A Cpk Index Of 1.00 Equates To What Defect Rate
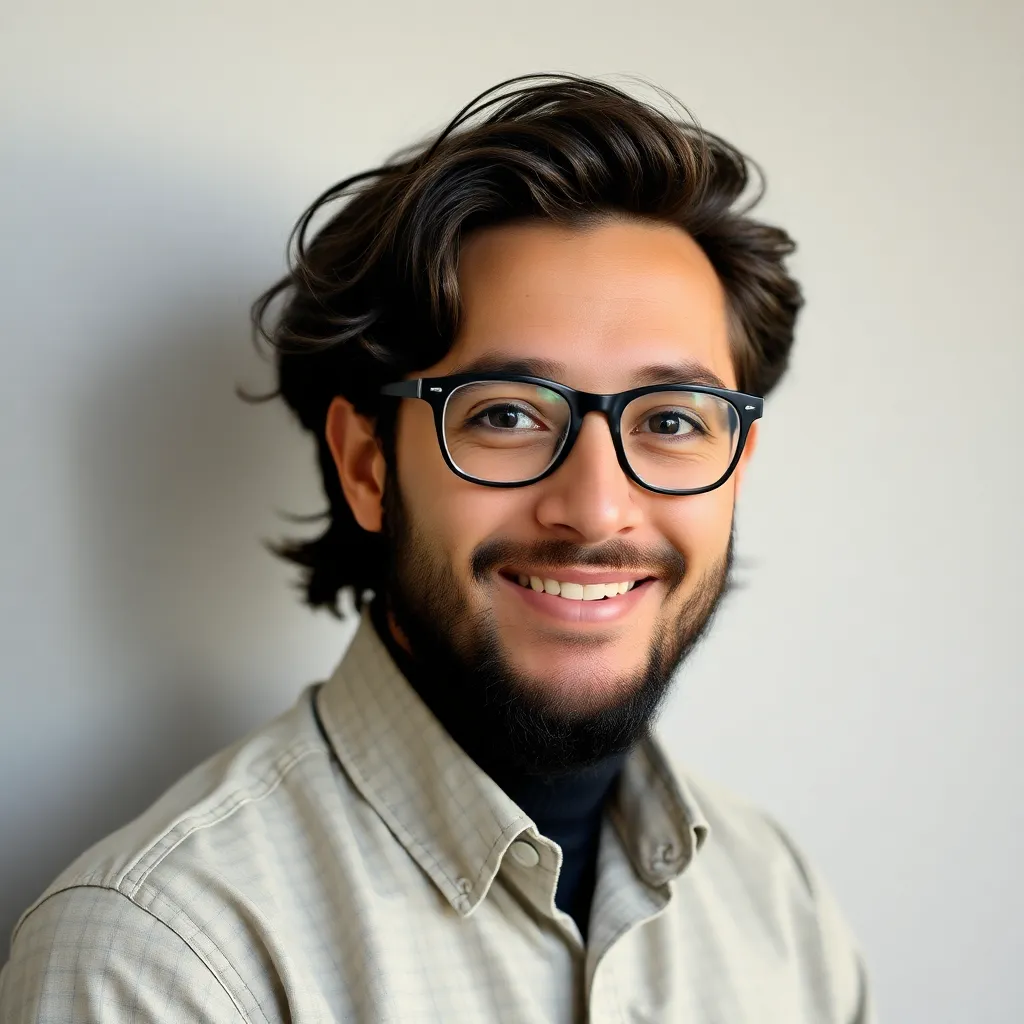
Holbox
May 12, 2025 · 6 min read
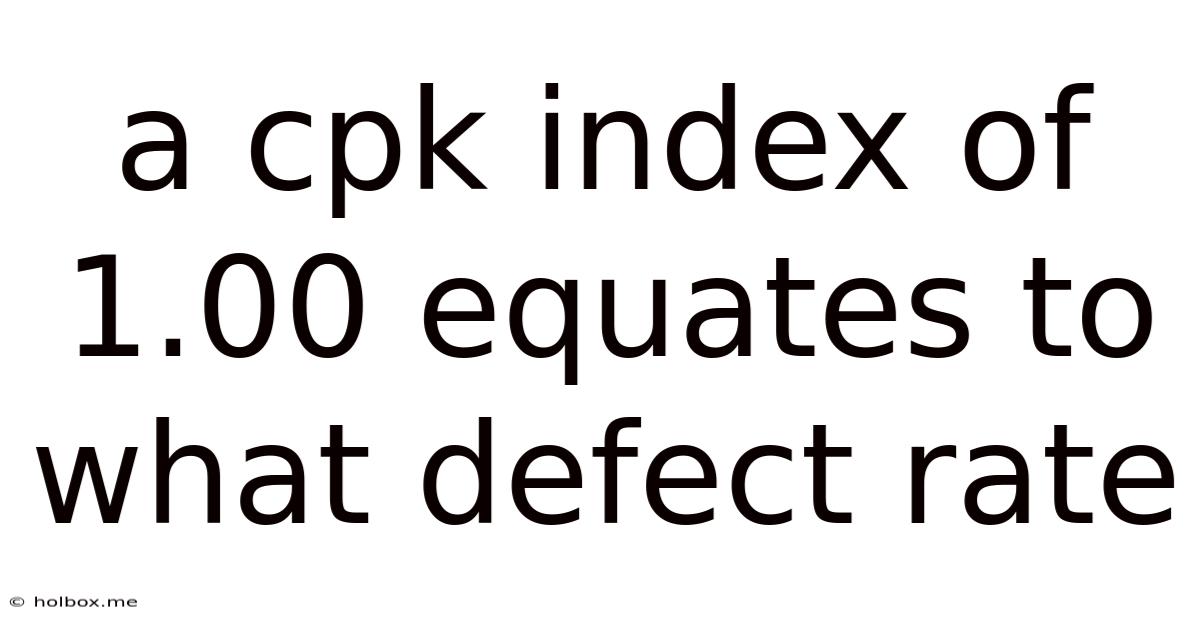
Table of Contents
- A Cpk Index Of 1.00 Equates To What Defect Rate
- Table of Contents
- A Cpk Index of 1.00 Equates to What Defect Rate? Understanding Process Capability and its Implications
- Understanding Cpk: A Measure of Process Capability
- The Role of the Normal Distribution
- Calculating Defect Rate from Cpk = 1.00
- Impact of Non-Normality
- Improving Cpk and Reducing Defect Rates
- Strategies for Cpk Improvement:
- Cpk, PPM, and Six Sigma
- Real-World Implications and Considerations
- Conclusion: More Than Just a Number
- Latest Posts
- Related Post
A Cpk Index of 1.00 Equates to What Defect Rate? Understanding Process Capability and its Implications
The world of manufacturing and quality control hinges on understanding process capability. A crucial metric in this realm is the Cpk index (Process Capability index), which quantifies how well a process meets pre-defined specifications. A common question arises: What defect rate does a Cpk index of 1.00 represent? The answer isn't a simple number, but rather a range and a deeper dive into the intricacies of statistical process control (SPC). This article will explore the relationship between Cpk and defect rates, offering insights into its interpretation and implications for manufacturing processes.
Understanding Cpk: A Measure of Process Capability
Before delving into the defect rate associated with a Cpk of 1.00, let's clarify what Cpk represents. Cpk is a statistical measure that considers both the process mean and its variability relative to the upper and lower specification limits (USL and LSL). It's a crucial tool in assessing process capability, indicating how well a process is centered and how consistent its output is.
