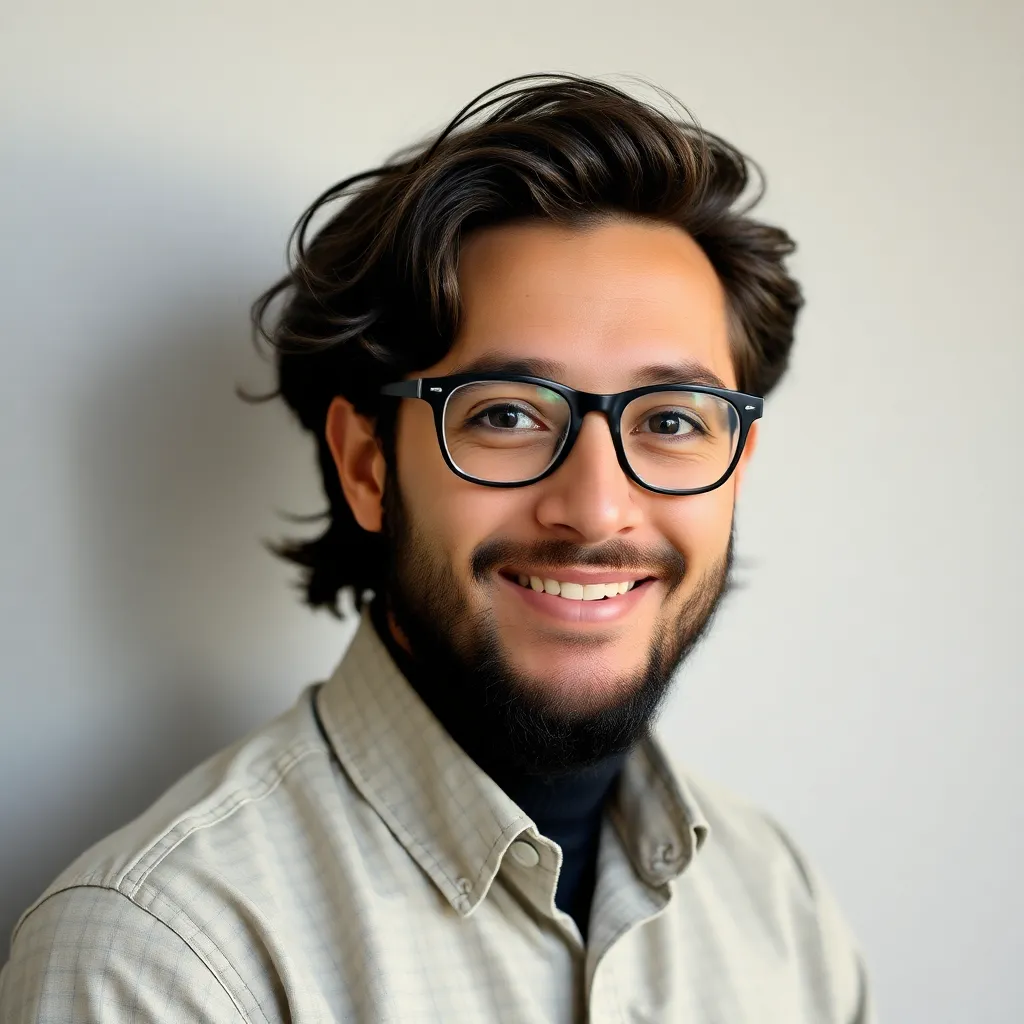
Holbox
Mar 16, 2025 · 6 min read
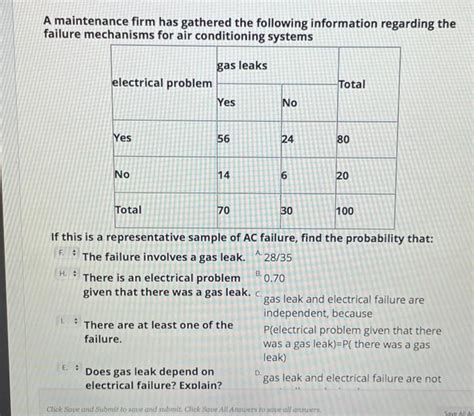
Table of Contents
Streamlining Your Business: A Comprehensive Guide to Maintenance Management for Peak Efficiency
Maintaining a smoothly running business requires more than just reacting to problems; it demands a proactive, strategic approach to maintenance management. Ignoring preventative measures can lead to costly downtime, safety hazards, and a decline in overall productivity. This comprehensive guide explores effective strategies for optimizing your maintenance operations, focusing on efficiency, cost-effectiveness, and improved asset lifespan.
