A Company Produces X Units Of A Product Per Month
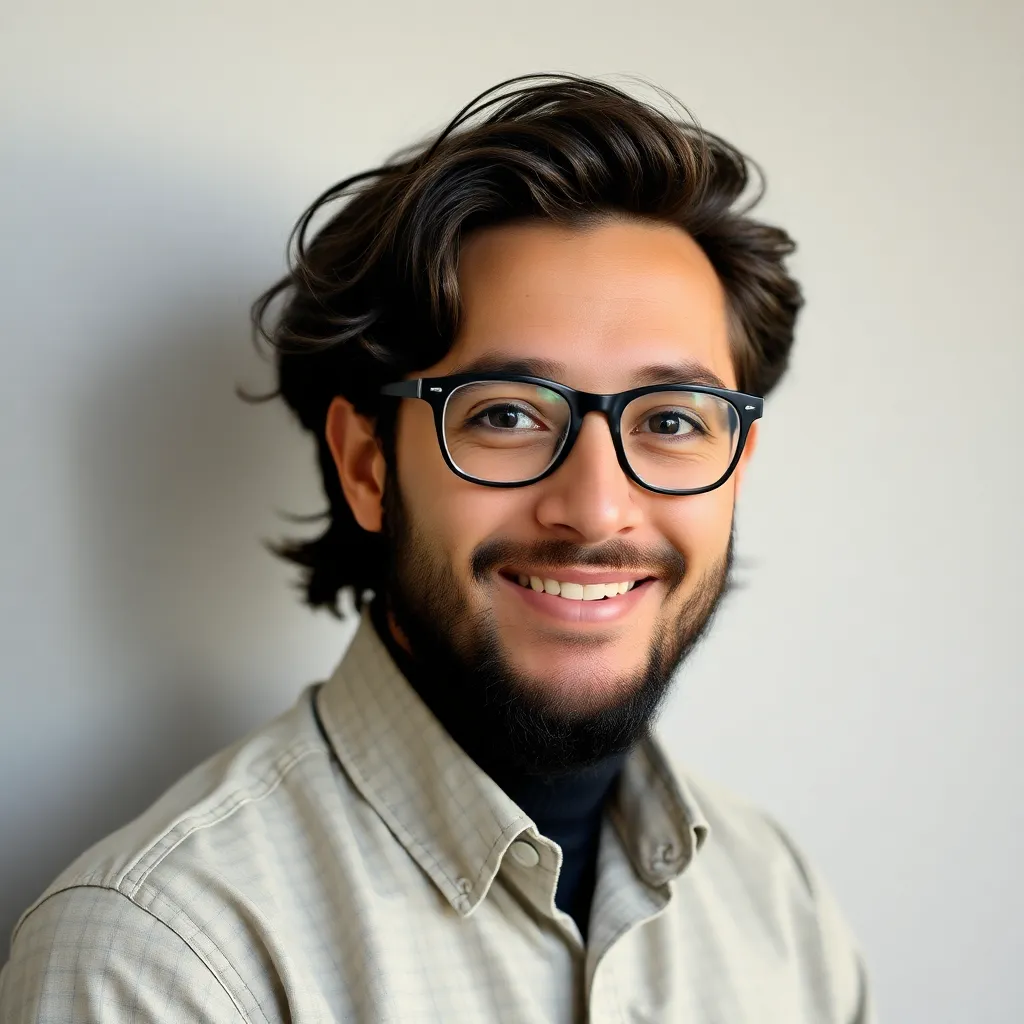
Holbox
Apr 26, 2025 · 5 min read
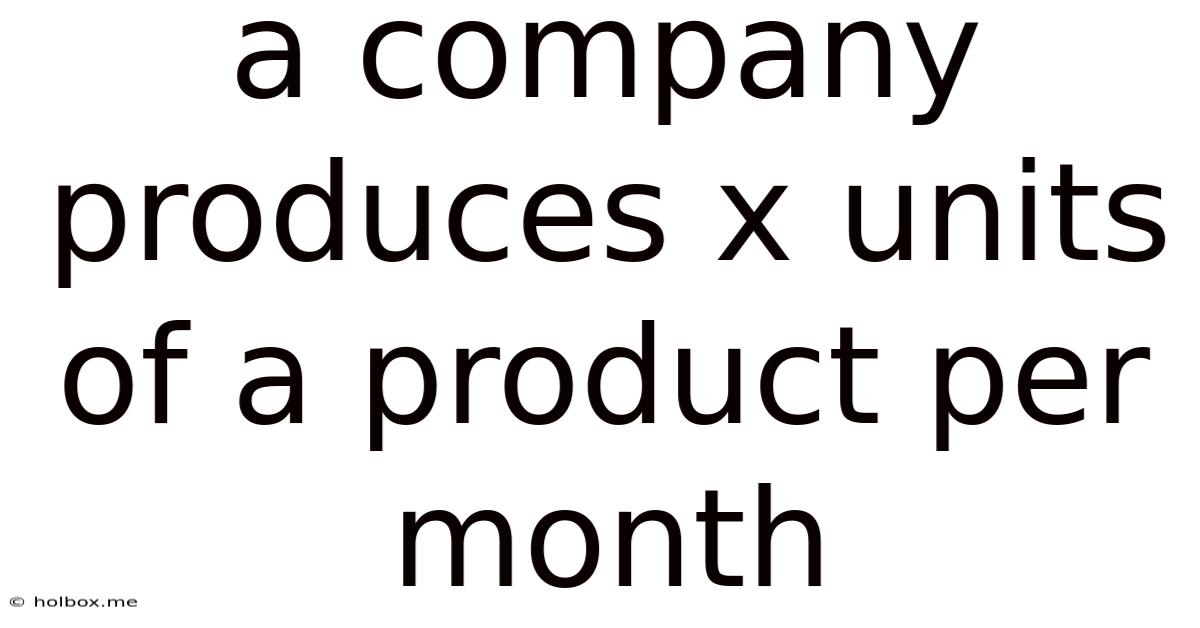
Table of Contents
- A Company Produces X Units Of A Product Per Month
- Table of Contents
- A Company Produces X Units of a Product Per Month: A Deep Dive into Production Optimization
- Understanding the "X" Factor: Production Volume and its Determinants
- 1. Production Capacity: The Physical Limits
- 2. Market Demand: The Driving Force
- Optimizing Production for Maximum Efficiency and Profitability
- 1. Lean Manufacturing Principles: Minimizing Waste
- 2. Just-in-Time (JIT) Inventory Management: Reducing Inventory Costs
- 3. Automation and Technological Advancements: Enhancing Efficiency
- 4. Quality Control and Continuous Improvement: Reducing Defects and Enhancing Product Quality
- 5. Supply Chain Management: Ensuring Timely Delivery of Raw Materials
- The Broader Implications of Production Volume: Market Dynamics and Economic Impact
- 1. Profitability and Revenue Generation: The Bottom Line
- 2. Market Share and Competitive Advantage: Maintaining Position in the Market
- 3. Job Creation and Economic Growth: Contributing to the Economy
- Conclusion: The Dynamic Nature of "X"
- Latest Posts
- Latest Posts
- Related Post
A Company Produces X Units of a Product Per Month: A Deep Dive into Production Optimization
The statement "a company produces X units of a product per month" is deceptively simple. Behind this seemingly straightforward sentence lies a complex interplay of factors influencing profitability, efficiency, and long-term sustainability. This article will explore the numerous aspects surrounding a company's monthly production output, delving into the intricacies of production planning, optimization strategies, and the wider economic and market implications.
Understanding the "X" Factor: Production Volume and its Determinants
The number "X" isn't just a random variable; it's a critical metric reflecting a company's production capacity and market demand. Several key factors determine this production volume:
