2. Compute The Average Manufacturing Cost Per Drum Set.
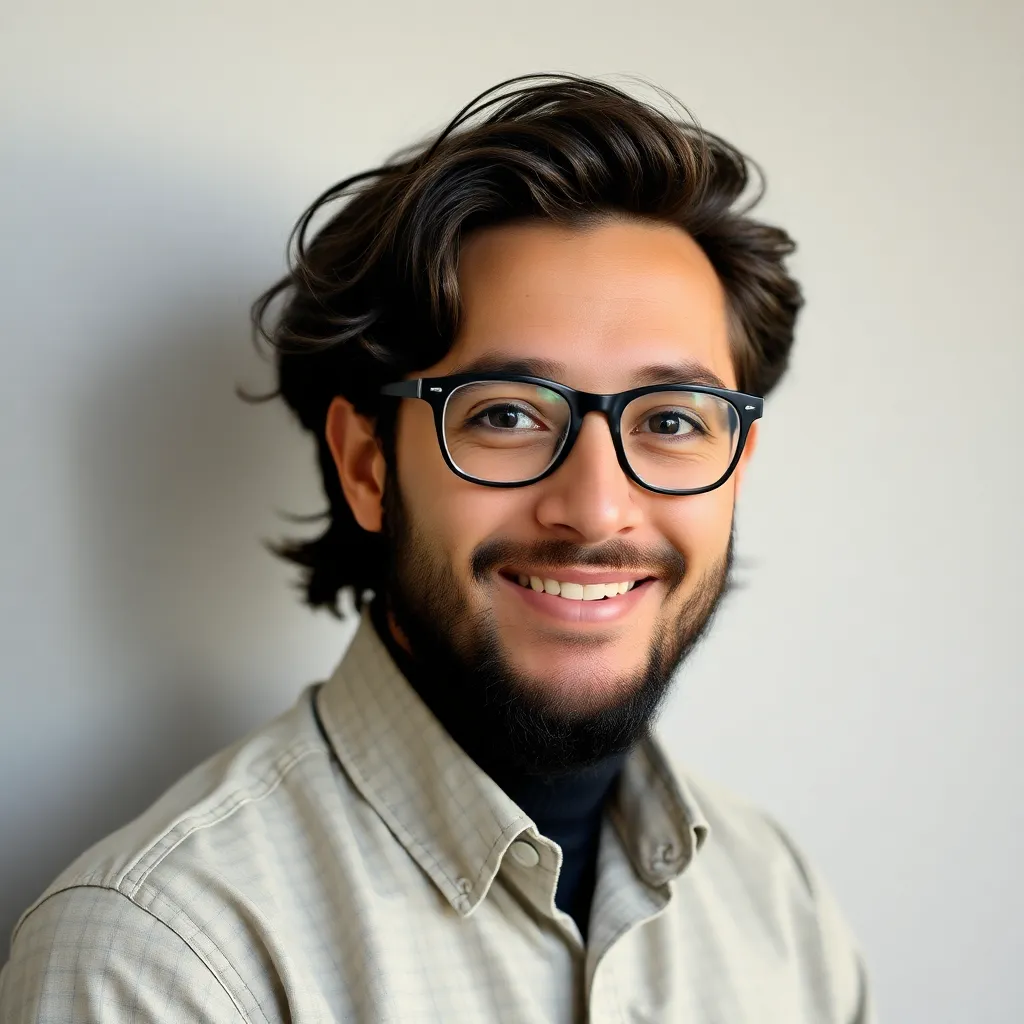
Holbox
Apr 15, 2025 · 6 min read

Table of Contents
- 2. Compute The Average Manufacturing Cost Per Drum Set.
