A Horizontal Pipe Carries A Smoothly Flowing Liquid
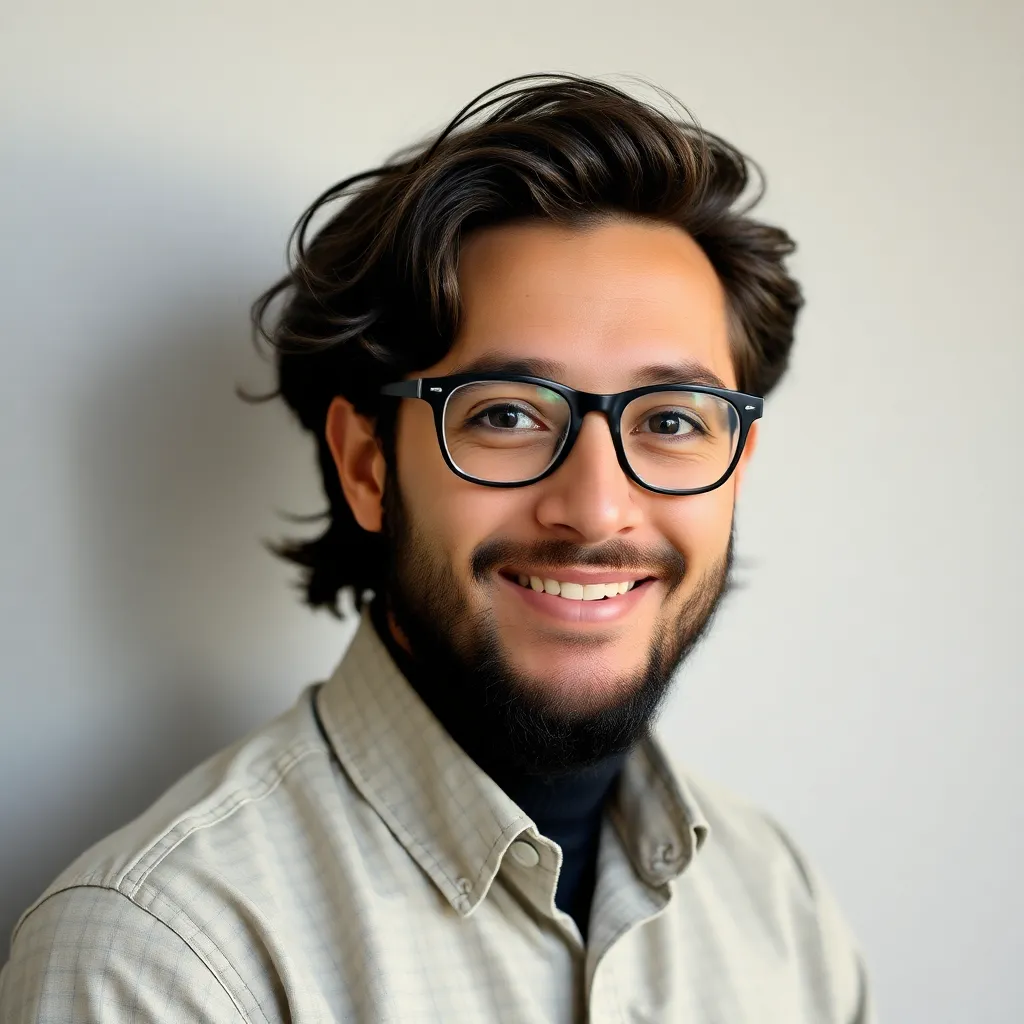
Holbox
May 10, 2025 · 6 min read
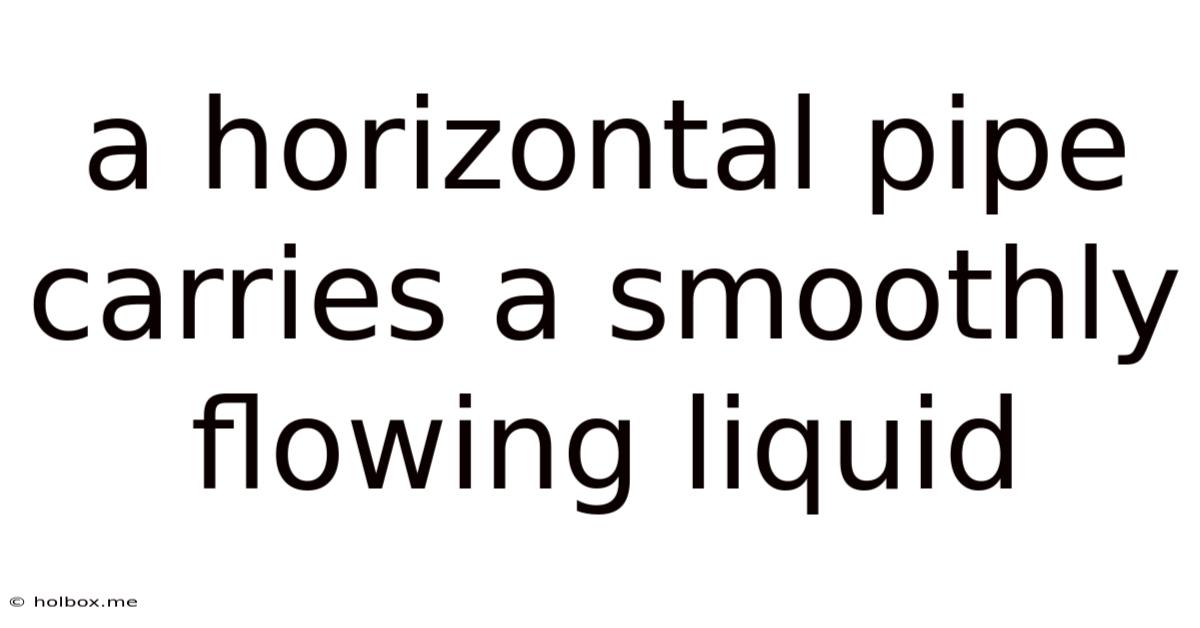
Table of Contents
- A Horizontal Pipe Carries A Smoothly Flowing Liquid
- Table of Contents
- A Horizontal Pipe Carrying a Smoothly Flowing Liquid: A Deep Dive into Fluid Mechanics
- Understanding Laminar and Turbulent Flow
- Laminar Flow: The Smooth Operator
- Turbulent Flow: A Chaotic Dance
- Factors Influencing Flow in a Horizontal Pipe
- 1. Reynolds Number (Re)
- 2. Pipe Diameter (D)
- 3. Fluid Properties (ρ and μ)
- 4. Pipe Roughness (ε)
- 5. Liquid Velocity (V)
- Pressure Drop in Horizontal Pipes: Understanding the Losses
- Major Losses: Friction in the Pipe
- Minor Losses: Fittings and Components
- Practical Applications and Implications
- Conclusion: A Complex Yet Essential Understanding
- Latest Posts
- Related Post
A Horizontal Pipe Carrying a Smoothly Flowing Liquid: A Deep Dive into Fluid Mechanics
Understanding the behavior of liquids flowing through pipes is crucial in numerous engineering applications, from designing efficient water distribution systems to optimizing oil pipelines. This article delves into the intricate dynamics of a smoothly flowing liquid within a horizontal pipe, exploring key concepts, influencing factors, and practical implications. We'll examine the principles of fluid mechanics governing this seemingly simple scenario, revealing a wealth of complexity hidden beneath the surface.
Understanding Laminar and Turbulent Flow
The nature of liquid flow within a pipe is primarily categorized into two distinct regimes: laminar and turbulent flow. This categorization is fundamentally determined by the Reynolds number (Re), a dimensionless quantity that represents the ratio of inertial forces to viscous forces within the fluid.
Laminar Flow: The Smooth Operator