1. Production Capacity: The Physical Limits
- Manufacturing Facilities: The size, layout, and technological advancement of the production facilities directly limit the maximum number of units a company can produce. A larger facility with state-of-the-art machinery will naturally have a higher production capacity than a smaller, outdated one.
- Equipment and Machinery: The efficiency and reliability of the equipment used significantly impact output. Downtime due to maintenance, breakdowns, or insufficient capacity bottlenecks the entire production process.
- Labor Force: The skill, training, and number of employees directly influence output. A well-trained, efficient workforce can achieve higher productivity compared to a less skilled or understaffed team.
- Raw Materials and Supplies: The availability and consistent supply of raw materials are critical. Shortages or delays in the supply chain can dramatically reduce production volume.
2. Market Demand: The Driving Force
- Consumer Preferences: Fluctuations in consumer demand based on trends, seasonality, and marketing campaigns directly influence production needs. A sudden surge in demand requires immediate scaling up, while a decrease necessitates adjustments to avoid overstocking.
- Competitive Landscape: The actions of competitors, including pricing strategies and product innovation, impact a company's market share and consequently its production volume. Intense competition necessitates efficient production to maintain competitiveness.
- Economic Conditions: Macroeconomic factors like inflation, recession, and unemployment significantly influence consumer spending and, thus, demand for products. Companies need to adjust production plans based on these economic indicators.
- Sales Forecasts and Predictions: Accurate sales forecasting is crucial for effective production planning. Sophisticated forecasting models analyze historical data, market trends, and external factors to predict future demand, optimizing production accordingly.