A Cpk of 1.00 signifies that the process is capable of producing outputs within the specification limits, with a relatively high probability of producing defects. However, it's essential to remember that this is a simplified interpretation. The actual defect rate depends on the underlying process distribution, typically assumed to be normal.
The Role of the Normal Distribution
The calculation of defect rates from Cpk relies heavily on the assumption of a normal distribution of the process output. The normal distribution, with its bell curve, allows us to calculate probabilities of defects falling outside the specification limits using statistical tables or software. If the process data significantly deviates from a normal distribution, the calculated defect rate based on Cpk might not be accurate. In such cases, other statistical methods or transformations may be needed to accurately assess process capability.
Calculating Defect Rate from Cpk = 1.00
A Cpk of 1.00 corresponds to a Z-score of 1.00 on either side of the mean. Using standard normal distribution tables or statistical software, we can find that the probability of a single data point falling outside of ±1 standard deviation from the mean is approximately 31.74%.
This means that with a Cpk of 1.00, the process is expected to generate a defect rate of approximately 31.74%. This is often stated as 31.73% or 31.73 ppm (parts per million).
It’s crucial to note that this is a theoretical calculation based on a perfectly normal distribution. Real-world processes are rarely perfectly normal. Variations in the process, unexpected shifts in the mean, or non-normal distributions can significantly affect the actual defect rate.