- Table of Contents
- Computing the Average Manufacturing Cost Per Drum Set: A Comprehensive Guide
- Understanding Cost Components
- 1. Direct Materials Costs
- 2. Direct Labor Costs
- 3. Manufacturing Overhead Costs
- Calculating the Average Manufacturing Cost
- Refining Your Cost Calculation: Strategies for Accuracy and Optimization
- Beyond the Numbers: Pricing and Profitability
- Conclusion
- Latest Posts
- Latest Posts
- Related Post
Computing the Average Manufacturing Cost Per Drum Set: A Comprehensive Guide
Calculating the average manufacturing cost per drum set is crucial for any drum manufacturing business aiming for profitability and competitive pricing. This process goes beyond simply adding up all expenses; it requires a detailed breakdown of direct and indirect costs, accurate cost accounting, and a keen understanding of your production process. This comprehensive guide will walk you through the steps involved, offering insights into various cost categories and strategies for optimization.
Understanding Cost Components
Before diving into the calculation, it's essential to grasp the different types of costs involved in drum set manufacturing:
1. Direct Materials Costs
These are the raw materials directly used in creating a drum set. This includes:
- Wood: Different types of wood (maple, birch, mahogany) contribute significantly to the cost, varying in price and quality. Consider the cost per board foot or cubic meter, factoring in waste and potential defects.
- Hardware: This encompasses lugs, tension rods, bass drum claws, cymbal holders, and other metal components. Prices vary depending on material (steel, zinc alloy), finish (chrome, nickel), and supplier.
- Heads: Drum heads (batter and resonant) are crucial. Cost depends on the brand, size, material (mylar, coated mylar), and construction.
- Finishes: Lacquer, stain, or other finishes impact the final cost, influenced by the type and number of coats.
- Other Components: This category includes things like gaskets, felt washers, mounting hardware, and any unique features like specialized hardware or inlays.
Calculating Direct Materials Cost: For each component, multiply the quantity used per drum set by its unit cost. Summing these individual costs gives you the total direct materials cost per drum set.
2. Direct Labor Costs
This refers to the wages and benefits paid to workers directly involved in manufacturing the drum sets. This includes:
- Assembly Workers: The time spent assembling the shells, mounting hardware, and tuning the drums.
- Finishers: The labor involved in sanding, finishing, and polishing the shells.
- Inspectors: Quality control personnel ensuring each drum set meets standards.
Calculating Direct Labor Costs: Determine the hourly wage (including benefits) for each worker involved in the process. Then, measure the time spent by each worker on a single drum set. Multiply the time by the hourly wage for each worker, and sum these figures to obtain the total direct labor cost per drum set.
3. Manufacturing Overhead Costs
These are indirect costs not directly traceable to individual drum sets but essential for production. This includes:
- Factory Rent and Utilities: Costs associated with the manufacturing facility.
- Equipment Depreciation: The gradual loss of value of machinery used in production (e.g., lathes, sanders, drum shell-forming machines).
- Maintenance and Repairs: Costs associated with maintaining and repairing manufacturing equipment.
- Factory Supplies: Consumables used in the production process, like sandpaper, adhesives, cleaning solvents.
- Insurance: Insurance premiums for the factory and equipment.
- Supervision: Salaries of supervisors and managers overseeing production.
- Quality Control: Costs associated with testing and inspecting materials and finished products beyond direct labor.
Calculating Manufacturing Overhead Costs: This can be done using different methods, including:
- Traditional Costing: Allocates overhead based on a predetermined overhead rate (e.g., based on direct labor hours or machine hours). This method involves estimating total overhead costs for a period and dividing by the total direct labor hours or machine hours. The resulting overhead rate is then multiplied by the direct labor hours or machine hours used for each drum set.
- Activity-Based Costing (ABC): A more sophisticated method that assigns overhead costs based on specific activities involved in production. This offers greater accuracy but requires more detailed data collection and analysis. It identifies cost pools (e.g., setting up machines, inspecting drums) and assigns costs based on the activities used per drum set.