Laminar flow, also known as streamline flow, is characterized by smooth, parallel layers of liquid moving in a consistent manner. There's minimal mixing between these layers, leading to a predictable and ordered flow pattern. In a horizontal pipe, laminar flow is typically observed at low Reynolds numbers. This means the viscous forces are dominant, effectively suppressing any chaotic tendencies. Visualizing laminar flow is like watching perfectly stacked sheets of paper sliding past each other without disruption. The velocity profile in laminar flow is parabolic, with the maximum velocity occurring at the center of the pipe and decreasing towards zero at the pipe walls due to the no-slip condition.
Key characteristics of laminar flow in a horizontal pipe:
- Predictable velocity profile: A parabolic velocity distribution.
- Low energy losses: Minimal frictional energy losses due to smooth flow.
- Low Reynolds number: Typically less than 2300 for a circular pipe.
- Easy to model mathematically: Allows for simpler calculations of pressure drop and flow rate.
Turbulent Flow: A Chaotic Dance
Turbulent flow, on the other hand, is characterized by chaotic and unpredictable movement of liquid particles. The flow is characterized by swirling eddies and mixing between layers, leading to increased energy dissipation. In a horizontal pipe, turbulent flow occurs at higher Reynolds numbers, where inertial forces dominate over viscous forces. The transition from laminar to turbulent flow is not abrupt; it's a gradual process influenced by various factors.
Key characteristics of turbulent flow in a horizontal pipe:
- Irregular velocity profile: No easily defined velocity profile.
- High energy losses: Significant frictional energy losses due to mixing and eddies.
- High Reynolds number: Typically greater than 4000 for a circular pipe.
- Complex to model mathematically: Requires advanced computational fluid dynamics (CFD) techniques.