Impact of Non-Normality
Many manufacturing processes exhibit non-normal distributions. The presence of outliers, skewness, or other deviations from normality can lead to inaccurate defect rate predictions based solely on the Cpk value. Techniques like data transformation or the use of non-parametric methods might be necessary for a more accurate assessment in such cases.
The key takeaway is that while a Cpk of 1.00 suggests a process capable of meeting specifications, it does not guarantee a zero or even low defect rate. The actual defect rate can be substantially higher than the theoretical value if the underlying distribution is significantly non-normal.
Improving Cpk and Reducing Defect Rates
A Cpk value of 1.00 is generally considered insufficient for many industries. While it might seem acceptable to produce some defects, most organizations aim for a much higher level of process capability. Improving the Cpk value requires addressing both the process mean and its variability.
Strategies for Cpk Improvement:
-
Process Centering: If the process mean is shifted towards one of the specification limits, adjusting the process parameters to center the mean will significantly improve Cpk. This reduces the probability of generating defects close to the specification limit.
-
Reducing Variability: This is often the more challenging aspect. Identifying and eliminating sources of variation through techniques such as root cause analysis (RCA), design of experiments (DOE), and process optimization are crucial for decreasing the process standard deviation. Reducing variability leads to a higher Cpk value.
-
Tightening Specifications: In some cases, reviewing and tightening the specification limits might be an option. This could improve Cpk by making it easier to meet the requirements, but only if the tightening aligns with the product’s functional requirements. It’s essential to avoid arbitrarily tightening specifications, potentially compromising product functionality.
-
Statistical Process Control (SPC): Implementing SPC charts, such as control charts, allows for the ongoing monitoring of the process. Early detection of process shifts or instability enables timely corrective actions, preventing a large number of defects.
Cpk, PPM, and Six Sigma
The relationship between Cpk, parts per million (PPM) defect rate, and Six Sigma methodologies is often closely examined. The Six Sigma methodology aims for extremely low defect rates, typically less than 3.4 PPM. To achieve this, a significantly higher Cpk value is typically required.
A general rule of thumb for achieving Six Sigma performance is a Cpk of at least 1.5. This is because a Cpk of 1.5 corresponds to a Z-score of 3, meaning the process mean is 3 standard deviations away from the nearest specification limit. The probability of a defect falling outside ±3 standard deviations is significantly lower than that of ±1 standard deviation.
Real-World Implications and Considerations
In practice, interpreting a Cpk of 1.00 requires careful consideration of several factors:
-
Cost of Defects: The financial implications of producing defects must be weighed against the cost of improving the process. If the cost of defects is low, a Cpk of 1.00 might be acceptable. However, for high-cost defects (e.g., medical devices, aerospace components), a significantly higher Cpk is often required.
-
Industry Standards: Certain industries have stricter requirements for Cpk values than others. Regulatory bodies and industry best practices often dictate acceptable levels of process capability, influencing the acceptable Cpk value.
-
Product Specifications: The tolerance limits for product specifications can vary widely. Wider tolerances allow for a higher acceptable Cpk value, as defects are less likely to impact the product's functionality.
-
Customer Requirements: Ultimately, the acceptable Cpk value is often influenced by customer requirements. Meeting customer expectations for quality and reliability necessitates the attainment of an appropriate Cpk value, exceeding minimum industry standards.
Conclusion: More Than Just a Number
A Cpk index of 1.00 indicates a process that's marginally capable of meeting specifications, theoretically corresponding to approximately a 31.74% defect rate under ideal conditions. However, this is a simplified interpretation. The actual defect rate can vary significantly based on the process distribution, cost of defects, industry standards, and customer requirements. Simply focusing on the Cpk value alone is insufficient for a complete understanding of process capability. A thorough analysis of the process, including assessment of the underlying data distribution and consideration of real-world factors, is essential for accurate interpretation and effective improvement strategies. Improving process capability often involves focusing on reducing variability and centering the process mean to achieve a higher Cpk value and significantly lower defect rates. Remember, achieving higher Cpk values often leads to improved product quality, reduced costs, and increased customer satisfaction.
Latest Posts
Related Post
Thank you for visiting our website which covers about A Cpk Index Of 1.00 Equates To What Defect Rate . We hope the information provided has been useful to you. Feel free to contact us if you have any questions or need further assistance. See you next time and don't miss to bookmark.