Calculating the Average Manufacturing Cost
Once you've determined the direct materials, direct labor, and manufacturing overhead costs, you can calculate the average manufacturing cost per drum set:
Average Manufacturing Cost = Direct Materials Cost + Direct Labor Cost + Manufacturing Overhead Cost
This calculation should be performed on a per-drum-set basis to reflect the actual cost of producing each unit.
Example:
Let's assume the following costs for a specific drum set model:
- Direct Materials Cost: $300
- Direct Labor Cost: $150
- Manufacturing Overhead Cost (calculated using traditional costing): $75
Average Manufacturing Cost = $300 + $150 + $75 = $525
Therefore, the average manufacturing cost for this particular drum set model is $525.
Refining Your Cost Calculation: Strategies for Accuracy and Optimization
The accuracy of your average manufacturing cost calculation is paramount. Here are some strategies to improve precision and identify areas for cost optimization:
- Accurate Cost Tracking: Implement a robust cost accounting system to meticulously track all expenses related to production. Use spreadsheets, dedicated accounting software, or enterprise resource planning (ERP) systems.
- Regular Cost Reviews: Conduct regular reviews of your cost structure to identify trends, potential inefficiencies, and areas for improvement. Market fluctuations in raw materials necessitate ongoing monitoring.
- Process Improvement: Analyze your production process to identify bottlenecks or inefficiencies. Streamlining workflows and improving efficiency can significantly reduce costs.
- Negotiation with Suppliers: Develop strong relationships with suppliers to negotiate favorable pricing on raw materials and components. Bulk purchasing can often lead to discounts.
- Waste Reduction: Implement strategies to minimize waste in the production process. This includes optimizing material usage, improving quality control to reduce defects, and recycling or repurposing scrap materials.
- Automation: Explore opportunities to automate certain aspects of the manufacturing process to increase efficiency and reduce labor costs.
- Inventory Management: Implement an effective inventory management system to minimize storage costs and prevent spoilage or obsolescence of raw materials. Just-in-time inventory management can be particularly effective.
Beyond the Numbers: Pricing and Profitability
The average manufacturing cost is just one piece of the puzzle. You'll need to consider other factors when setting your selling price:
- Market Research: Understand your target market and competitive pricing to determine a price point that is both attractive to customers and profitable for your business.
- Profit Margin: Determine the desired profit margin you want to achieve on each drum set. This will influence your pricing strategy. Consider factors like overhead costs unrelated to manufacturing, marketing and distribution, and desired return on investment.
- Pricing Strategies: Explore various pricing strategies such as cost-plus pricing, value-based pricing, or competitive pricing to find the optimal pricing approach for your business.
Conclusion
Calculating the average manufacturing cost per drum set requires a meticulous approach, encompassing a detailed breakdown of direct and indirect costs. Regular review, process optimization, and strategic cost management are crucial for maintaining profitability and competitiveness. By implementing the strategies outlined in this guide, drum manufacturers can gain valuable insights into their cost structure, allowing them to make informed decisions regarding pricing, production, and overall business strategy. Remember that this is an ongoing process, requiring continuous monitoring and adaptation to market changes and operational improvements. Consistent accuracy in cost tracking will lead to more effective pricing decisions and sustainable growth.
Latest Posts
Latest Posts
-
Short Term Considerations In Determining Capacity Requirements Include
Apr 23, 2025
-
Select Each Graph That Shows A Function And Its Inverse
Apr 23, 2025
-
Maximum Capacity Commonly Refers To The Upper Limit On
Apr 23, 2025
-
A Companys Culture Is In Part Defined And Identified By
Apr 23, 2025
-
What Is Recourse As It Relates To Selling Receivables
Apr 23, 2025
Related Post
Thank you for visiting our website which covers about 2. Compute The Average Manufacturing Cost Per Drum Set. . We hope the information provided has been useful to you. Feel free to contact us if you have any questions or need further assistance. See you next time and don't miss to bookmark.