Optimizing Production for Maximum Efficiency and Profitability
Producing "X" units efficiently is not simply about meeting a target; it's about optimizing the entire production process to maximize profitability and minimize waste. This involves implementing several strategies:
1. Lean Manufacturing Principles: Minimizing Waste
Lean manufacturing focuses on eliminating waste throughout the production process. This includes:
- Overproduction: Producing more than needed leads to excess inventory, storage costs, and potential obsolescence.
- Waiting: Delays in material handling, machine setups, or process steps lead to idle time and reduced efficiency.
- Transportation: Inefficient material movement increases handling time and risk of damage.
- Inventory: Excess inventory ties up capital and increases storage costs.
- Motion: Unnecessary movements by workers increase labor costs and reduce efficiency.
- Over-processing: Performing more work than is necessary increases costs and doesn't add value.
- Defects: Producing defective products results in rework, scrap, and customer dissatisfaction.
Implementing lean principles requires careful analysis of the entire production process, identifying and eliminating these wastes. This may involve streamlining workflows, optimizing material flow, improving employee training, and implementing quality control measures.
2. Just-in-Time (JIT) Inventory Management: Reducing Inventory Costs
JIT inventory management minimizes inventory levels by procuring and producing materials only when needed. This reduces storage costs, minimizes the risk of obsolescence, and improves cash flow. However, it requires a highly reliable supply chain and effective forecasting to avoid stockouts.
3. Automation and Technological Advancements: Enhancing Efficiency
Automating various stages of the production process can significantly increase efficiency and reduce labor costs. Robotics, automated guided vehicles (AGVs), and advanced manufacturing technologies enhance speed, precision, and consistency, allowing companies to produce more units with fewer resources.
4. Quality Control and Continuous Improvement: Reducing Defects and Enhancing Product Quality
Rigorous quality control measures at each stage of the production process are vital. This includes implementing inspection procedures, using statistical process control (SPC) techniques, and continuously monitoring for defects. A culture of continuous improvement, where employees are encouraged to identify and suggest improvements, is crucial for long-term efficiency.
5. Supply Chain Management: Ensuring Timely Delivery of Raw Materials
Efficient supply chain management is paramount for maintaining consistent production. This involves establishing strong relationships with suppliers, optimizing logistics, and implementing robust inventory management systems to ensure a timely and reliable supply of raw materials.
The Broader Implications of Production Volume: Market Dynamics and Economic Impact
The "X" units produced per month don't exist in isolation. They have significant implications for the company's overall performance and broader economic context:
1. Profitability and Revenue Generation: The Bottom Line
Production volume directly impacts a company's revenue and profitability. Producing more units generally leads to higher revenue, provided the products are sold at a profitable price. However, overproduction can lead to losses if the excess inventory cannot be sold.
2. Market Share and Competitive Advantage: Maintaining Position in the Market
The production volume influences a company's market share. Higher production capacity allows a company to meet increased demand, potentially capturing a larger market share. Efficient production leads to lower costs, enabling competitive pricing and improved profitability.
3. Job Creation and Economic Growth: Contributing to the Economy
A company's production volume affects employment levels. Increased production generally requires a larger workforce, leading to job creation and stimulating economic growth. The company's economic contribution extends beyond direct employment, encompassing related industries involved in the supply chain.
Conclusion: The Dynamic Nature of "X"
The statement "a company produces X units of a product per month" is far more than a simple numerical expression. It represents a complex interplay of production capacity, market demand, and optimization strategies. Understanding these factors is crucial for companies aiming to achieve efficient production, maximize profitability, and maintain a competitive edge in the ever-evolving marketplace. Continuous monitoring, adaptation, and improvement are essential for managing and optimizing this critical variable, ensuring long-term success and sustainability. The number "X" is not static; it’s a dynamic metric that constantly adapts to the changing dynamics of the market and the evolving capabilities of the company. The key to success lies in the ability to effectively manage and optimize this variable to align with business goals and market realities.
Latest Posts
Latest Posts
-
Scholarly Review Journals Will Always Be Reviewed By Blank
May 12, 2025
-
What Is The Overarching Principle Of Object Relations Theory
May 12, 2025
-
Amoeba Sisters Video Recap Biomagnification Answers Pdf
May 12, 2025
-
Core Competencies And Competitive Capabilities Are Usually
May 12, 2025
-
Which Of The Following Best Describes The Structures Of Carbohydrates
May 12, 2025
Related Post
Thank you for visiting our website which covers about A Company Produces X Units Of A Product Per Month . We hope the information provided has been useful to you. Feel free to contact us if you have any questions or need further assistance. See you next time and don't miss to bookmark.