The Importance of Proactive Maintenance Management
Reactive maintenance, or "fixing things when they break," is a short-sighted approach. It often results in:
- Unexpected Downtime: Equipment failure interrupts workflow, leading to lost production time and revenue.
- Increased Repair Costs: Addressing problems after they escalate significantly increases the cost of repair compared to preventative maintenance.
- Safety Risks: Malfunctioning equipment can pose serious safety hazards to employees and potentially customers.
- Shorter Asset Lifespan: Neglecting regular maintenance accelerates the deterioration of assets, shortening their lifespan and requiring premature replacements.
Proactive maintenance, on the other hand, involves scheduled inspections, preventative repairs, and predictive analysis to minimize breakdowns and extend the life of your assets. This approach fosters:
- Reduced Downtime: Preventative measures significantly decrease the likelihood of unexpected equipment failures.
- Lower Repair Costs: Addressing minor issues before they become major problems saves money in the long run.
- Improved Safety: Regular inspections and maintenance identify and address potential safety hazards proactively.
- Extended Asset Lifespan: Proper maintenance significantly extends the useful life of your assets, reducing the frequency of costly replacements.
Implementing a Robust Maintenance Management System
Creating a streamlined and efficient maintenance management system is crucial. Here's a step-by-step guide:
1. Asset Inventory and Documentation:
- Comprehensive Inventory: Create a detailed inventory of all your assets, including equipment, machinery, vehicles, and buildings. Include detailed specifications, purchase dates, and relevant documentation.
- Centralized Database: Utilize a Computerized Maintenance Management System (CMMS) or a spreadsheet to store this information centrally for easy access and analysis. This facilitates tracking of maintenance history and predicting future needs.
- Regular Audits: Conduct regular audits to ensure the accuracy and completeness of your asset inventory.
2. Developing a Preventative Maintenance Schedule:
- Manufacturer Recommendations: Refer to manufacturer guidelines for recommended maintenance schedules and procedures for your equipment.
- Historical Data Analysis: Analyze historical maintenance data to identify patterns and predict potential failures. This helps in prioritizing maintenance tasks based on risk assessment.
- Prioritization: Prioritize tasks based on criticality and potential impact on operations. Focus on critical assets that are essential for your business's functioning.
- Scheduled Inspections: Establish a clear schedule for routine inspections and preventative maintenance activities. Use calendar reminders and automated notifications to ensure adherence to the schedule.
3. Selecting the Right Maintenance Techniques:
Several approaches can be implemented, each with its own strengths and weaknesses:
- Preventative Maintenance (PM): This involves scheduled inspections and maintenance to prevent equipment failure before it occurs. This is the cornerstone of a robust maintenance strategy.
- Predictive Maintenance (PdM): This uses advanced technologies like sensors and data analytics to predict when equipment is likely to fail. This allows for targeted maintenance, reducing unnecessary work and maximizing efficiency.
- Condition-Based Maintenance (CBM): This focuses on monitoring the condition of equipment to determine when maintenance is necessary. This combines elements of preventative and predictive maintenance.
- Corrective Maintenance (CM): This involves repairing equipment after a failure. While necessary, it should be minimized through the use of preventative and predictive methods.
4. Optimizing Maintenance Processes:
- Standardized Procedures: Develop clear, standardized procedures for all maintenance tasks to ensure consistency and quality.
- Training and Skill Development: Invest in training your maintenance personnel to ensure they possess the necessary skills and knowledge to perform their tasks effectively and safely.