Factors Influencing Flow in a Horizontal Pipe
Several factors significantly influence the flow characteristics of a liquid within a horizontal pipe. These factors intricately interact to determine whether the flow is laminar or turbulent and the overall pressure drop along the pipe length.
1. Reynolds Number (Re)
As already mentioned, the Reynolds number is the most critical parameter in determining the flow regime. It's calculated using the following formula:
Re = (ρVD)/μ
Where:
- ρ is the density of the liquid
- V is the average velocity of the liquid
- D is the diameter of the pipe
- μ is the dynamic viscosity of the liquid
A higher Reynolds number indicates a greater likelihood of turbulent flow.
2. Pipe Diameter (D)
The pipe diameter plays a significant role. Larger diameter pipes generally promote turbulent flow at lower velocities compared to smaller diameter pipes, due to increased inertia.
3. Fluid Properties (ρ and μ)
The density (ρ) and dynamic viscosity (μ) of the liquid directly influence the Reynolds number. High-density liquids are more prone to turbulent flow, while high-viscosity liquids tend to resist turbulence and favor laminar flow.
4. Pipe Roughness (ε)
The surface roughness of the pipe's inner walls influences frictional losses and can trigger the transition to turbulent flow at lower Reynolds numbers than predicted by theory for smooth pipes. A rougher pipe surface creates more resistance to flow and increases energy losses. This roughness is often characterized by the Darcy-Weisbach friction factor, which is empirically determined or calculated using equations like the Colebrook-White equation.
5. Liquid Velocity (V)
Increasing the liquid velocity increases the Reynolds number, making the transition to turbulent flow more likely.
Pressure Drop in Horizontal Pipes: Understanding the Losses
The pressure drop along a horizontal pipe is a consequence of frictional losses caused by the interaction between the liquid and the pipe walls. This pressure drop is crucial for designing piping systems and ensuring adequate flow rates.
Major Losses: Friction in the Pipe
Major losses represent the frictional energy losses due to the shear stress at the pipe wall. For laminar flow, the pressure drop can be accurately predicted using the Hagen-Poiseuille equation:
ΔP = (32μLV)/(D²)
Where:
- ΔP is the pressure drop
- μ is the dynamic viscosity
- L is the length of the pipe
- V is the average velocity
- D is the diameter of the pipe
For turbulent flow, the calculation becomes significantly more complex, often requiring the Darcy-Weisbach equation:
ΔP = f (L/D) (ρV²/2)
Where:
- f is the Darcy-Weisbach friction factor, a dimensionless number that depends on the Reynolds number and the pipe roughness.
The determination of the friction factor in turbulent flow often involves iterative methods or empirical correlations, such as the Moody chart.
Minor Losses: Fittings and Components
Beyond major losses, minor losses occur due to changes in pipe geometry, such as bends, valves, and fittings. These losses are often expressed as a head loss coefficient (K) multiplied by the velocity head (V²/2g):
Δh = K (V²/2g)
Where:
- Δh is the head loss
- K is the loss coefficient, which depends on the type and geometry of the fitting.
- g is the acceleration due to gravity.
These minor losses are often significant and should be considered in the overall pressure drop calculation.
Practical Applications and Implications
The understanding of liquid flow in horizontal pipes is crucial across numerous engineering disciplines:
- Water distribution systems: Designing efficient and reliable water supply networks requires accurate prediction of pressure drops to ensure adequate flow rates to consumers.
- Oil and gas pipelines: Transporting oil and gas over long distances necessitates careful consideration of pressure drops and flow regimes to optimize energy efficiency and avoid operational issues.
- Chemical processing: Many industrial processes involve the transport of fluids through pipes, and accurate flow modeling is essential for process optimization and safety.
- HVAC systems: Heating, ventilation, and air conditioning systems rely on the flow of liquids and gases through pipes.
- Medical devices: Certain medical devices, such as dialysis machines, involve precise fluid flow control within tubing systems.
Conclusion: A Complex Yet Essential Understanding
The seemingly simple scenario of a smoothly flowing liquid in a horizontal pipe unveils a complex interplay of fluid mechanics principles. Understanding the factors influencing flow regime (laminar or turbulent), accurate calculation of pressure drops considering major and minor losses, and the application of relevant equations are crucial for successful engineering design and efficient operation across various industries. Further exploration into computational fluid dynamics (CFD) offers powerful tools for analyzing complex flow scenarios and optimizing designs beyond the capabilities of simplified analytical models. This detailed understanding of fluid flow not only ensures efficient systems but also contributes to safety and optimal performance in numerous applications.
Latest Posts
Related Post
Thank you for visiting our website which covers about A Horizontal Pipe Carries A Smoothly Flowing Liquid . We hope the information provided has been useful to you. Feel free to contact us if you have any questions or need further assistance. See you next time and don't miss to bookmark.