- Inventory Management: Implement a robust inventory management system to ensure that necessary spare parts and supplies are readily available. This minimizes downtime due to parts shortages.
- Technology Integration: Utilize CMMS software or other technological tools to streamline work orders, track maintenance history, manage inventory, and generate reports.
5. Data Analysis and Performance Monitoring:
- Key Performance Indicators (KPIs): Establish relevant KPIs to measure the effectiveness of your maintenance program. These could include downtime, repair costs, maintenance costs, Mean Time Between Failures (MTBF), and Mean Time To Repair (MTTR).
- Regular Reporting: Generate regular reports to track progress, identify areas for improvement, and demonstrate the ROI of your maintenance program.
- Continuous Improvement: Use data analysis to identify patterns, trends, and areas for optimization. Continuously refine your maintenance processes to maximize efficiency and minimize costs.
The Role of Technology in Modern Maintenance Management
Technology plays a crucial role in modernizing and optimizing maintenance operations. Here are some key technological advancements:
- Computerized Maintenance Management Systems (CMMS): These software solutions streamline work order management, scheduling, inventory tracking, and reporting. They provide a centralized platform for managing all aspects of maintenance.
- Internet of Things (IoT) Sensors: IoT sensors embedded in equipment can provide real-time data on equipment performance, allowing for predictive maintenance and early detection of potential problems.
- Artificial Intelligence (AI) and Machine Learning (ML): AI and ML algorithms can analyze vast amounts of data to identify patterns, predict failures, and optimize maintenance schedules.
- Augmented Reality (AR): AR technology can provide maintenance technicians with real-time information and guidance, improving efficiency and accuracy.
Cost-Effective Strategies for Maintenance Management
Implementing a robust maintenance program doesn't have to break the bank. Here are some cost-effective strategies:
- Prioritize Preventative Maintenance: Focus on preventative maintenance to avoid costly emergency repairs.
- Negotiate with Suppliers: Negotiate favorable pricing and contracts with suppliers for parts and services.
- Train Your Personnel: Investing in training reduces errors, downtime, and the need for external expertise.
- Utilize Technology Wisely: Select technologies that offer a good return on investment, focusing on solutions that address your specific needs.
- Regular Audits and Reviews: Conduct periodic audits and reviews to identify areas where costs can be reduced without compromising efficiency.
Building a Successful Maintenance Culture
Implementing a successful maintenance program requires more than just technology and procedures; it requires a cultural shift.
- Employee Engagement: Involve your maintenance team in the planning and implementation of the maintenance program. Their input and expertise are invaluable.
- Clear Communication: Maintain open and clear communication between the maintenance team and other departments.
- Continuous Improvement Mindset: Foster a culture of continuous improvement, encouraging the team to identify areas for optimization and innovation.
- Safety First: Prioritize safety in all maintenance activities. Provide adequate training and safety equipment.
Conclusion: A Proactive Approach to Success
By implementing a robust and proactive maintenance management system, businesses can significantly improve efficiency, reduce costs, and enhance the longevity of their assets. A combination of preventative and predictive maintenance strategies, coupled with the effective use of technology and a focus on employee engagement, is key to achieving optimal results. Remember, a well-maintained operation is a profitable operation. Investing in a comprehensive maintenance program is not an expense, but rather a strategic investment in the long-term success and sustainability of your business.
Latest Posts
Latest Posts
-
You Receive A Text Message From A Package Shipper
Mar 16, 2025
-
What Is The Definition For Mitigation Mission Area
Mar 16, 2025
-
Which Of The Following Are Fundamental Objectives Of Information Security
Mar 16, 2025
-
The Nose Is To The Cheekbones
Mar 16, 2025
-
Sales Mix Is The Proportion Of For Various Products
Mar 16, 2025
Related Post
Thank you for visiting our website which covers about A Maintenance Firm Has Gathered The Following . We hope the information provided has been useful to you. Feel free to contact us if you have any questions or need further assistance. See you next time and don't miss to bookmark.